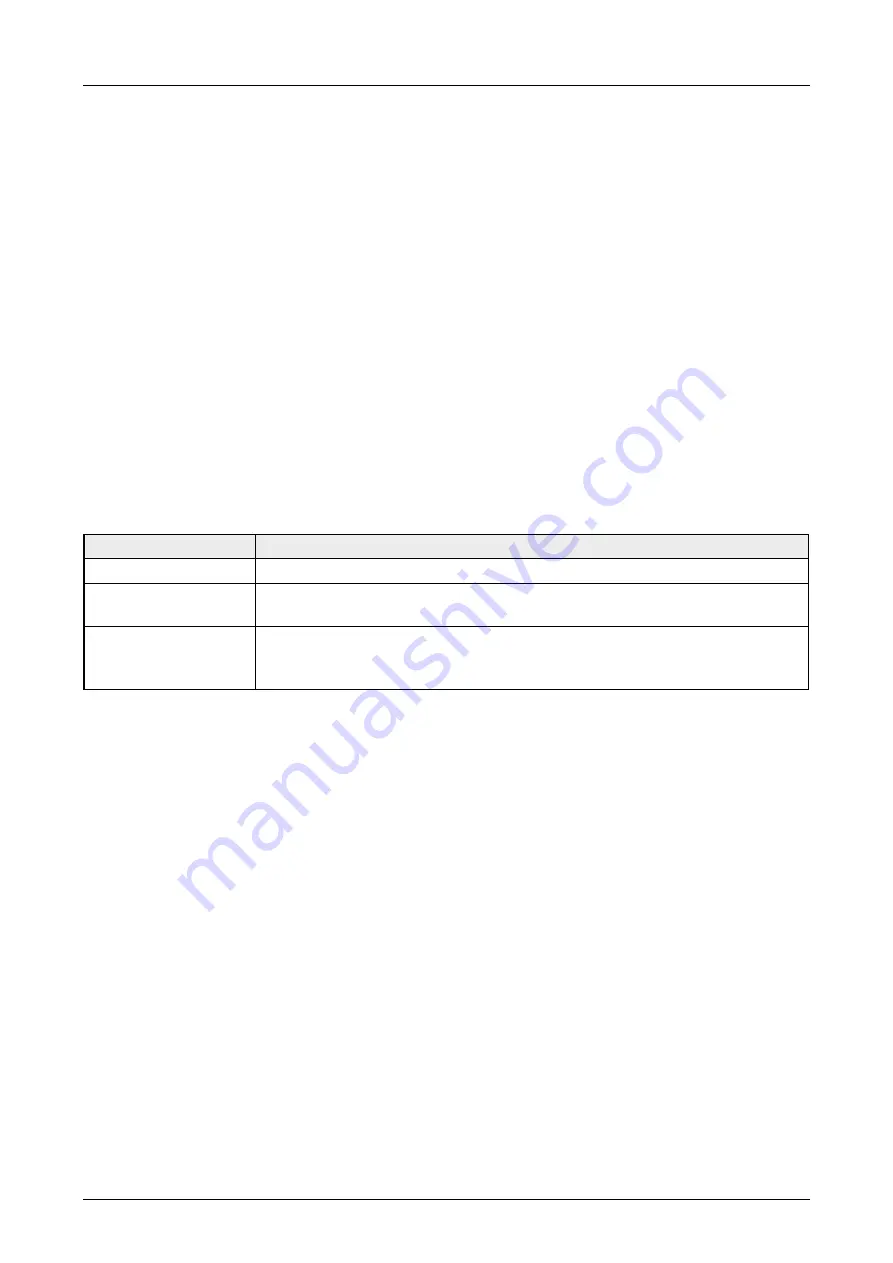
Manual VIPA System 300S SPEED7
Chapter 5 Communication protocols
HB140E - CP - RE_341-2CH71 - Rev. 09/46
5-7
Number of bits onto which a character is mapped.
Range of values: 5 ... 8
Default: 8
The addition of its value "0" or "1" brings the value of all the bits (data bits
and parity bit) up to a defined status.
Range of values: none, odd, even
Default: none
When data is transmitted, stop bits are appended to each character to be
sent in order to signal the end of a character.
Range of values: 1, 2
Default: 1
Data flux control synchronizes data transmission when one communication
partner works faster than the other. Here the type of data flux control may
be set.
Value
Description
none
The flux control is deactivated.
hardware
Hardware flux control employs the RTS and CTS lines and these must
therefore be wired accordingly.
XON/XOFF
Software flux control employs the control characters XON=11h and
XOFF=13h. Please remember that your data must not contain these
control characters.
Range of values: none, hardware, XON/XOFF
Default: none
The delay time that must expire before a command is executed. The ZNA
is to be specified in ms.
Range of values: 0 ... 65535
Default: 0
TMO defines the maximum time between two messages. TMO is to be
specified in ms.
Range of values: 0 ... 65535
Default: 200
You may select 1 or 2 start identifications. When you select "1" as number
of start identifications, the contents of the 2. start identification is ignored.
Range of values: 0 ... 2
Default: 2
Data bits
Parity
Stop bit
Flux control
Time after order
Timeout (TMO)
Number start
identifications
Summary of Contents for CP 341S
Page 1: ...VIPA System 300S SPEED7 CP 341 2CH71 Manual HB140E_CP RE_341 2CH71 Rev 09 46 November 2009 ...
Page 4: ...Contents Manual VIPA System 300S SPEED7 ii HB140E CP RE_341 2CH71 Rev 09 46 ...
Page 8: ...Safety information Manual VIPA System 300S SPEED7 4 HB140E CP RE_341 2CH71 Rev 09 46 ...
Page 70: ...Index Manual VIPA System 300S SPEED7 A 2 HB140E CP RE_341 2CH71 Rev 09 46 M Stich ...