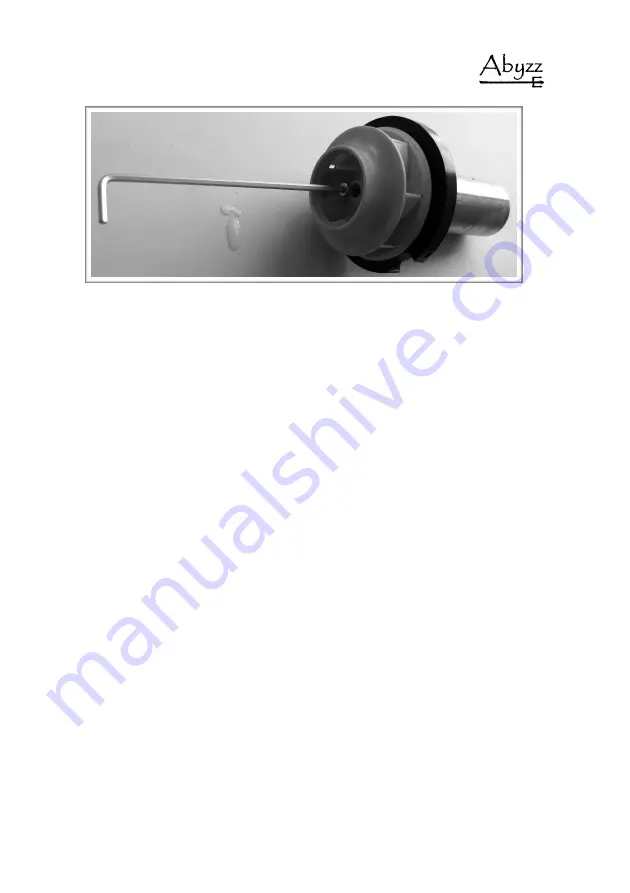
!
Fig. 5:
Disassembly of impeller wheel
When assembling the pump (fig. 6 and 7), please make sure that the guide lug (A) fits
into the corresponding opening on the magnetic impeller plate and that the flushing
opening (C) is in the right place. Make sure that the bearing (B) is in the correct
position inside the motor. If necessary, push the bearing into position with a blunt
object (e.g. the handle of a screwdriver). Make sure that the O-ring for the vibration
isolation and sealing (fig. 10) is in the right position before reassembling the pump.
20