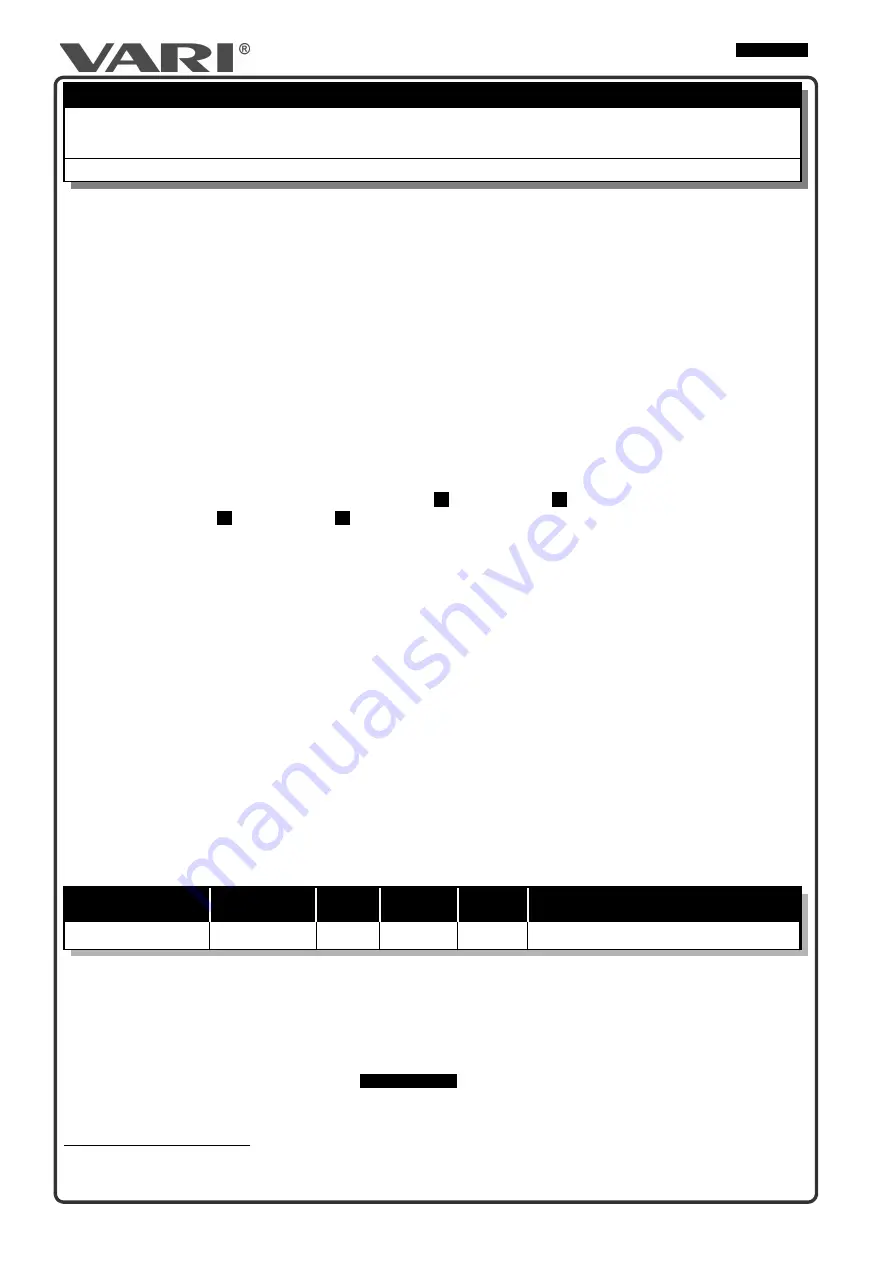
RBS-700D
TOOLS
Wrench 10 mm – 2x or wrench 10 mm – 1x 12-point socket – 1x.
Wrench or socket 13 mm – 1x.
Allen key No. 6
12-point socket 15 mm 1x; 16 mm - 1x. Low bent ratchet 3/8“.
Table 14: Recommended Tools and Accessories
2.5.2 Sharpening, replacement of working tool
If the cutting edges are worn or damaged, causing machine vibrations, the cutting edges should be restored or the blades replaced
Even though the working tool is made of quality quenched steel, wear and tear of the sharp edges and reduction of the mowing
performance occurs.
In case of a replacement of the working tool with a non.original spare part the manufacturer is not responsible for
damages or injuries caused by the machine or on the machine. The blade is embossed with a sign that indicates
the manufacturer and is a check mark that the blade is an original spare part!
The machine must be placed on a hard horizontal surface and must be secured so that there is good access to the
blade and machine would not start moving unexpectedly.
Take special care when removing the blades. Blade cutting edges are sharp. Protect your hands with working
gloves.
The engine must be switched OFF and the spark plug cable end removed!
See
Fig.
1.
Use a 16mm socket to loosen and remove the M10 low nut
1
. Loosen the screw
2
using a 15-mm socket and remove it.
2.
Remove the blade
3
and blade support
4
from the cutting disc. Straighten the edges and sharpen the blade cutting edges. The
inclination of the sharpened edge should be 30° with respect to the blade’s bottom plane.
3.
Make sure all the blade mounting parts feature no visible damage. Otherwise, replace the damaged part with a new one.
4.
Screw the blade screw assembly back in
. Lock the screw with its nut.
If any blade is bent or excessively worn, you must always replace all the cutting disc blades!
For the quality of the vegetation processing we recommend to check the blade quality every 5 hours, especially if the
machine works under very demanding conditions!
Spend several seconds of your time to tighten the bolted joints of the working tool prior to every work with the machine
and after every impact of the blade on a solid obstacle!
Failure to observe this rule means a risk of injury in case the working tool detaches!
2.5.3 Machine Lubrication
When working with lubricants, observe the basic hygiene regulations and observe the environmental protection
regulations and laws.
2.5.3.1 Lubrication Points
Sliding bearings require to be lubricated by a lubricant with MoS and graphite admixture. However, its application usually requires the
dismantling of the respective slide. Leave this work to the authorized service.
Lubrication point -
description
Interval within
season
After
season
Lubricant
Figure
Note
Tensioning pulley
every 100 hours
Yes
MOLYKA G
Fig. 8
Pulley arm pin or case - service.
Table 15: Lubrication intervals
2.5.4 Adjusting tension pulley
If you are not sufficiently manually skilled, have the operations done by an authorized service centre.
If the travel mechanism of the working tool starts failing under the load, it is possible that clutch drive belt slippage occurs.
See figure
Fig.
on page
for the procedure.
1.
Attach (or leave attached) the adaptor to the
RAPTOR Hydro
multifunctional carrier.
2.
Remove the plastic belt cover - six M6x16 screws (see chap.
2.4.1.2 Machine Assembly Procedure
)-
2x wrenches
or a wrench and socket 10mm.
3.
First, check visually for any signs that the v-belt is greasy or for any visible ruptures or separated rubber parts.
41
The blades have two edges - they may be rotated as needed. In any case, the blade must be undamaged.
42
If the rubber ring is damaged, its replacement with a new one is not necessary. The function of the blade or the mowing is not affected, it is used only to fix the blades in the
machine packaging.
43
Insufficient screw tightening leads in most cases to the destruction of the hardened pad around which the blade rotates.
25
re
vi
ze
0
2/
20
18
Summary of Contents for RBS-700D
Page 2: ......
Page 4: ...Z ru n list CZ...
Page 29: ...RBS 700D 29 revize 02 2018...
Page 48: ...RBS 700D 48 revize 02 2018 10 11 12 13 14 14 Mu MAX Mu MAX 15 15 16 F MAX 17 17 18...
Page 53: ......
Page 54: ......
Page 55: ......