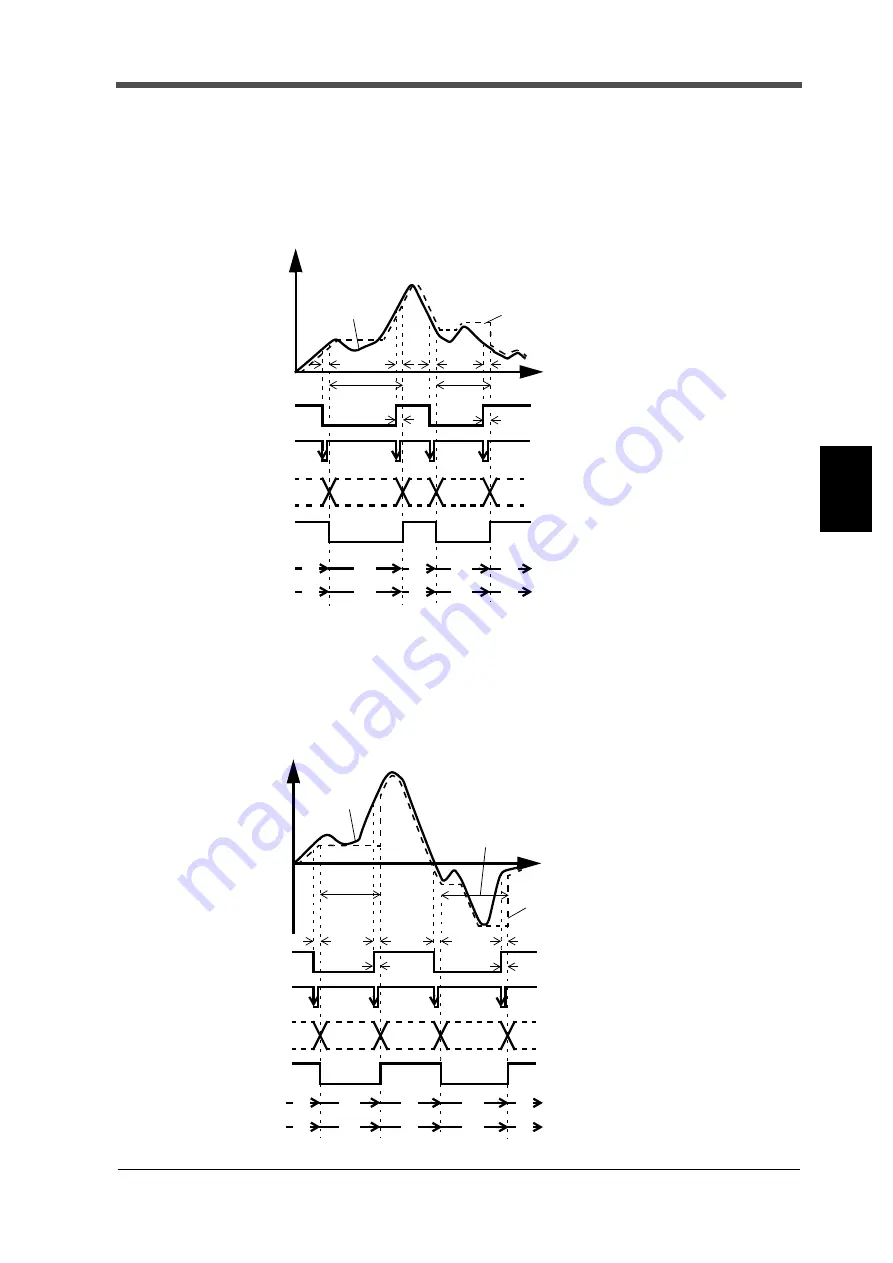
5
SETTING OF FUNCTIONS
51
SETTING OF FUNCTIONS
Chapter
5
Peak hold
The maximum value (peak) in the positive direction of the specified section is held.
The section is specified by the setting of “all section”, “external signal”, “external time”,
“level+time”, or “level”.
(Example) All section peak hold
t1: A delay time between the instant
when the T/H signal is inputted and the
instant when the indicated value is held
1.0ms (max.)
t2: A delay time between the instant
when the T/H signal is released and the
instant when the indicated value returns
to tracking
1.0ms (max.)
t3: A minimum reset signal width
required for releasing the hold
1.0ms (min.)
Note: During the undetermined section, the
judging output varies with fluctuations in the
input waveform. However, the H/E output
remains on during the undetermined section.
Read the judging result when the indicated
value becomes stable (immediately before the
T/H signal rises).
Valley hold
The maximum value (valley) in the negative direction of the specified section is held.
The section is specified by the setting of “all section”, “external signal”, “external time”,
“level+time”, or “level”.
(Example) All section valley hold
t1: A delay time between the instant
when the T/H signal is inputted and the
instant when the indicated value is held
1.0ms (max.)
t2: A delay time between the instant
when the T/H signal is released and the
instant when the indicated value returns
to tracking
1.0ms (max.)
t3: A minimum reset signal width
required for releasing the hold
1.0ms (min.)
Note: During the undetermined section, the
judging output varies with fluctuations in the
input waveform. However, the H/E output
remains on during the undetermined section.
Read the judging result when the indicated
value becomes stable (immediately before the
T/H signal rises).
Indicated Value
t2
t3
Sensor Input Value
Detection
t
+
T/H
HI-LO Limit
Judging Output
H/E
Detection
t1
t2
t1
t3
OFF
ON
OFF
ON
OFF
ON
OFF
ON
Status Display
PEAK
Status Display
ON
Blink
Blink
OFF
ON
OFF
OFF
OFF
OFF
OFF
HOLD
Button
Undetermind
section (Note)
Undetermind
section (Note)
Hold Section
Hold Section
HOLD
Indicated Value
t2
t3
Sensor Input Value
Detection
t
+
T/H
HI-LO Limit
Judging Output
H/E
Detection
・
Hold Section
t1
t2
t1
t3
OFF
ON
OFF
ON
OFF
ON
OFF
ON
HOLD
Status Display
VLLY
Status Display
ON
Blink
Blink
OFF
ON
OFF
OFF
OFF
OFF
OFF
HOLD
Button
Undetermind
section (Note)
Undetermind
section (Note)
Hold Section
Summary of Contents for F377A
Page 1: ...18JUL2012REV 3 06 DIGITAL INDICATOR F377A OPERATION MANUAL ...
Page 5: ...What is RoHS 4 M E M O ...
Page 12: ...11 11 STANDARD ...
Page 13: ...12 12 M E M O ...
Page 94: ...93 93 EXPANSION ...
Page 95: ...94 94 M E M O ...
Page 97: ...Expansion Function 96 M E M O ...
Page 152: ......