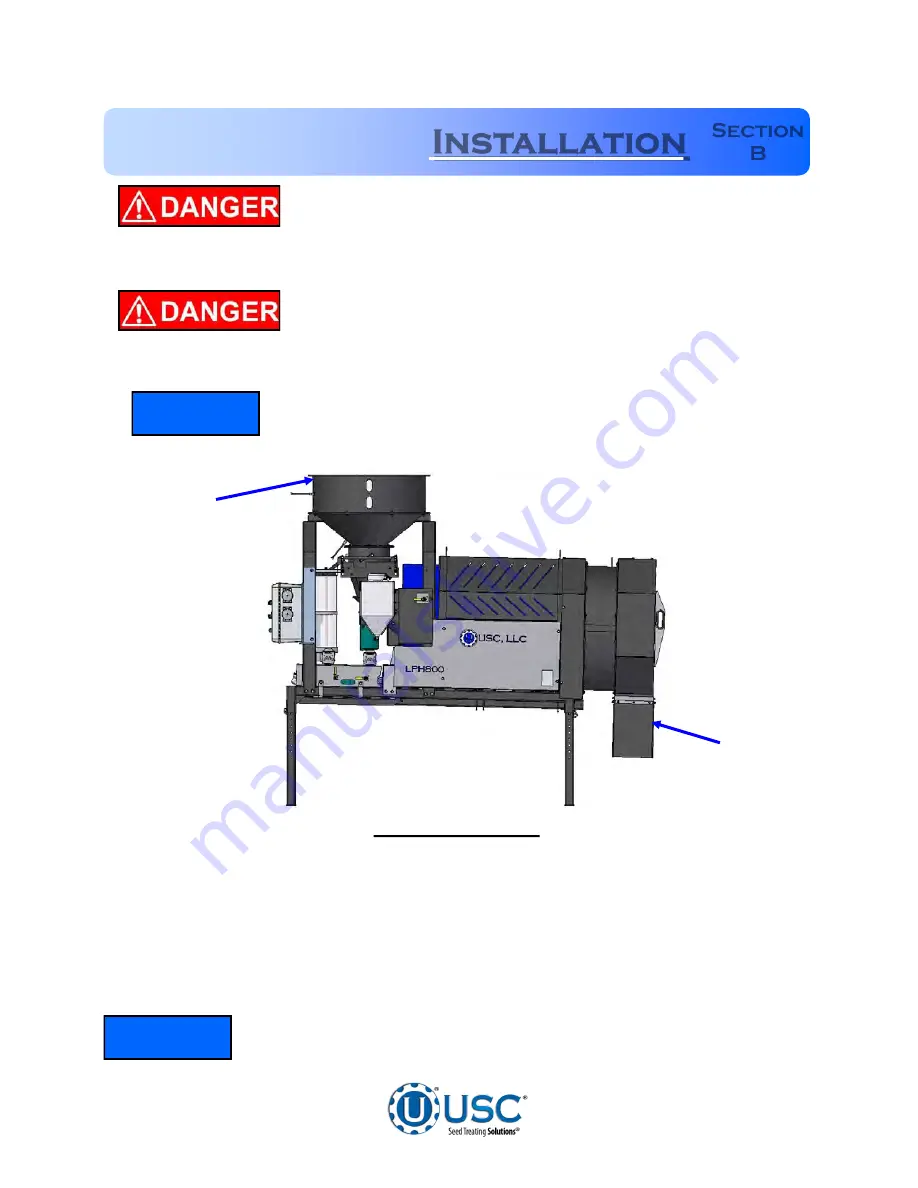
Page 13
LPH800 TREATER
Installation
Section
B
HIGH VOLTAGE ~
Always disconnect the power source
before working on or near the control panel or lead wires.
HIGH VOLTAGE ~
Use insulated tools when making
adjustments while the controls are under power.
Permanent installation may require additional electrical cords,
chemical tubing, and air lines, since each installation is unique.
Rear
Inlet
Discharge
Front
TREATER SET
-
UP
The following steps outline the initial set
-
up of your USC Seed Treating system:
1.
Clear the area of bystanders, especially small children, before moving.
2.
Be sure there is enough clearance from overhead obstructions and power lines or
other equipment to move the machine into its working position.
3.
Using a forklift, place the seed treater in the desired position on a level surface.
USC highly recommends that the seed treater be set up inside a
building or any covered structure to protect the machine from
weathering.
NOTICE
NOTICE
Summary of Contents for LPH800
Page 17: ...Page 17 LPH800 TREATER LPH800 MIX TANK PLUMBING 2 3 ...
Page 49: ...Page 49 LPH800 TREATER LPH800 BASE FRAME ASSEMBLY 18 01 0011 2 9 1 19 16 10 17 15 ...
Page 50: ...Page 50 LPH800 TREATER LPH800 BASE FRAME ASSEMBLY 18 01 0011 20 5 2 3 18 12 3 18 13 2 21 2 ...
Page 57: ...Page 57 LPH800 TREATER LPH800 TREATER Drum 41 A DETAIL A 19 4 42 26 ...
Page 60: ...Page 60 LPH800 TREATER LPH800 TREATER Discharge End 44 49 42 52 46 28 23 ...
Page 61: ...Page 61 LPH800 TREATER LPH800 TREATER Forklift Pockets and Bottom Guards 22 15 16 51 22 26 ...
Page 68: ...Page 68 LPH800 TREATER 30 GALLON TANK AND BASE ASSEMBLY 04 03 0199 7 6 5 2 3 8 10 4 1 4 9 ...
Page 70: ...Page 70 LPH800 TREATER LPH CALIBRATION TUBE ASSEMBLY 13 04 0208 4 10 1 3 8 6 7 11 5 2 9 9 ...
Page 74: ...Page 74 LPH800 TREATER NOTES ...