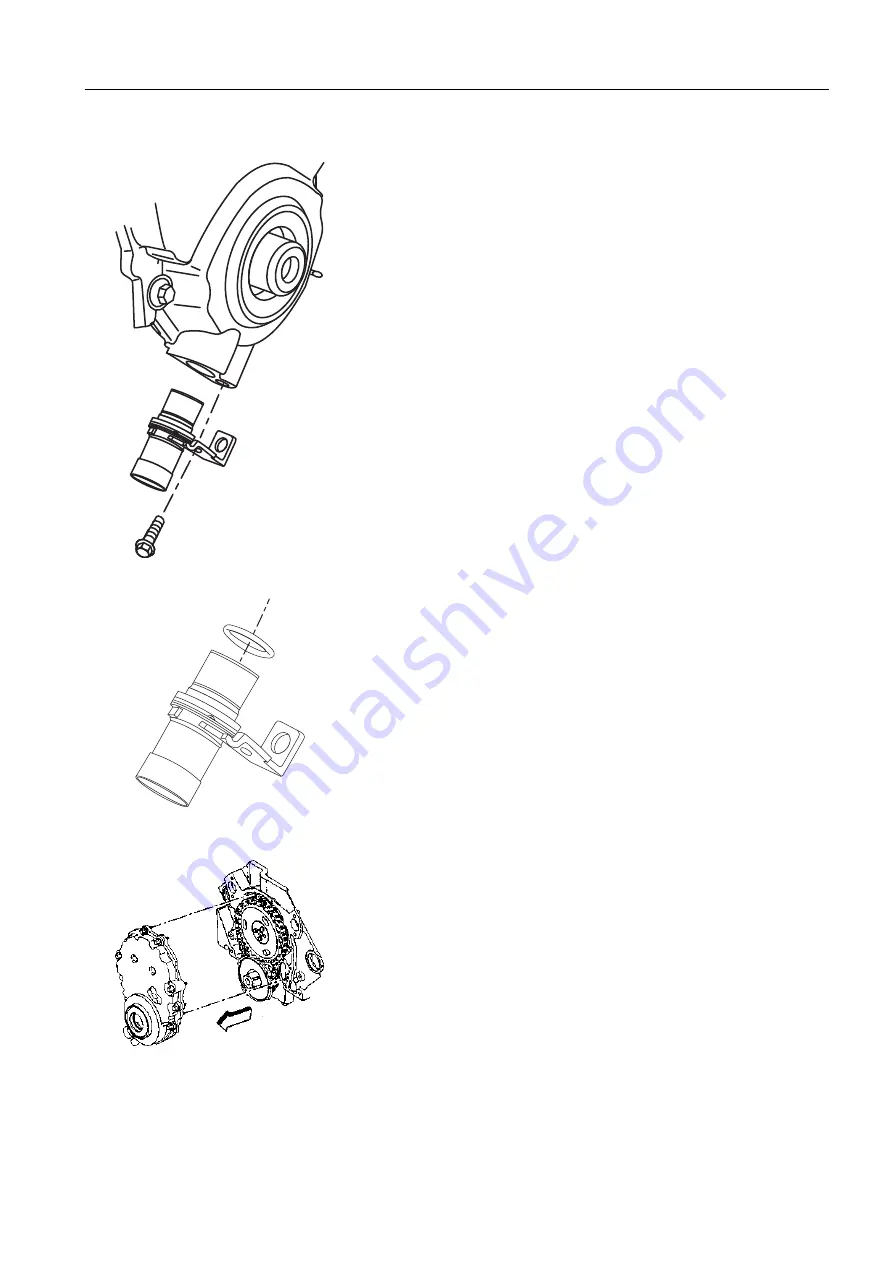
VPA 7748089 English 09-2007
93
Engine — 5.0 & 5.7 Litre
Removal
1.
Remove the crankshaft position sensor bolt.
2.
Remove the crankshaft position sensor.
3.
Remove and discard the crankshaft position sensor seal (O-
ring).
4.
Remove engine front cover bolts and front cover.
NOTICE!
The engine front cover is made of composite material
and has an intergral gasket. Once the front cover is re-
moved, it must be discarded and a new front cover
must be used.
69010