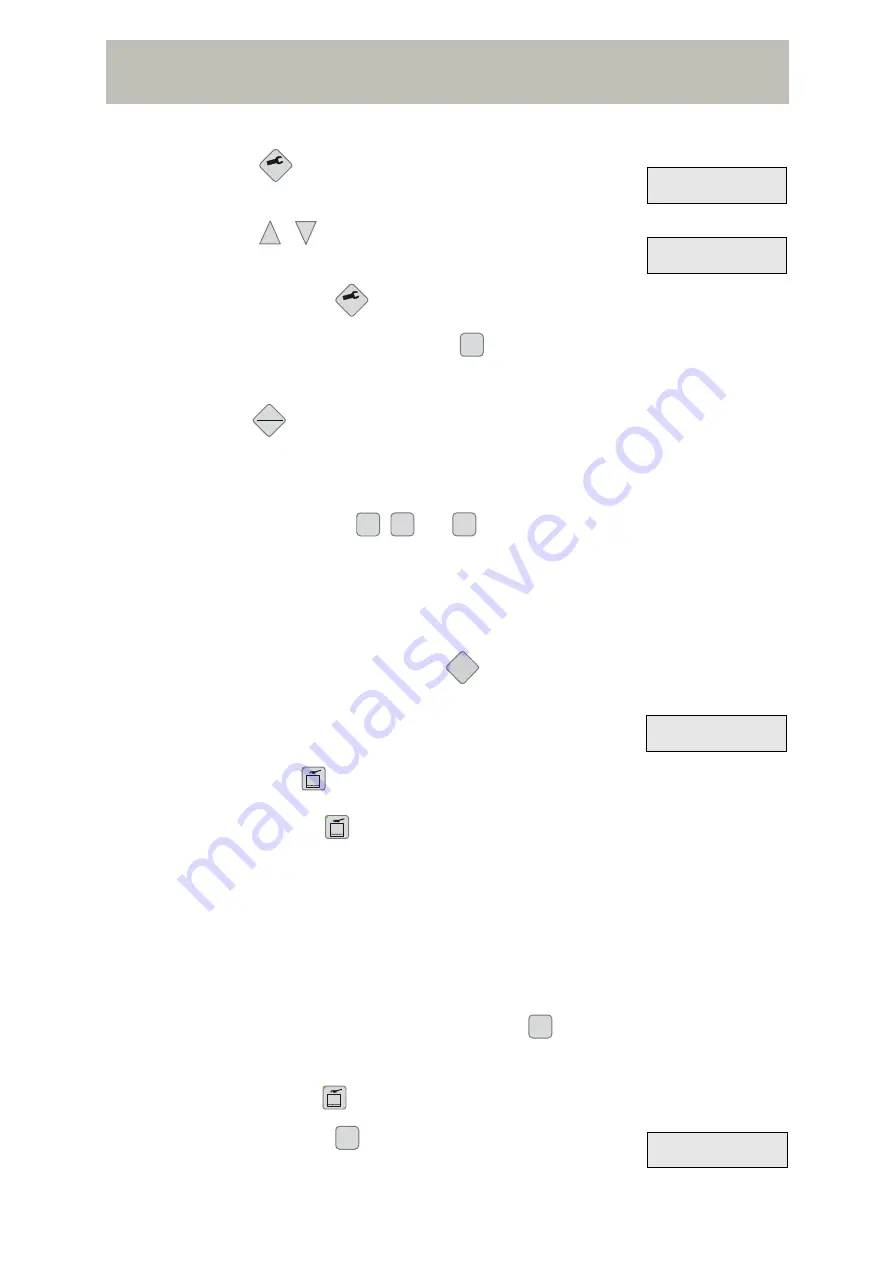
Programming and calibrating
54
3. Press
(approx. 1 second) to switch to the
programming mode:
4. Press
/
to set the required feed
amount (here: 3.5 l (or kg)):
5. Briefly press the
key.
6. This assigns the preselection key
a feed amount of 3.5 l (or kg) and ends
the programming mode.
Use the
key to exit the programming of the feed amount.
7.5
Programming the cleaning programs
The preselection keys
,
and
can be programmed with frequently
required cleaning times. One can either programme simple or extended cleaning
programs. With extended cleaning, the rinsing phase is preceded by a heating
phase. While simple cleaning is possible both in mains and in battery mode, the
extended cleaning (with pre-heating function) is only possible in mains operation.
Switch on the Milk Shuttle with the
key
(approx. 2 seconds).
The "Cleaning" menu is accessed from the main menu:
Hold down the
key for approx. 2 seconds.
After pressing the
key, the LED of this key flashes. The last used cleaning
menu is called up.
The factory settings for the cleaning times are as follows:
- Key 1:
2 minutes
- Key 2:
3 minutes
- Key 3:
5 minutes
In the following example, the preselection key
is programmed for a cleaning
time of 4 minutes:
1. Hold down the
key for approx. 2 seconds.
2. Briefly press the
key:
SET
SET Feeding
2:>03,0<
+
-
SET Feeding
2:>03,5<
SET
2
ESC
INFO
1
2
3
ON
15.07.14
10:30:32
MilkShuttle
105A31
1
1
Cleaning
1: 02:00
Summary of Contents for MilkShuttle
Page 6: ...About these operating instructions 6 ...
Page 28: ...Start up 28 ...
Page 41: ...Operation 41 Figure 6 7 Moving on slopes 9 x ...
Page 42: ...Operation 42 ...
Page 56: ...Programming and calibrating 56 ...
Page 78: ...Maintenance Repairs 78 ...
Page 80: ...Spare parts 80 ...
Page 84: ...Mixing tables 84 ...
Page 86: ...Index 86 ...
Page 87: ...87 Notes ...