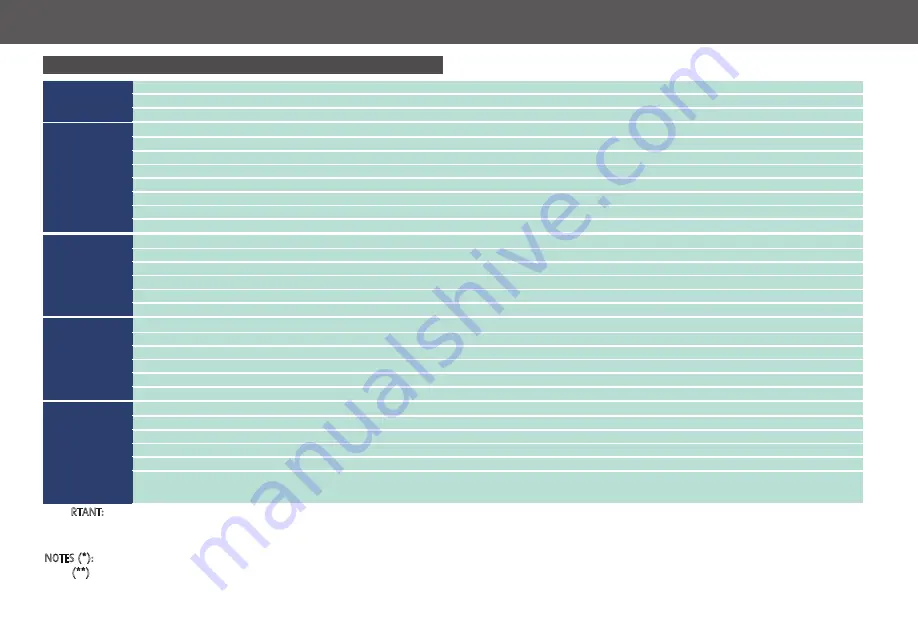
PREVENTIVE MAINTENANCE
1 - Clean or change the return air filter.
2 - Check out the belt stretchiness condition and compressor with alternator alignment, observing the wear and tear of them.
3 - Check the water level of the radiator reservoir. See note (*)
1 - Accomplish the weekly check list.
2 - Clean the condenser capillary tube coil (Apply only water and neutral non-aggressive soup to cooper and aluminum). See note (**)
3 - Check if the evaporator hatches are closed to avoid air intake into the equipment.
4 - Check the refrigerant charge: wait 15 minutes, it has to flow through the liquid display without bulb formation.
5 - Check the compressor oil level: wait 15 minutes, it must be 3/4 up to 1/4 full at oil display.
6 - Test the equipment operation functions: cool / fan (high and low speed) / heat / dry (air renewing) modes.
7 - Lubricate the components of the compressor support. It includes articulation (elbows), axles, bushing and pulleys, if necessary.
8 - Operate the heating system (if any) for at least 30 minutes.
1 - Accomplish the monthly check list.
2 - Measure the exhaust suction pressure, temperature and suction line condition.
3 - Check the tightening of alternator potency cables fuses in general, electric board and start motor.
4 - Measure the condenser and evaporator fan flow consumption (check their air outflow).
5 - Measure the electromagnetic clutch coil.
6 - Measure the Voltage and Current from alternator.
1 - Accomplish the trimestral check list.
2 - Clean the evaporator capillary tube coil (Apply only water and neutral non-aggressive soup to cooper and aluminum). See note (**)
3 - Clean the evaporator drain.
4 - Check out the oil retainer felt of the compressor sealing part.
5 - Look carefully, if there is any leakage at coupling spots: oil leakage, refrigerant leakage.
Check if there are any loose, free, damaged, broken, worn parts, rusty, melting, cracked or bad fractioning to the bus body.
1 - Accomplish the semester check list.
2 - Test the compressor efficiency at 1500 RPM.
3 - Make notes about the compressor oil pressure at 1000 RPM.
4 - Check the opening and closing pressures of high and low pressure switches.
5 - Check the screws or bolts that attach the compressor support and equipment, checking the right torque.
6 - Clean the air conditioning body getting rid of any dust/scrap at components: evaporator, condenser, clutch compressor, alternator, alternator,
relay and control board. See note (**)
IMPO
RTANT: If you do not accomplish the preventive maintenance check list as above, it implies to total or partial loss of warranty coverage.
(**): when cleaning using water, protect electrical and electronic components to prevent damage.
The actions of preventive maintenance written in this manual have been based on normal conditions. Just in case of environment contaminated and bad weather
conditions, then you must do the maintenance more frequent.
WEEKLY
MONTHLY
NOTES (*): if necessary, fill it in with water and additives, follow the recommendations of the OEM Body Builder.
YEARLY
SEMESTER
TRIMESTRAL
- Preventive Maintenance Frequency Check List
CC 430 P3
5