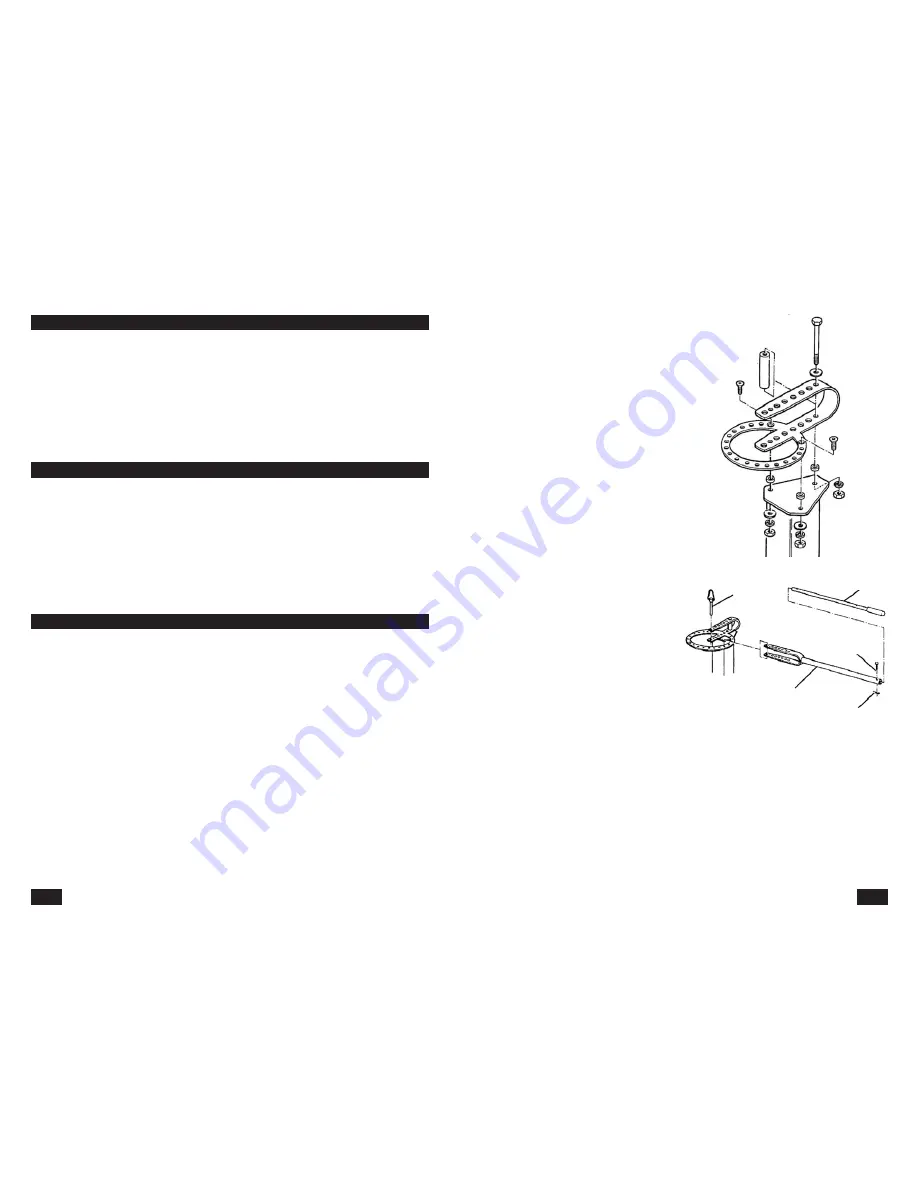
36
•
Keep your tools clean. Dirt may enter the inner mechanism of your machine and cause damage.
•
Do not use aggressive cleaning solution or paint thinners to clean the machine.
•
Clean plastic parts with cloth dipped in soup water.
•
Clean and lubricate metal surfaces with a cloth dipped in paraffin oil.
•
If you are not using your machine, lubricate it with suitable grease and store it in a dry place to prevent
corrosion.
Lubrication
Lubricate working surfaces with suitable grease regularly.
When the operational life of your device is over, dispose off it in accordance with valid rules and regulations.
Your product is made of metal and plastic parts that may be recycled when separated.
1. Disassemble all parts.
2. Separate all parts according to the material they are made of (e.g. metals, rubber, plastics, etc.).
Take the separated parts to the recycling facility near you.
Information about the locations of recycling centres may be found at your local City office or throughout an
Internet search.
If the machine breaks down, send it back to the vendor for quick repair.
Please, enclose brief description of the defect. That makes repair easier. If the machine is still covered by
warranty, enclose the warranty card and proof of purchase receipt. After the warranty period expires, we
repair your machine for a special price.
To prevent possible damages during shipping, packed the machine carefully or use the original packaging
material. We are not liable for shipping damages due to incorrect packaging of your machine. If making
a claim at the shipping company the level and method of packaging plays a major role during claim evaluation
process.
Note:
Pictures and contents in this manual may slightly differ from the actual product or accessories.
It is due to continuous improvement of our products. Such small differences have no effect on the product
functionality.
DISPOSAL
CAUTION
MAINTENANCE
5
Assembling procedure
•
Connect the bent part with the round base,
using screw 3/8", flat washer, thick distance
washer (that is placed on the screws inside
the fold), thin distance washers, spring washers
and nuts.
•
Place the bent part of the handle (with the holes)
inside the base fold and secure in place with
one or both long connecting studs.
•
Remove the clamp from the handle stud and pull
the stud out. Pull the extension arm out, push
the stud in the inner hole and replace the clamp
back.
•
Put the machine in final position, where it will
be used. Turn the handle in both directions, to
make sure that no obstacles are within the reach
of the handle.
•
Make sure that there is enough space behind the machine to handle long work pieces. If you need to
place the machine close to a wall, tray to place it according to the drawing on the picture.
CAUTION:
Do not use the machine if it is not securely mounted to a work table or to the floor. Severe
injuries may occur.
screw 3/8"
thick
distance
spacer
flat washer
thin distance
spacer
elastic washer
nut
flat washer
elastic washer
nut
mount
stud
extension
arm
handle
safety pin
handle stud