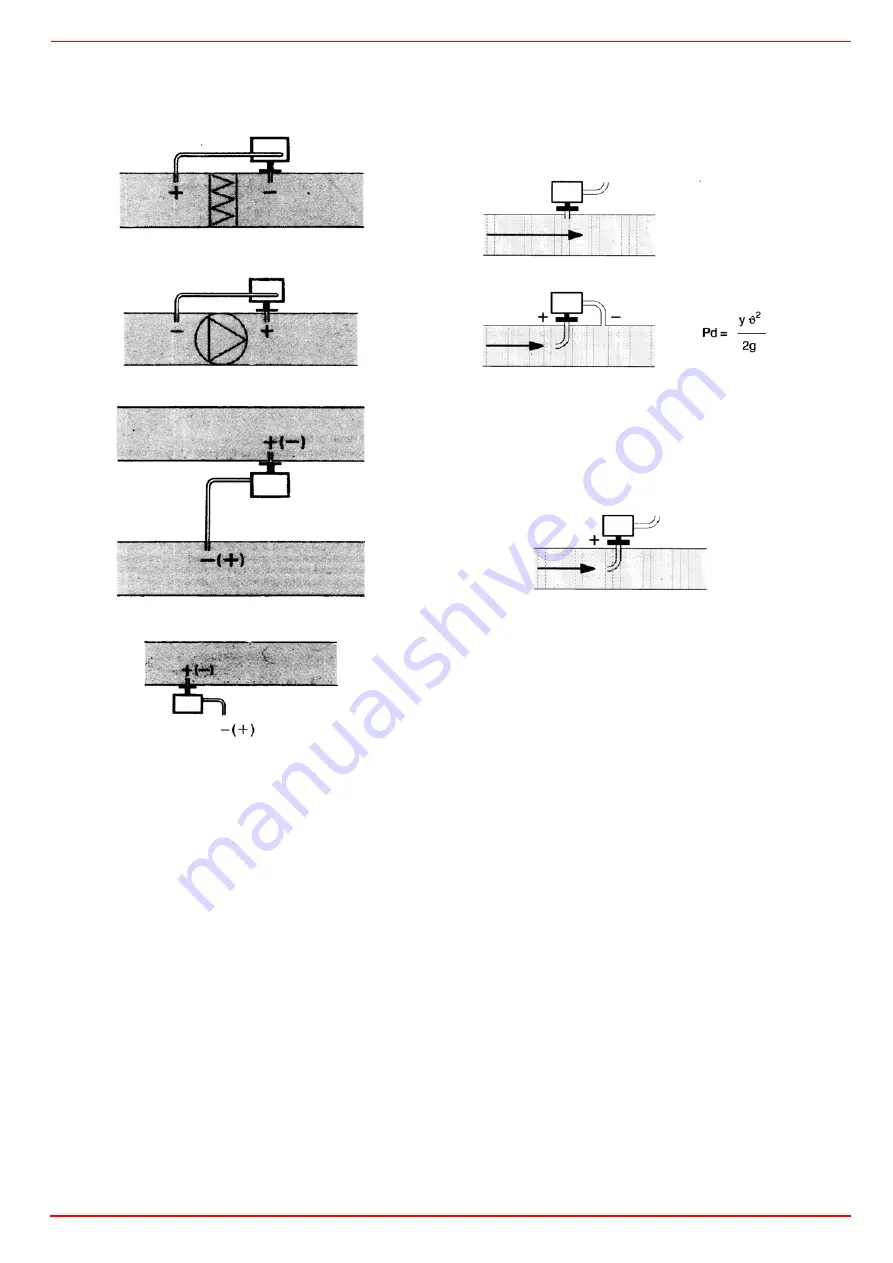
22
Duct pressure switches and sensors
Installing differential pressure probes for air
A - Control a filter (clogging)
B - Control a fan (upstream/downstream)
C - Measurement of difference in pressure between two ducts
D - Measurement of difference in pressure between two rooms or
of inside of duct and outside
Basic principles
Measuring static pressure(i.e. pressure exerted by air on pipe
walls)
Measuring dinamic pressure
Legend
y
Kg/m3, specific weight of air
q
m/s, air speed
g
9.81 m/s2 gravity acceleration
Pd
mm C.A., dynamic pressure
Measuring total pressure
Summary of Contents for PBY1025
Page 40: ...C I B UNIGAS M039126CE 40...
Page 47: ......
Page 48: ......
Page 49: ......
Page 50: ......
Page 51: ......
Page 52: ......
Page 53: ......
Page 54: ......
Page 55: ......
Page 56: ......
Page 57: ......
Page 58: ......
Page 59: ......
Page 60: ......
Page 61: ......
Page 62: ......
Page 63: ......
Page 64: ......
Page 65: ......
Page 66: ......
Page 67: ......
Page 68: ......
Page 69: ......
Page 70: ......
Page 71: ......
Page 72: ......
Page 73: ......
Page 74: ......
Page 75: ......
Page 76: ......
Page 77: ......
Page 78: ......
Page 79: ......
Page 81: ...RWF55 5X RWF55 6X User manual M12926CA Rel 0 2 11 2023...
Page 82: ...2 DEVICE INSTALLATION Fixing system Drilling dimensions...
Page 103: ......
Page 104: ...23 Note Specifications and data subject to change Errors and omissions excepted...
Page 113: ......
Page 114: ......
Page 115: ......
Page 116: ......
Page 117: ......
Page 118: ......
Page 119: ......