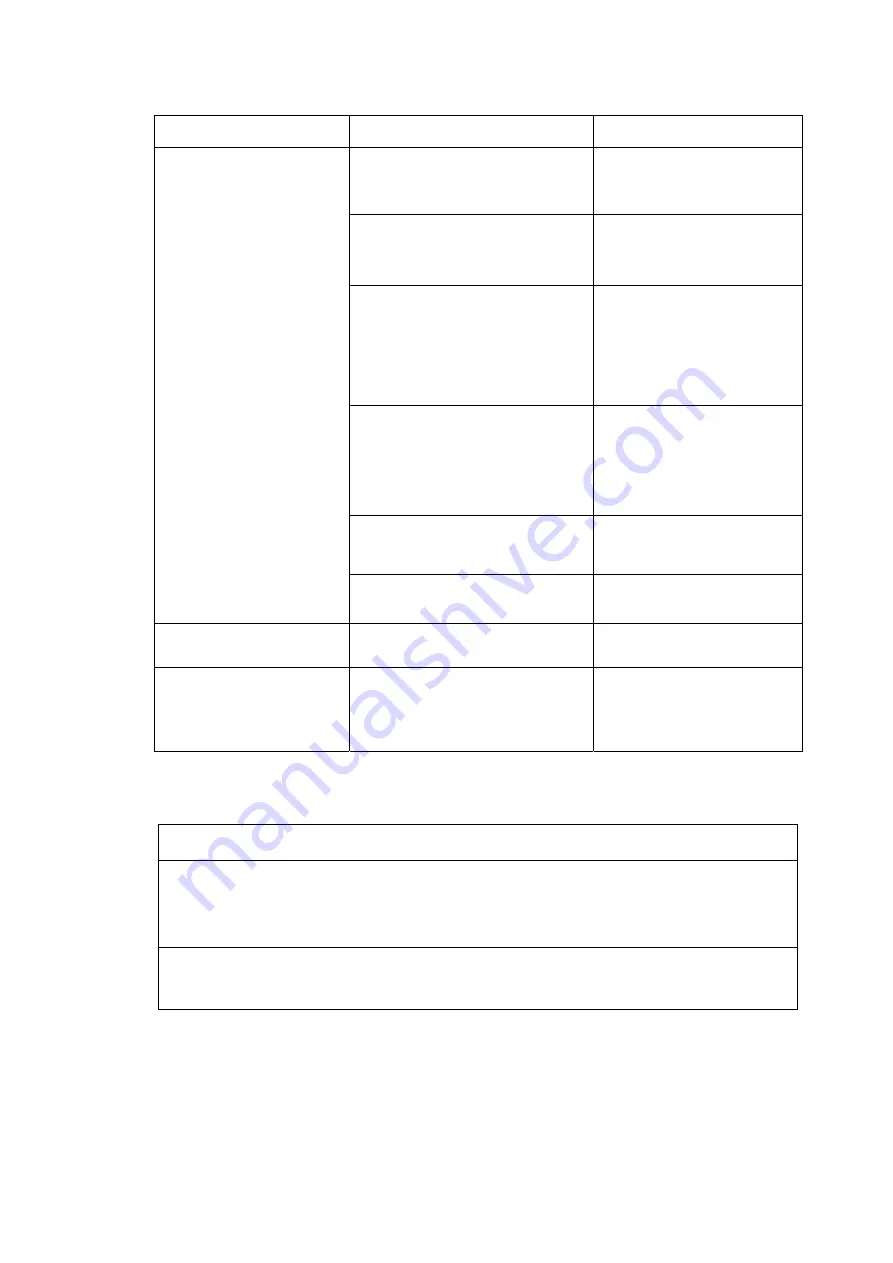
14
5. Troubleshooting
Symptom
Cause
Troubleshooting
Ultimate pressure is
low or unstable, or
evacuation
performance is low.
The ambient temperature at
the installation site is high.
Decrease the ambient
temperature to 25°C by
cooling.
Operation time is too long
after installation or long
termination.
Operate 24 hours to 48
hours, and then perform
checking.
Leakage is detected.
Check components that
were maintained before
ultimate pressure
changes.
Deterioration of the oil for
the oil diffusion pump.
If the cause of the
deterioration is clear
(incorrect air intake,
leakage, etc.), replace
the oil.
Failure in the oil sealed
vacuum pump
Refer to the Oil Sealed
Vacuum Pump User’s
Manual.
Failure in measuring
instrument
Replace the measuring
instrument.
The oil diffusion pump
stays cold.
The heater is disconnected. Replace the heater.
The thermal relay for
oil sealed vacuum
pump operates.
Overloaded
Refer to the Oil Sealed
Vacuum Pump User’s
Manual.
Thermal relay set
6. Storage of Equipment
Observe the following guidelines to store the equipment.
1) Place of storage
- Floor with sufficient strength - Location with good ventilation
- Location without direct sunlight - Location where no corrosive
chemicals or gases are present.
2) Cautions before and upon storing
- Perform roughing evacuation inside the chamber