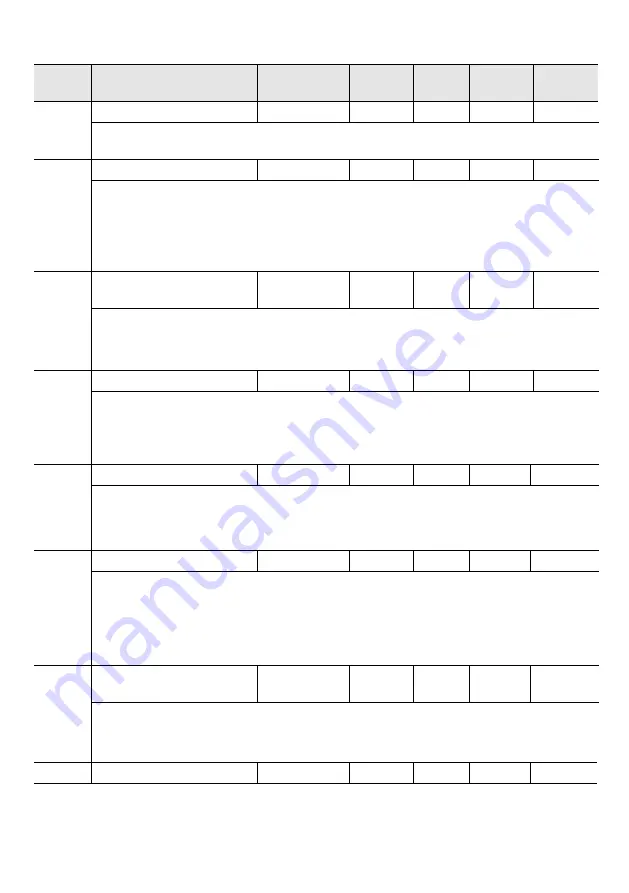
17
3.2
Pn1 Gain Parameters
Function
code
Parameters
Range
Default
Unit
Address
Effective
way
Pn100
Rotary inertia ratio
0~20000
100
%
0x0100
INST
Rotary inertia ratio = Motor shaft converted load rotary inertia /servo motor rotor rotary inertia
*100%
Pn101
First speed gain
1~2000
40.0
Hz
0x0101
INST
Parameters to determine the responsiveness of the speed loop. When the responsiveness of the
speed loop is low, it will become the delay element of the outer position loop. Therefore,
overshoot or vibration of the speed command will occur. Within the range where the mechanical
system does not vibrate, the larger the setting value, the more stable the servo system. The better
the responsiveness
Pn102
First speed integral time
constant
0.15~512
20.00
ms
0x0102
INST
In order to respond to small inputs, the velocity loop contains integral elements. Since the integral
element is a delay element for the servo system, when the time parameter is set too large,
overshoot will occur, or the positioning time will be prolonged, making the response worse
Pn103
First position gain
1~2000
40.0
1/s
0x0103
INST
The response of the position loop is determined by the position loop gain. The higher the position
loop gain setting, the higher the responsiveness and the shorter the positioning time. The position
loop gain cannot be increased beyond the rigidity of the mechanical system. To set the position
loop gain to a larger value, the machine rigidity needs to be increased
Pn104
First torque command filter
0~655.35
1.00
ms
0x0104
INST
Adjusting the torque command filter parameters may eliminate the machine vibration caused by
the servo drive. The smaller the value, the better the responsive control, but it is restricted by the
machine conditions.
Pn105
Second speed gain
1~2000
40.0
Hz
0x0105
INST
Parameters to determine the responsiveness of the speed loop. When the response of the speed
loop is low, it will become the delay element of the outer position loop. Therefore, overshoot or
vibration of the speed command will occur. Within the range where the mechanical system does
not vibrate, the larger the setting value, the more stable the servo system. The better the
responsiveness
Pn106
Second speed integral time
constant
0.15~512
20.00
ms
0x0106
INST
In order to respond to small inputs, the velocity loop contains integral elements. Since the integral
element is a delay element for the servo system, when the time parameter is set too large,
overshoot will occur, or the positioning time will be prolonged, making the response worse
Pn107
Second position gain
1~2000
40.0
1/s
0x0107
INST
Summary of Contents for SD700-110D series
Page 8: ...4 ...
Page 14: ...10 1 10 Position Control Wiring Diagram ...
Page 15: ...11 1 11 Speed Control Wiring Diagram ...