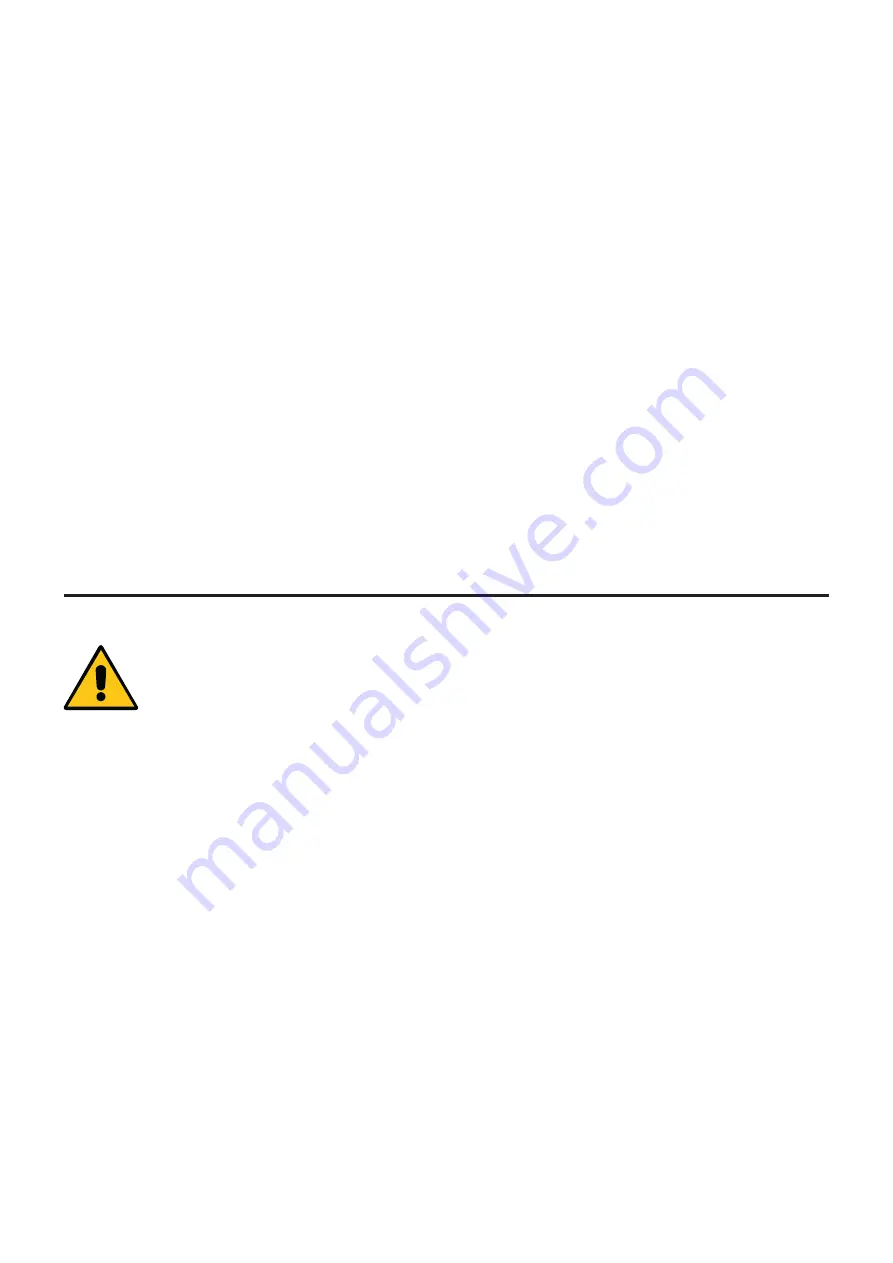
42
3.23 - ADJUSTING THE BURNER
The following instructions are intended exclu-
sively for service personnel
authorised by the
manufacturer of the burner
.
Burner calibration and preliminary operations are described in
the burner's instruction booklet.
Gas-fired burners are equipped with a gas valve with which the
flow rate can be determined: upon commissioning the actual
thermal flow rate
must always
be controlled by means of the
counter on the main piping, making sure it is not below the
minimum value on the data plate of the boiler.
When the burner is adjusted properly, the following values should
be obtained, measured at the chimney by a specific analyser:
1)
for diesel oil with max visc. 1.5°E at 20°C:
- CO2 ~ 12÷13%
- Bacharach flue gas index ‹1
- Flue gas temperature ~ 190÷210 °C
2) with natural gas:
- CO2 ~ 9÷10%
- Flue gas temperature ~ 180÷200°C
(values for boiler cleaned with water at ~ 70°C).
The flow rate of the fuel should be adjusted to the actual re-
quirement of the system without, on the one hand, exceeding
the indicated flue gas temperature and on the other, without
dropping below 160°C.
3.22.2 - Ignition and extinction
Ignition
When the checks indicated in the previous paragraph are suc-
cessful, the burner can be commissioned by a technician quali-
fied and acknowledged by the Manufacturer of the burner.
The technician takes on all responsibility regarding calibration
within the declared and approved output range of the boiler.
After having opened the fuel shut-off valves and made sure
there are no leaks in the adduction circuit, set all switches at
ON.
The burner is now ready for commissioning and adjustment,
performed solely by the above-mentioned technician.
During commissioning, you must check that the door, the burn-
er flange and connections with the chimney are airtight and that
there is a slight negative pressure at the base of the flue.
The fuel flow rate must correspond to the plate data of the boil-
er. It must by no means exceed the maximum declared nominal
output value.
The flue gas temperature must never drop below 160°C.
Extinction
- Set the operating thermostat at minimum.
- Disconnect power to the burner and close the fuel supply.
- Leave the pumps running until they are stopped by the mini-
mum thermostat.
- Disconnect power to the electric panel.