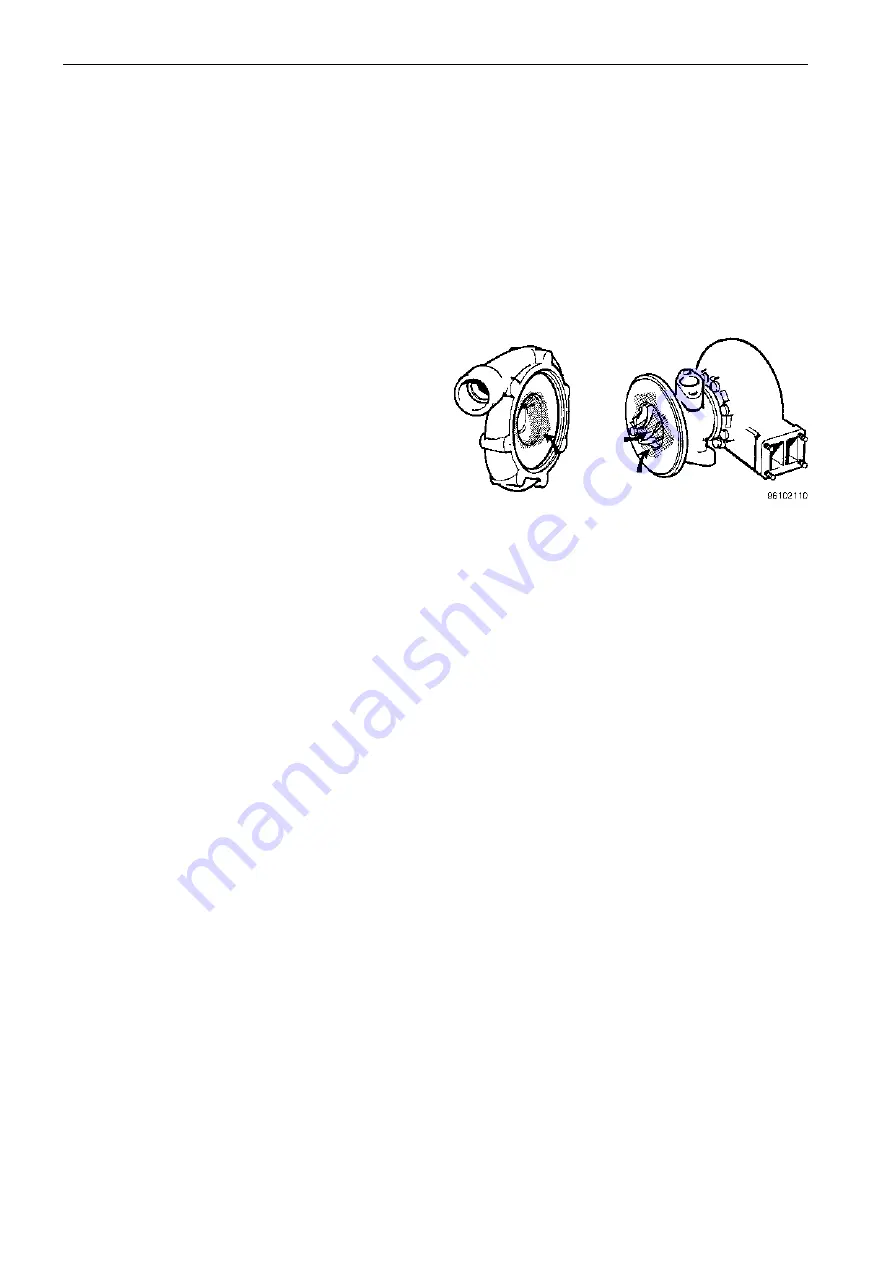
Service procedures - intake and exhaust systems
Group 22
112
Rectifying low boost pressure
1.
Tightness of seals, inlet and exhaust manifolds.
It is essential that the hose between the turbocharger and
the inlet manifold is not cracked or is inadequately clamped.
In addition to a loss in boost pressure, leakage can also
cause a high exhaust gas temperature which will result in
excessive stresses on the exhaust pipe, turbo, valves and
piston rings.
An exhaust system operating with too large a counter pres-
sure reduces boost pressure, gives a lower engine output
and increases exhaust temperature with a related risk of
burnt valves and turbo failure.
When an exhaust system has been rebuilt the back pres-
sure must always be checked in accordance with the in-
structions given. See next page ”Checking exhaust back
pressure”
The following demands must be met when converting an ex-
haust system:
A.
The diameter of the connecting pipe must be 1/2-1" larg-
er than the pipe to which it is to be connected.
B.
The transition between the existing pipe, to which con-
nection is being made, and the connecting pipe must not
be abrupt. It should be tapered, the taper being about
180 mm long.
C.
The pipe elbows should have as large a radius as pos-
sible. ”Pleating” should be avoided.
2.
Air filter
Check that the air filters are not blocked and that the correct
filters are being used. The indicator on the air filter inlet pipe
must not show red. Replace the filters when necessary.
3.
Accelerator linkage
Check that the accelerator linkage provides full travel of the
injection pump arm.
4.
Turbocharger
Check if the rotor shaft is sluggish or if the turbine wheel and
compressor wheel chafe against their housings. Turn the
wheel at first with a slight pressure, and when with a slight
axial pull. If the wheel is sluggish, the turbocharger must be
immediately replaced or reconditioned. Check the wheel for
damage.
In the event of daily operation in dusty or oily air, regular
cleaning of the compressor housing and compressor wheel
is recommended. Fouled compressor parts can result in low
boost pressure.
The compressor parts can be cleaned with the unit fitted as
follows:
Remove the compressor housing. Clean the compressor
housing, compressor wheel and the end head in kerosene or
the like. Fit the compressor housing and measure the boost
pressure again.
5.
Injection pump
Check the following:
Governing, injection angle, calibration, fast idle, smoke elimi-
nator diaphragm and triggering point, curve plate setting and
sealing.
6.
Feed pressure
Check that fuel leakage does not occur and that the pump
provides the correct feed pressure.
7.
Delivery pipes
Check that the pipes are of the correct dimension and that
the holes are not damaged.
8.
Injectors
Check the markings, opening pressure, spray pattern and
that the holes are not faulty or blocked.
9.
Engine condition
Check the compression pressure and the valve clearance of
the engine.
If the boost pressure remains unsatisfactory once all these
points have been checked and approved, the turbocharger
should be reconditioned or replaced.
Summary of Contents for TAD1630G
Page 1: ...Workshop manual TAD1630G GE P V TAD1631G GE TID162AP TWD1620G GH TWD1630G GE P V TD164KAE ...
Page 2: ......
Page 18: ...Design and Function Group 21 16 Engine Design and Function ...
Page 80: ...Service procedures engine Group 21 78 Application of sealant to cylinder block ...
Page 162: ...160 ...
Page 164: ...7742302 English 10 2002 ...