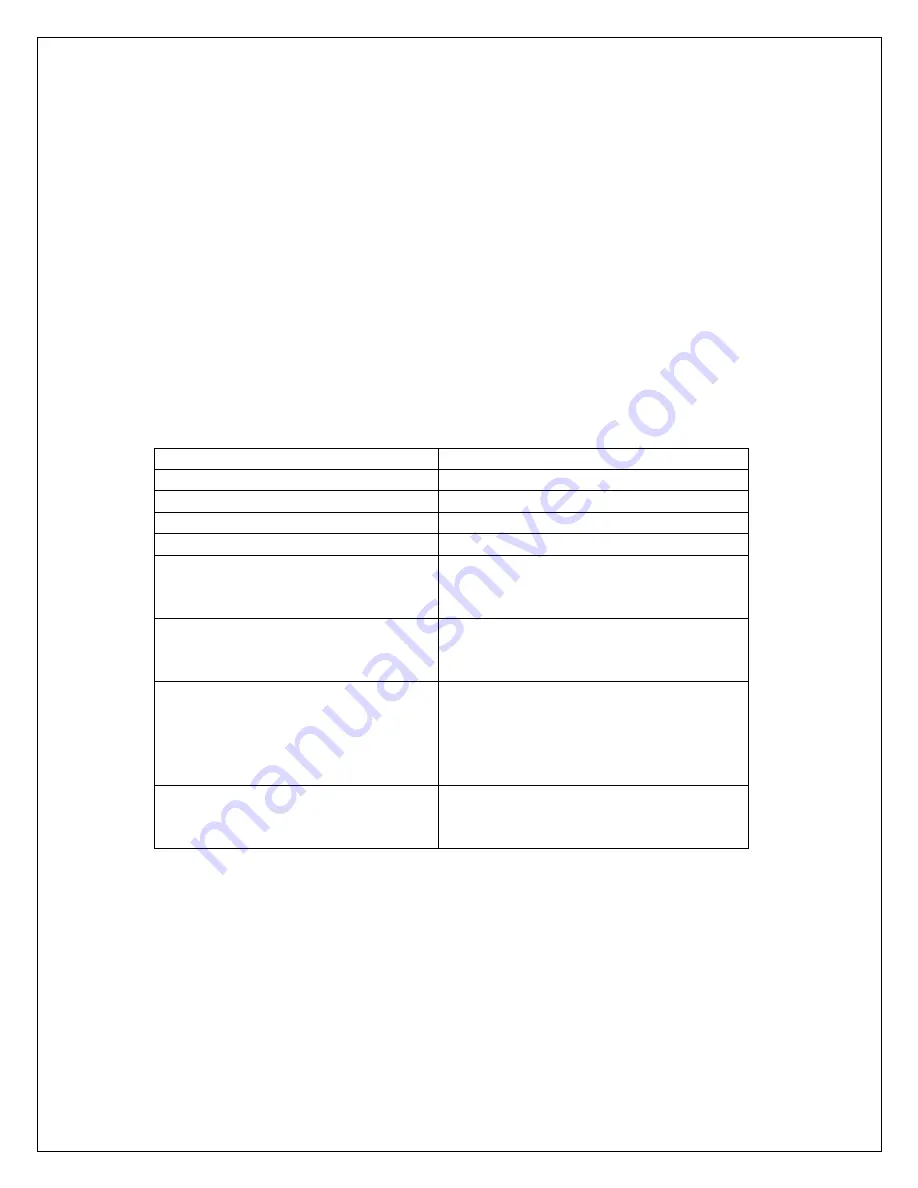
- 4 -
•
Use dry nitrogen to purge the system.
•
Do not overcharge the refrigeration system.
•
Do not leave replacement compressor open to the atmosphere for more
than 10 minutes.
•
Do not operate the compressor without refrigerant charge in the system.
•
Do not use the compressor if the rubber plugs on the replacement
compressor appear to have been tampered or removed.
•
Always replace the filter-drier when performing any repairs on the sealed
system.
•
The filter-drier must be cut from the sealed system. Never unbraze the
filter-drier from system tubing. Applying heat will drive moisture back into
sealed system.
Table 1-1 Health and Safety Handling of R134a
Allowable Overall Exposure Limit 1,000 ppm
Vapor Exposure to Skin
No Effect
Liquid Exposure to Skin
Can cause frostbite
Vapor Exposure to Eyes
Can cause very slight irritation
Liquid Exposure to Eyes
Can cause frostbite
Above Minimum Exposure Limit
Can cause asphyxiation, tachycardia
and cardiac arrhythmia's. Wear
appropriate skin and eye care.
Spill Management
Combustible sources. Evacuate or
ventilate area.
May decompose if in contact.
Fire and Explosion Hazards
Made with flames and heating
elements. Container may explode if
heated due to pressure rise.
Combustion products are toxic.
Storage Conditions
The procedures/rules for R12 also
apply to R134a.
Reclaim
Summary of Contents for WINE-MATE VINO3500HZD
Page 2: ...1 SAFETY INFORMATION...
Page 8: ...7 Figure 2 3 Figure 2 4...