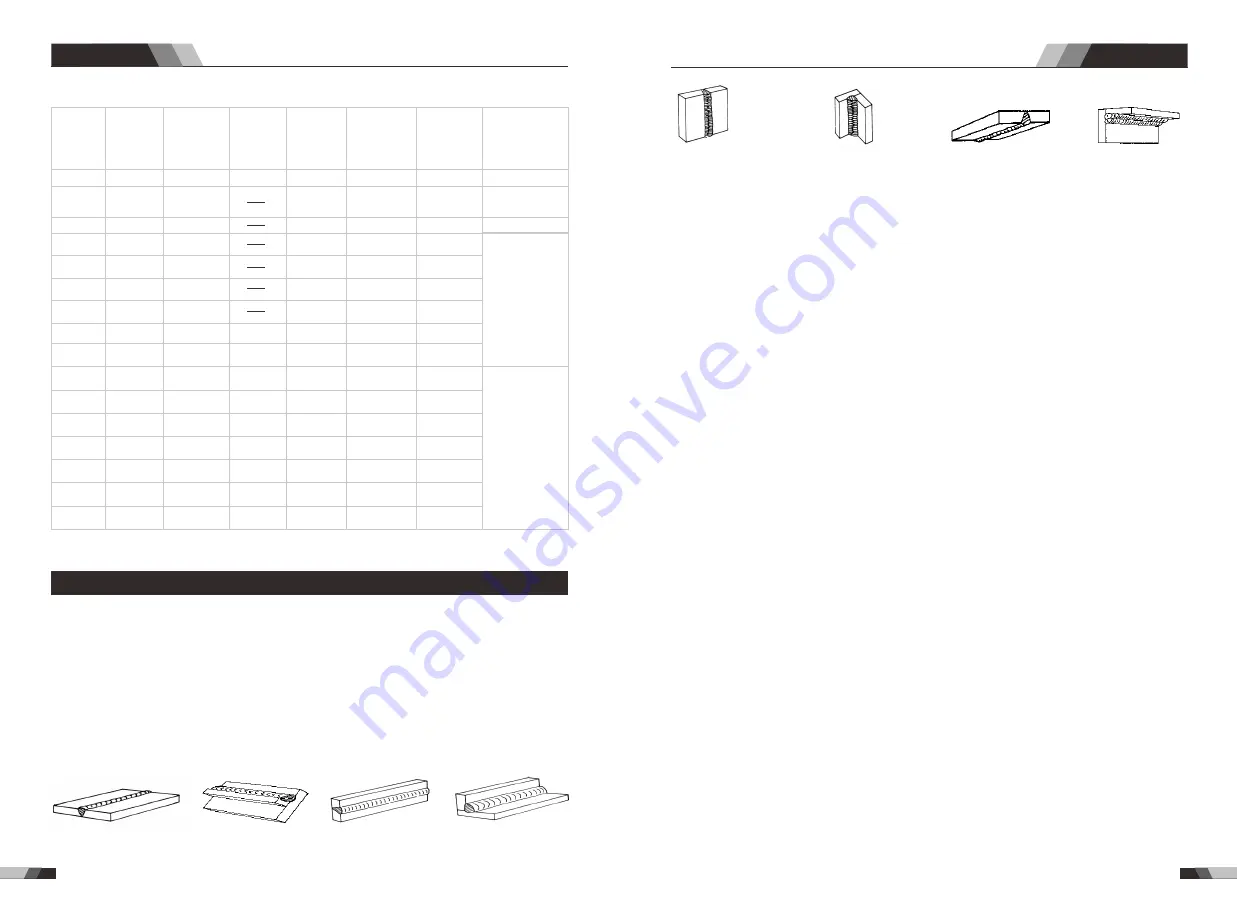
59
60
Welding technique
Welding technique
Notice: the above parameters originate from
《
Welding Dictionary
》
P538, Volume 2 of Edition 2.
Parameters of AC TIG(MMA) for Aluinum and its alloy
Steet
thickness
/mm
Welding
wire
diameter
/mm
Tungsten
eletrode
diameter
/mm
Pre-heat
Temper
-ature/ºC
Welding
current/A
Argon flow
1
rate/L•min-
Gas nozzle
diameter
/mm
Remark
1.6
1.6~2.0
2~2.5
2~3
3
3~4
4
4~5
4~5
2
2
2~3
3
4
4
5
5
5
100
100~150
45~60
50~80
90~120
150~180
180~200
180~240
240~280
260~320
280~340
1
1.5
2
3
4
5
6
8
10
7~9
7~9
8~12
8~12
10~15
10~15
16~20
16~20
16~20
8
8
8~12
8~12
8~12
10~12
14~16
14~16
14~16
Flange welding
Flange or butt
welding by
one side
Butt welding
V-groove
butt welding
12
14
16
18
20
16~20
22~25
4~5
5~6
5~6
5~6
5~6
5~6
5~6
5~6
5~6
6
6
6
6
6~7
150~200
180~200
200~220
200~240
200~260
200~260
200~260
300~360
340~380
340~380
360~400
360~400
300~380
360~400
18~22
20~24
20~24
25~30
25~30
25~30
30~35
16~20
16~20
16~20
16~20
20~22
16~20
20~22
X-groove
butt welding
4.5 MMA Basic Welding Technique
Arc Welding Practice
The techniques used for arc welding are almost identical regardless of what types of
metals are being joined. Naturally enough, different types of electrodes would be used
for different metals as described in the preceding section.
Welding Position
T h e e l e c t r o d e s d e a l t w i t h i n t h i s p u b l i c a t i o n c a n b e u s e d i n m o s t p o s i t i o n s , i . e . t h e y
are suitable for welding in flat, horizontal, vertical and overhead positions. Numerous
applications call for welds to be made in positions intermediate between these. Some
of the common types of welds are shown
Flat
Position
,
Down
Hand
Butt
Weld
Flat
Position
,
Gravity
Fillet
Weld
Horizontal
Position
,
Butt
Weld
Horizontal
-
Vertical
(
HV
)
Position
AC/DC WIG SERIES EQUIPMENT
AC/DC WIG SERIES EQUIPMENT
Vertical Position,
Butt Weld
Vertical
Position
,
Fillet
Weld
Vertical Position,
Fillet Weld
Overhead
Position
,
Fillet
Weld
Joint Preparations
In many cases, it will be possible to weld steel sections without any special preparation.
For heavier sections and for repair work on castings, etc., it will be necessary to cut or grind
an angle between the pieces being joined to ensure proper penetration of the weld metal
and to produce sound joints.
In general, surfaces being welded should be clean and free of rust, scale, dirt, grease, etc.
Slag should be removed from oxy-cut surfaces.
Arc Welding Technique - A Word to Beginners
For those who have not yet done any welding, the simplest way to commence is to run beads
on a piece of scrap plate. Use mild steel plate about 6.4mm (1/4") thick and a 3.2mm (1/8")
electrode. Clean any paint, loose scale or grease off the plate and set it firmly on the work
bench so that welding can be carried out in the downhand position. Make sure that the work
clamp is making good electrical contact with the work, either directly or through the work
table. For light gauge material, always clamp the work lead directly to the job, otherwise
a poor circuit will probably result.
The Welder
Place yourself in a comfortable position before beginning to weld. Get a seat of suitable
height and do as much work as possible sitting down. Don't hold your body tense. A taut
attitude of mind and a tensed body will soon make you feel tired. Relax and you will find
that the job becomes much easier. You can add much to your peace of mind by wearing
a leather apron and gauntlets. You won't be worrying then about being burnt or sparks
setting alight to your clothes.
Place the work so that the direction of welding is across, rather than to or from your body.
The electrode holder lead should be clear of any obstruction so that you can move your
arm freely along as the electrode burns down. If the lead is slung over your shoulder,
it allows greater freedom of movement and takes a lot of weight off your hand. Be sure the
insulation on your cable and electrode holder is not faulty, otherwise you are risking an
electric shock.