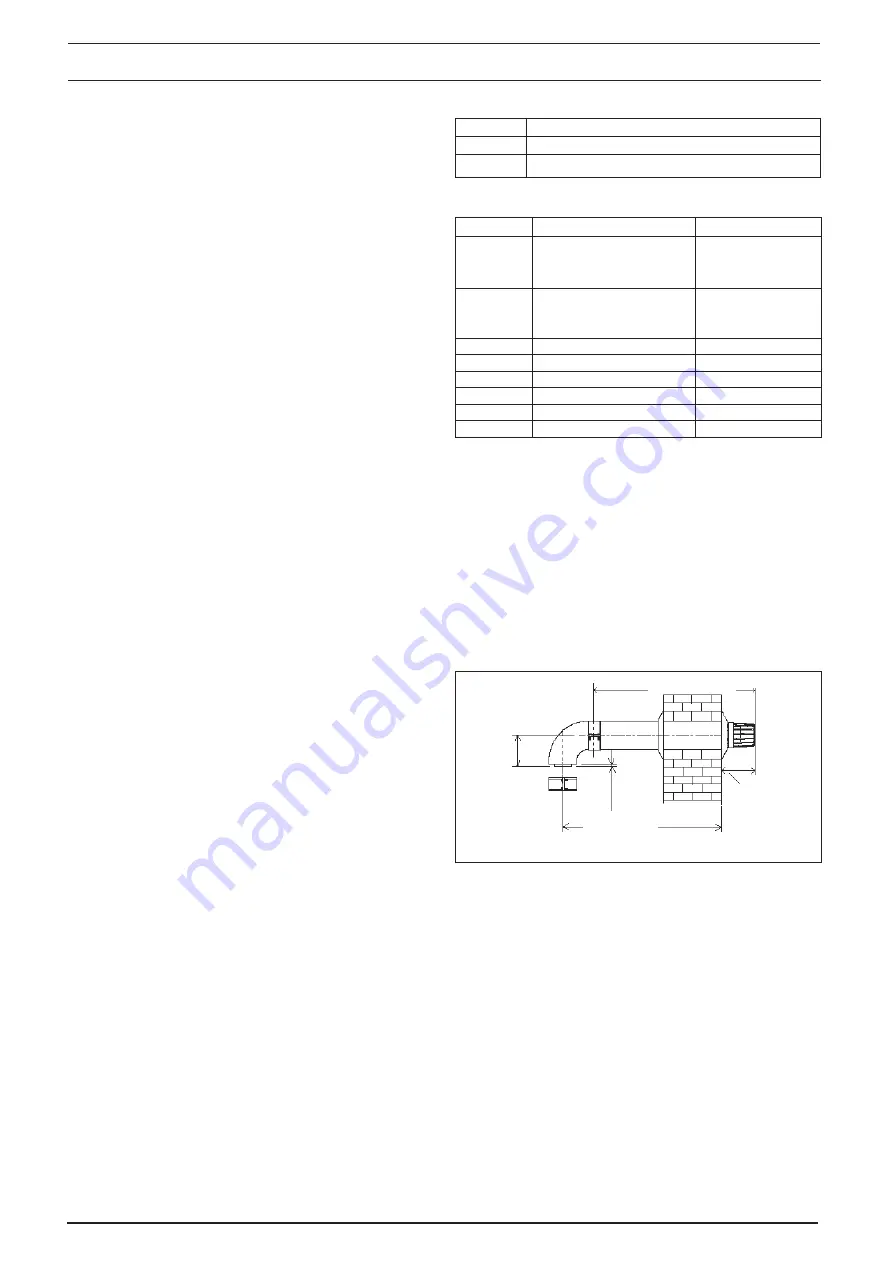
9
Mynute 24m
SECTION 4
INSTALLATION
4.1
DELIVERY
Due to the weight of the appliance it may be
necessary for two people to lift and attach the
appliance to its mounting. The appliance is
contained within a heavy-duty cardboard carton.
Lay the carton on the floor with the writing the
correct way up.
4.2
CONTENTS
Contained within the carton is:
•••••
the boiler
•••••
the wall bracket
•••••
template
•••••
an accessories pack containing appliance serv-
ice connections and washers
•••••
the instruction pack containing the installation &
servicing instructions, user instructions, Bench-
mark logbook, guarantee registration card and a
3-amp fuse.
4.3
UNPACKING
At the top of the carton pull both sides open - do
not use a knife - unfold the rest of the carton from
around the appliance, carefully remove all protec-
tive packaging from the appliance and lay the
accessories etc. to one side. Protective gloves
should be used to lift the appliance, the appliance
back-frame should be used for lifting points.
4.4
PREPARATION FOR MOUNTING THE APPLI-
ANCE
The appliance should be mounted on a smooth,
vertical, non-combustible surface, which must be
capable of supporting the full weight of the appli-
ance. Care should be exercised when determining
the position of the appliance with respect to hidden
obstructions such as pipes, cables, etc.
When the position of the appliance has been
decided - using the template supplied - carefully
mark the position of the wall-bracket (fig. 6) and
flue-hole (if applicable).
4.5
FITTING THE FLUE
The top flue outlet permits both horizontal and
vertical flue applications to be considered, alterna-
tively, the Vokera twin flue system can be utilised
if longer flue runs are required.
4.5.1
CONCENTRIC HORIZONTAL FLUE
(For concentric vertical flue, see 4.5.2).
(For twin flue applications, see 4.5.3).
This appliance can only be used with the standard
60/100mm Uni-flue concentric flue system or the
Vokera parallel (twin) system.
NOTE
These instructions relate
only
to the standard 60/
100mm concentric flue system. The appliance flue
outlet elbow can be rotated through 360° on its
vertical axis. In addition the flue may be extended
from the outlet elbow in the horizontal plane (see
2.9). A reduction must also be made to the
maximum length (see table) when additional bends
are used.
Using the template provided, mark and drill a
105mm hole for the passage of the flue pipe. The
hole should have a 1º drop from the boiler to out-
side, to eliminate the possibility of rainwater en-
tering the appliance via the flue.
The fixing holes for the wall-mounting bracket
should now be drilled and plugged, an appropriate
type and quantity of fixing should be used to
ensure that the bracket is mounted securely.
Once the bracket has been secured to the wall,
mount the appliance onto the bracket.
4.5.1.1 FITTING THE HORIZONTAL FLUE KIT (see
4.5.1)
Carefully measure the distance from the centre
of the appliance flue outlet to the face of the out-
side wall (dimension “
X
” see fig. 7). Ensure the
inner (60mm) pipe is fully inserted into the outer
(100mm) pipe (when the inner pipe is fully inserted,
it stands proud of the outer pipe by 7.5mm). Add
32mm to dimension “
X
” to give the overall flue
length (dimension “
Y
”).
NOTE
The standard horizontal flue kit (part no. 2359029)
is suitable for a distance (dimension “
Y
”) of up to
865mm.
The telescopic flue kit (part no. 2359119) is suit-
able for a distance (dimension “
Y
”) of up to 600mm.
Dimension “
Y
” is measured from the end of the
terminal to the end of the outer (100mm) pipe.
Part No.
Description
Min-Max Length
2359029
Standardl flue kit
For use with add. bends
833 mm
and extensions
(dimension ‘
X
’)
2359119
Telescopic flue kit.
For use with add. bends
and extensions
2359069
750 mm extension
750 mm
2359079
1500 mm extension
1500 mm
2359089
Telescopic extention
350-490 mm
2359049
45º bend (pair)
N/A
2359059
90º bend
N/A
0225760
Wall bracket (5)
N/A
Horizontal flue terminals and accessories
Bend
Reduction in maximum flue length for each bend
45º bend
0.5 metre
90º bend
0.85 metre
Reduction for additional bends
Fig. 7
Dimension “
Y
”
Dimension “
X
”
135 mm
7,5
110