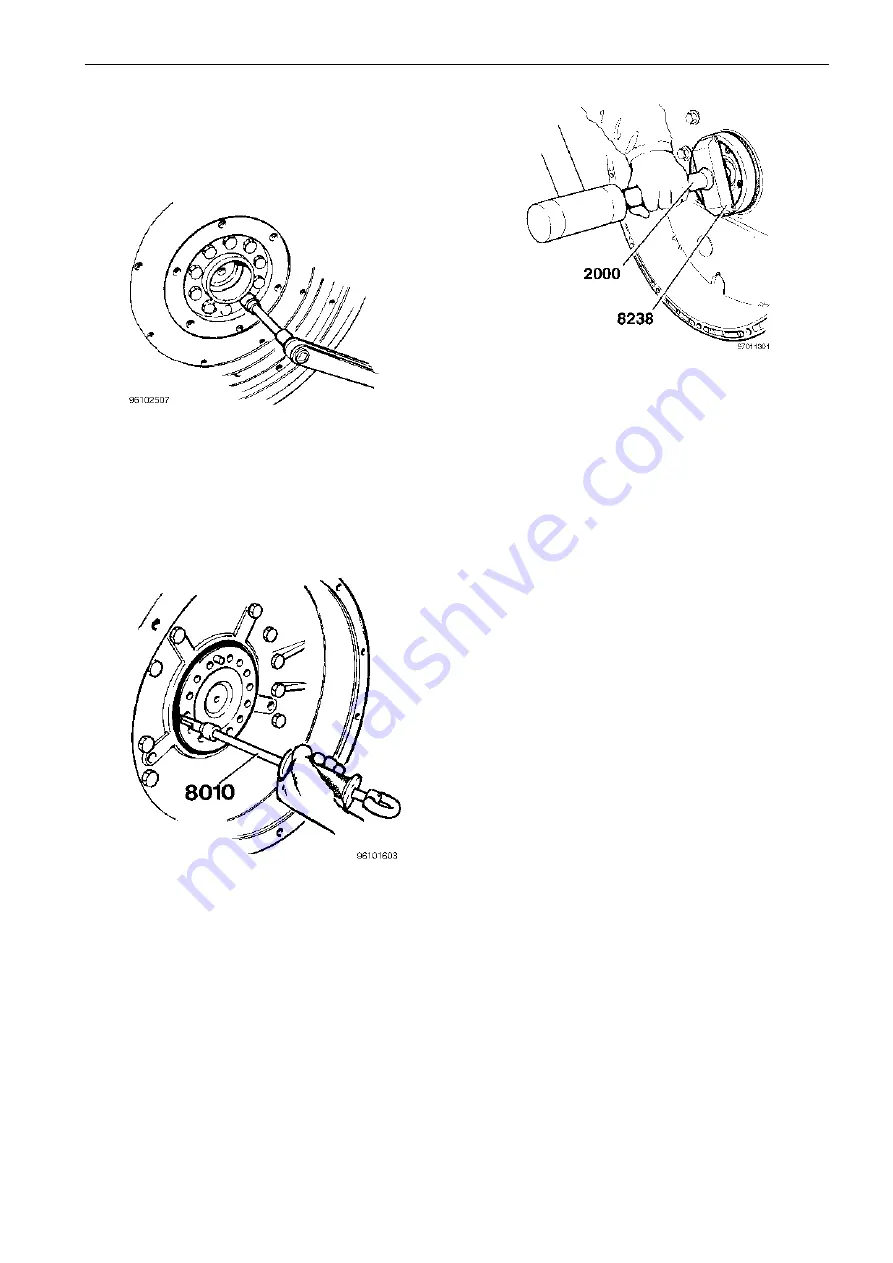
Group 21
Service procedures - engine
75
Crankshaft seal, rear,
replacing
Special tools: 999 2000, 999 3590, 999 8010, 999 8238
1
Remove the flywheel bolts.
2
Fit two bolts and lift out the flywheel.
3
Knock out the crankshaft seal using tool 999 8010.
4
Clean the seat of the sealing ring in the flywheel casing.
5
Apply sealant to the outer edge of the sealing ring and oil the
inner edge of the sealing ring before fitting it with tool 999
8238 and handle 999 2000.
6
Lift the flywheel into position. Refit the bolts.
7
Block the flywheel using cranking tool 999 3590.
8
Torque the flywheel bolts to 260 Nm (191.8 ft-lb).
Summary of Contents for TAD1630G
Page 1: ...Workshop manual TAD1630G GE P V TAD1631G GE TID162AP TWD1620G GH TWD1630G GE P V TD164KAE ...
Page 2: ......
Page 18: ...Design and Function Group 21 16 Engine Design and Function ...
Page 80: ...Service procedures engine Group 21 78 Application of sealant to cylinder block ...
Page 162: ...160 ...
Page 164: ...7742302 English 10 2002 ...