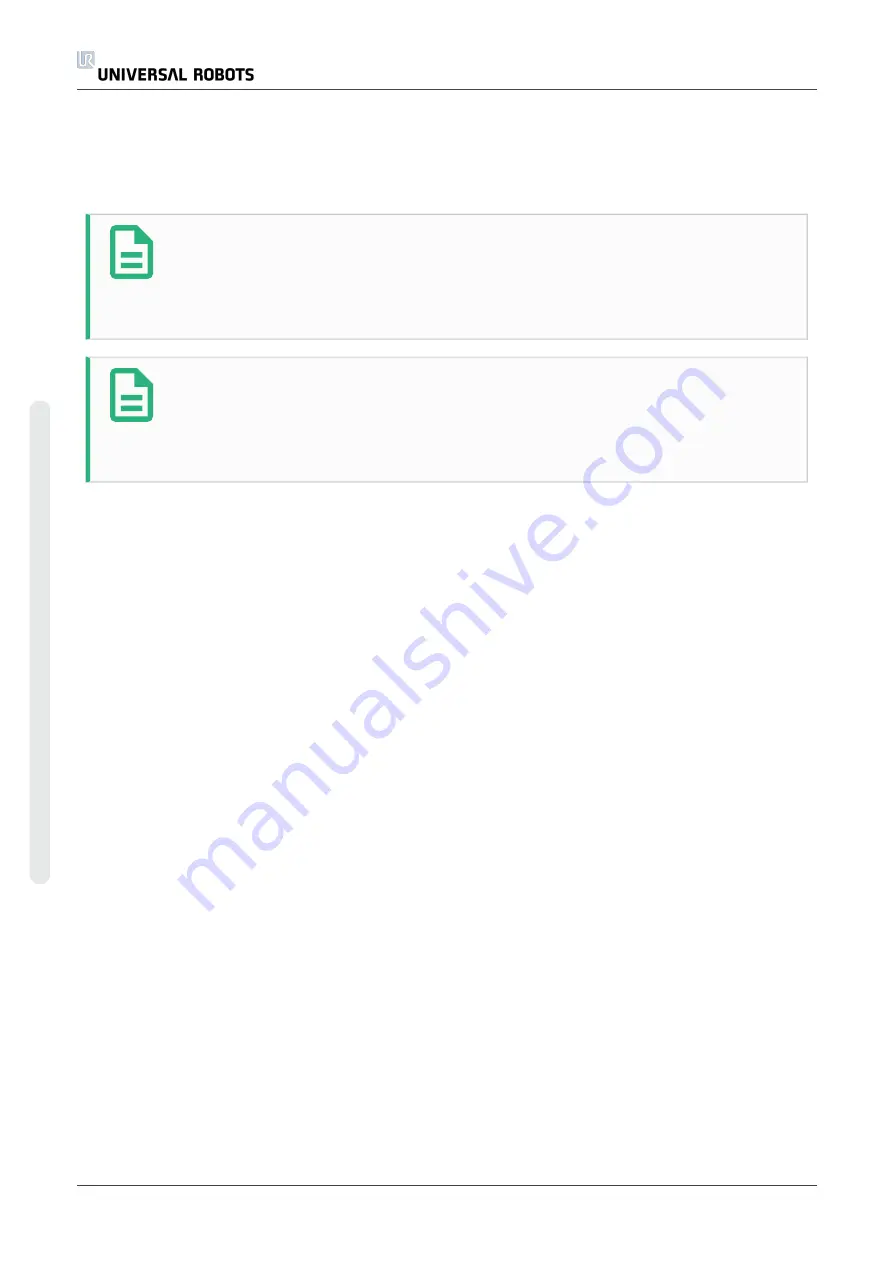
The (normal) state of the signals at startup, is that they are all low, except for the
24V
signals,
and the robot output
Automatic Mode
which is active-low and therefore set high per default.
If a signal is not part of a program structure, and it is intended to be used in a robot program, this
is achievable making use of e.g.
Action
and
Wait
nodes.
NOTE
,,Automatic mode” from the robot to the IMM is active low. The button reflects
the physical level and therefore ,,Automatic mode” is
activated
when the button is
not
activated.
NOTE
The buttons for controlling output signals are per default only availabe in robot
programming mode. This can, however, be set as desired on the
I/O setup
tab
found on the
Installation
screen.
Control
The signals related to controlling the interaction between the robot and the IMM are shown here.
These signals are all used by the program structures, where they have been joined in appropriate
and secure ways.
Manufacturer dependent
These are signals, that may have specific purposes according to the IMM manufacturer. The
robot is not dependant on specifics of these signals, and they can be used as needed.
Safety
In the robot column, the indicators
Emergency Stop
and
Mould Area Free (Electrical)
are not
controlable from this screen. They simply indicate if the robot is emergency stopped, and if the
MAF output is set high. The MAF output is set high under the condition that the electrical
supervision signal of the mould area (possible with use of light guard, as explained above), and
the MAF signal from the software are both high. The MAF signal from software can be controlled
by the respective button. The emergency stop signal from the machine indicates whether the
IMM is emergency stopped. The
Safeguard Open
input shows the state of the ,,Safety devices”
signals specified in the EUROMAP 67 standard.
Status
The operation mode of the robot and the IMM can be controlled/viewed (these signals are also
used in the program structures). The bars showing voltage and current consumption represent
the values delivered to the IMM and possibly a light guard by the EUROMAP 67 module.
UR10
222
User Manual
EUROMAP 67 Interface
C
o
p
yr
ig
h
t
©
2
0
0
9
–
2
0
2
0
b
y
U
n
iv
e
rs
a
l
R
o
b
o
ts
A
/S
.
A
ll
ri
g
h
ts
re
s
e
rv
e
d
.
Summary of Contents for UR10/CB3
Page 1: ...Universal Robots User Manual UR10 CB3 Original instructions en...
Page 28: ...UR10 20 User Manual Copyright 2009 2020 by Universal Robots A S All rights reserved...
Page 30: ...UR10 22 User Manual Copyright 2009 2020 by Universal Robots A S All rights reserved...
Page 36: ...UR10 28 User Manual Copyright 2009 2020 by Universal Robots A S All rights reserved...
Page 56: ...UR10 48 User Manual Copyright 2009 2020 by Universal Robots A S All rights reserved...
Page 62: ...UR10 54 User Manual Copyright 2009 2020 by Universal Robots A S All rights reserved...
Page 64: ...UR10 56 User Manual Copyright 2009 2020 by Universal Robots A S All rights reserved...
Page 72: ...China RoHS UR10 64 User Manual Copyright 2009 2020 by Universal Robots A S All rights reserved...
Page 73: ...KCC Safety User Manual 65 UR10 Copyright 2009 2020 by Universal Robots A S All rights reserved...
Page 92: ...UR10 84 User Manual Copyright 2009 2020 by Universal Robots A S All rights reserved...
Page 116: ...UR10 108 User Manual Copyright 2009 2020 by Universal Robots A S All rights reserved...
Page 124: ...UR10 116 User Manual Copyright 2009 2020 by Universal Robots A S All rights reserved...
Page 164: ...UR10 156 User Manual Copyright 2009 2020 by Universal Robots A S All rights reserved...
Page 214: ...UR10 206 User Manual Copyright 2009 2020 by Universal Robots A S All rights reserved...