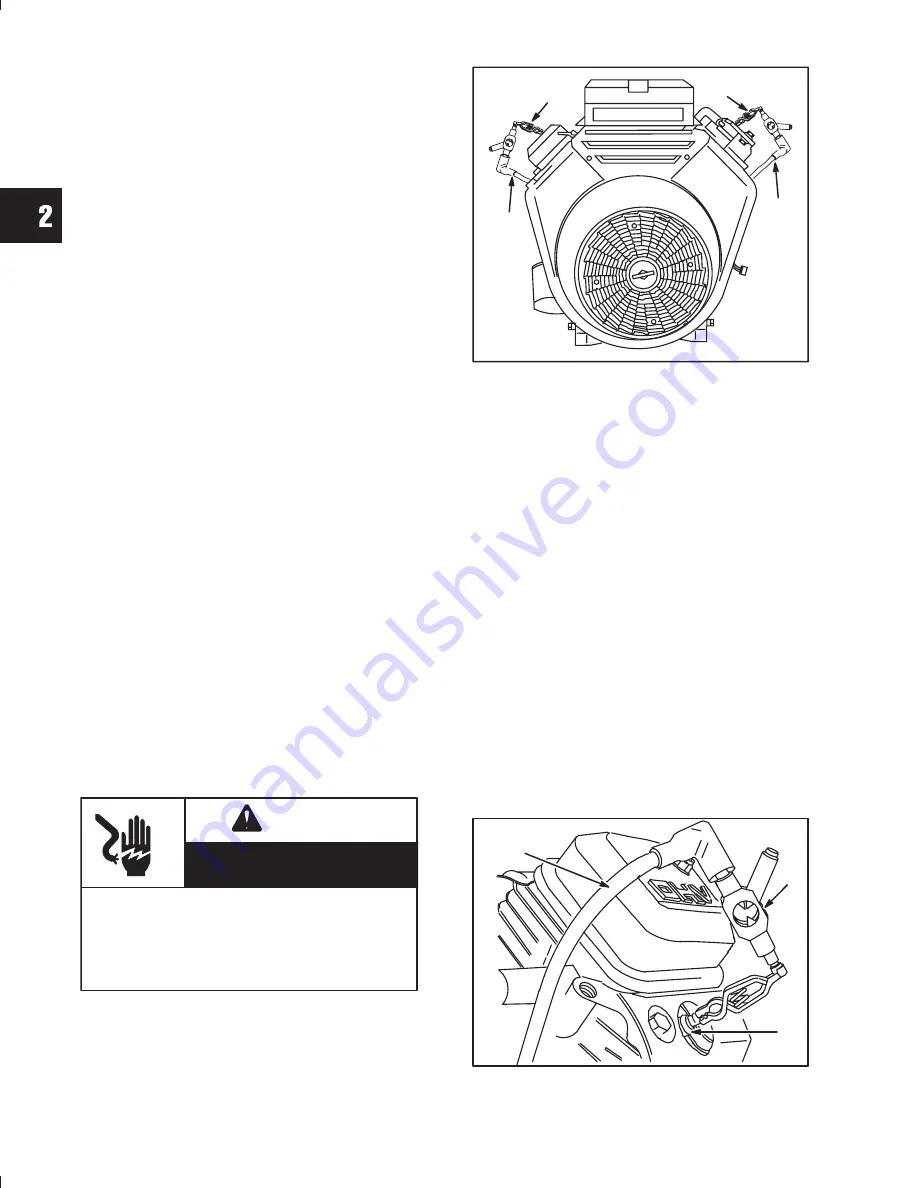
2
28
Most complaints concerning engine operation can be
classified as one or more of the following:
1. Will not start
2. Hard starting
3. Lack of power
4. Runs rough
5. Vibration
6. Overheating
7. High oil consumption
NOTE:
What appears to be an engine problem may
actually be the fault of the powered
equipment. If equipment is suspect, see
Equipment Affecting Engine Operation.
SYSTEMATIC CHECK
A systematic check of the engine can be performed
in minutes, and is an accurate method of
determining the source of the problem. The basic
procedure is the same for all engine models.
Variations, by model, will be shown under the subject
heading. If the engine will not start and the cause is
not apparent, perform a systematic check in the
following order:
1. Ignition
2. Carburetion
3. Compression
Ignition
Test Using Electric Starter
NOTE:
Magnetron
R
ignition systems require a
minimum of
350 RPM
to produce spark.
AVOID ELECTRICAL SHOCK!
WARNING
•
A partially sheared flywheel key will affect
ignition timing and engine performance.
•
Spark can still occur with a sheared flywheel
key. A severe shock or kickback hazard may
exist.
With spark plugs installed, attach Ignition Tester
#
19368
(1) to each spark plug lead (2). Ground the
other end of the tester as shown,
Fig. 1
. Spin the fly-
wheel rapidly with engine starter. If spark jumps the
tester gap the ignition system is working correctly.
Fig. 1
If there is NO SPARK look for –
1. Improperly operating equipment interlock
system
2. Shorted equipment stop switch wire
3. Two closed diodes in ground wire harness
(current style) or ground terminal (early style)
4. Incorrect armature air gap
5. Armature failure
Test With Engine Running
If the engine runs, but misses under load, test the
ignition by installing an Ignition Tester #
19368
(2)
between the spark plug lead (1) and each spark plug
(3),
Fig. 2
. A spark miss will be readily apparent
when the engine is running. If the spark appears
good in the tester but the engine misses, check for
a fouled spark plug.
Fig. 2