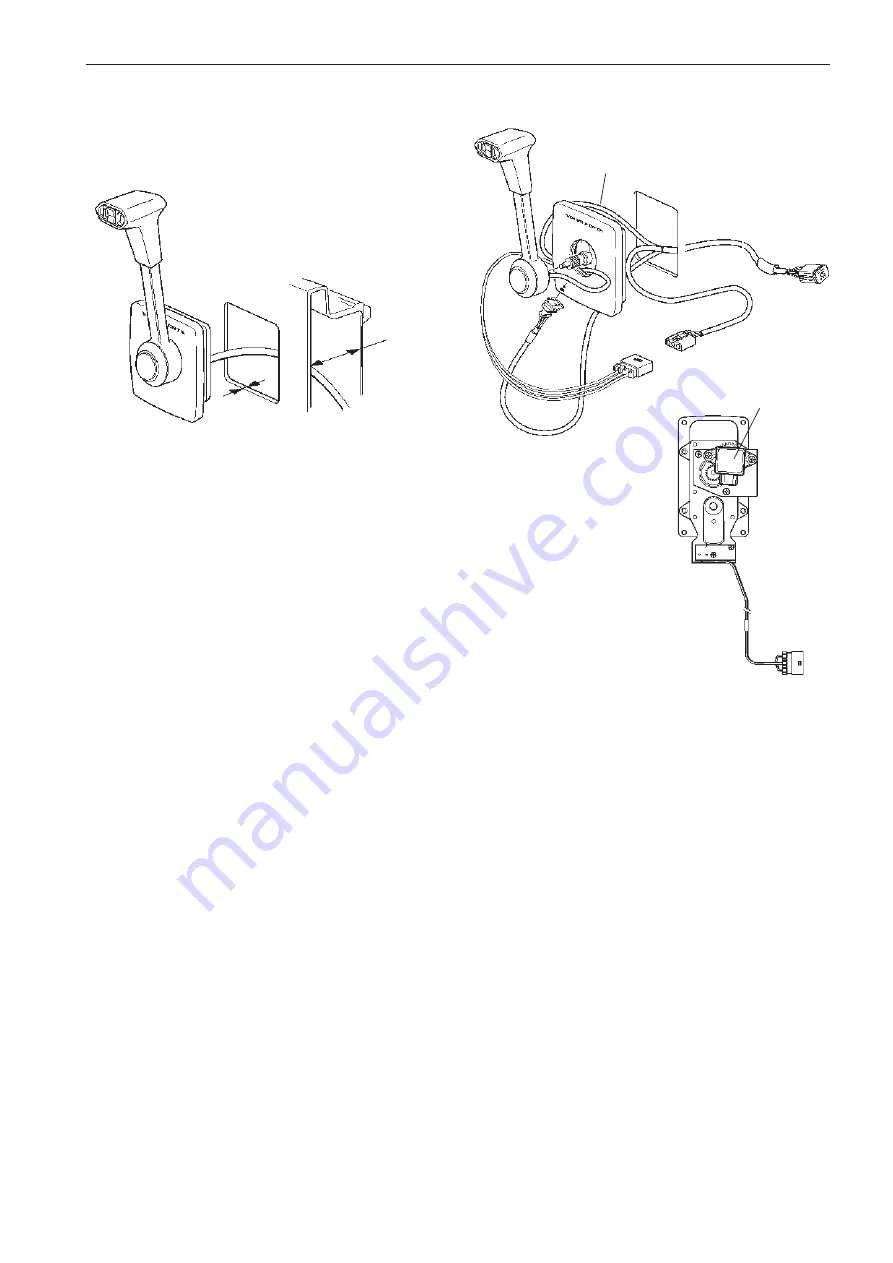
Controls, electronic
Side mounted
Standard mounting
Make.holes.in.the.bulkhead.according.to.template..
Please.refer.to.the.
Templates for controls and pan-
els
.chapter.
Maximum.bulkhead.thickness:.10.mm.(3/8")..
Minimum.space.inside.bulkhead:.100.mm.(4").
THROTTLE.
POT.
CONN.X7.
Blue
Cable,..
Powertrim.control
NEUTRAL.
SWITCH
NEUTRAL.
SWITCH
Potentiometer
Control including Powertrim function
Route.the.cable.harness.and.connectors.through.the.
holes.in.the.plastic.cover,.the.mounting.plate.and.the.
bulkhead.
Connect.the.connector.marked.“THROTTLE.POT.”.to.
the.potentiometer.on.rear.of.the.mounting.plate.
Fit.the.connector.marked.NEUTRAL.SWITCH.to.the.
pig.tail.
Fit.the.mounting.plate.on.the.bulkhead.using.four.
screws..Install.the.cover.and.the.shift.lever.
Connect.the.cable.marked.CONN.X7.to.the.HCU.X7.
connection.(blue).
Max..
10.mm.(3/8")
Min..
100.mm.(4")
73
EVC-C.
Installation.procedure,.helm
Summary of Contents for EVC EC -C
Page 1: ...EVCEC C Electronic Vessel Control D4 D6 D9 D12 D16 Installation 1 1 B E ...
Page 2: ......
Page 135: ...Notes 135 ...
Page 136: ... References to Service Bulletins Group No Date Concerns 136 ...
Page 138: ...7745547 English 09 2007 ...