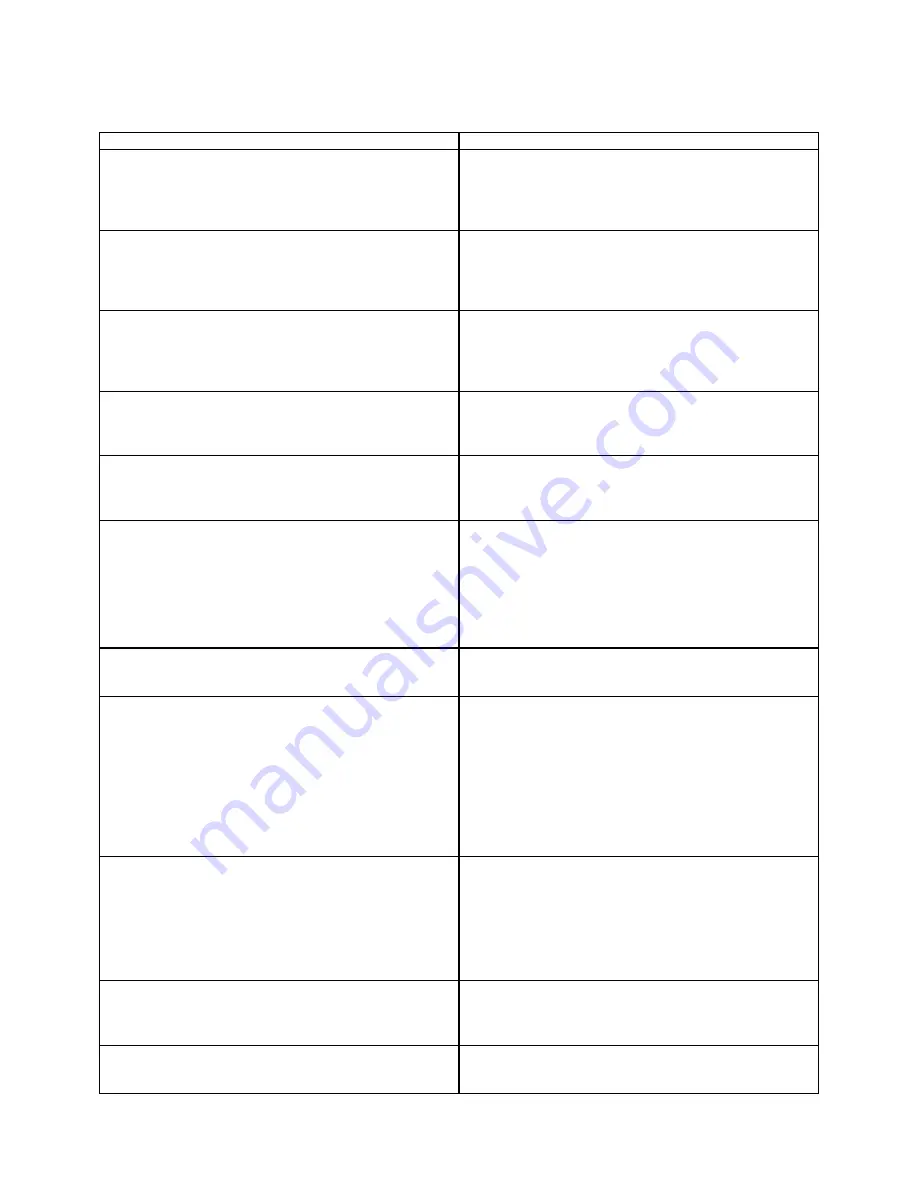
P18AL Service Manual
TROUBLESHOOTING
3/6/07
8-2
Symptom: Machine Stopped
Possible Cause
Possible Remedy
Power failure or interruption
Check fused disconnect or circuit breaker supplying power to
the machine. If power has been off, make sure the crankcase
heater is energized and there is no liquid refrigerant in the
compressor crankcase prior to restarting the compressor. If ice
is in the freezer, initiate a manual harvest.
Circuit breaker (CB4) for control circuit tripped
Check compressor crankcase heater, coils of relays, contactors,
starters, solenoid valves, and thawing timer for a ground.
Repair or replace any defective part and reset circuit breaker.
Make sure there is no liquid refrigerant in the compressor
crankcase prior to restarting the machine.
Compressor motor starter overload tripped
Check for a loose connection on all motor starter and motor
terminals that could cause excessive amp draw. Reset
overload and restart the machine, check amperage, power
supply, and head pressure. (Check delay timer in part wind
starts only).
Water pump, cutter motor, conveyor motor, overload tripped
Check for loose connection on all terminals that could cause
excessive amp draw. Reset the overload and manually run that
particular motor to check actual voltage and amperage against
motor rating.
Freezer water pump motor overload (P) tripped
Check for loose terminal connections and/or blown fuse, reset
the overload and restart by pushing the start push button (PB2).
Machine will start in a harvest. Check voltage and amperage
against motor rating during freeze. Confirm proper rotation.
Cutter motor overload (CU) tripped
Check for loose terminal connections and/or blown fuse. Clear
all ice that may have jammed cutter. Reset the overload and
restart by pushing the start push button (PB2). Machine will
start in a harvest. Check voltage and amps against motor
rating. If tripping repeats but ice is not jammed, check the
gear reducer for resistance, cutter bearings for wear, drive gear
and ring gear for proper engagement, and reducer motor for
defect or single phasing.
Bin level control (optional) open
Adjust or replace control as required. If bin level control is not
used, make sure jumper wire from #11 to #14 is installed at the
terminal block.
High/Low pressure safety switch tripped (optional)
If the machine stops by low pressure cutout, the switch will
reset automatically when the pressure rises to the “cut-in”
setting. Check thaw gas valve (18) to make sure it opens
during harvest time. Check Liquid feed valve (25) to make
sure it is feeding during a freeze.
If the machine stops by high pressure cutout, the switch will
have to be manually reset after the pressure drops below the
“cut-in” setting. Check the head pressure during the next
freeze cycle.
Low oil pressure tripped (OPS) located on compressor
Manually reset the switch after the switch heater cools. Check
the crankcase oil level (1/4-3/4 full). Add oil if below 1/4
glass before attempting to restart the machine.
Restart the machine and check net oil pressure (net oil pressure
= oil pump line pressure minus crankcase suction pressure).
Net oil pressure range: Mycom= 17-28 psig Vilter= 35-50 psig
Defective control panel component such as 1PB, SS, 1CR, T
See FIGURE 6-3, Wiring Schematic, and check for open
circuit. Refer to FIGURES 6-1 and 6-2, Control Panel to
identify parts. Check for loose wires. Replace defective part,
restart machine, check power supply, and current draw.
Fused disconnect for pump or cutter motor blown.
Check for loose connection on all terminals, replace fuse and
check amp draw against fuse rating. Check voltage and
current unbalance, Section 3. Replace fuse if blown.
Summary of Contents for P18AL TUBE-ICE
Page 1: ...8 28 00 P18AL TUBE ICE MACHINE Manual Part Number 12A4171M09 Service Manual 5000 ...
Page 4: ......
Page 14: ...P18AL Service Manual INTRODUCTION 3 6 07 1 4 FIGURE 1 1 P18AL Front View ...
Page 15: ...P18AL Service Manual INTRODUCTION 3 6 07 1 5 FIGURE 1 2 P18AL Back View ...
Page 16: ...P18AL Service Manual INTRODUCTION 3 6 07 1 6 FIGURE 1 3 P18AL Left View ...
Page 17: ...P18AL Service Manual INTRODUCTION 3 6 07 1 7 FIGURE 1 4 P18AL Right View ...
Page 18: ...P18AL Service Manual INTRODUCTION 3 6 07 1 8 ...
Page 48: ...P18AL Service Manual ELECTRICAL CONTROLS 3 6 07 6 6 ...
Page 56: ...P18AL Service Manual MAINTENANCE 3 6 07 7 8 ...
Page 64: ...P18AL Service Manual TROUBLESHOOTING 3 6 07 8 8 ...
Page 76: ...P18AL Service Manual SERVICE OPERATIONS 3 6 07 9 12 FIGURE 9 3 Cutter Water Tank Assembly ...
Page 78: ...P18AL Service Manual TABLES CHARTS 3 6 07 10 1 10 Tables Charts ...