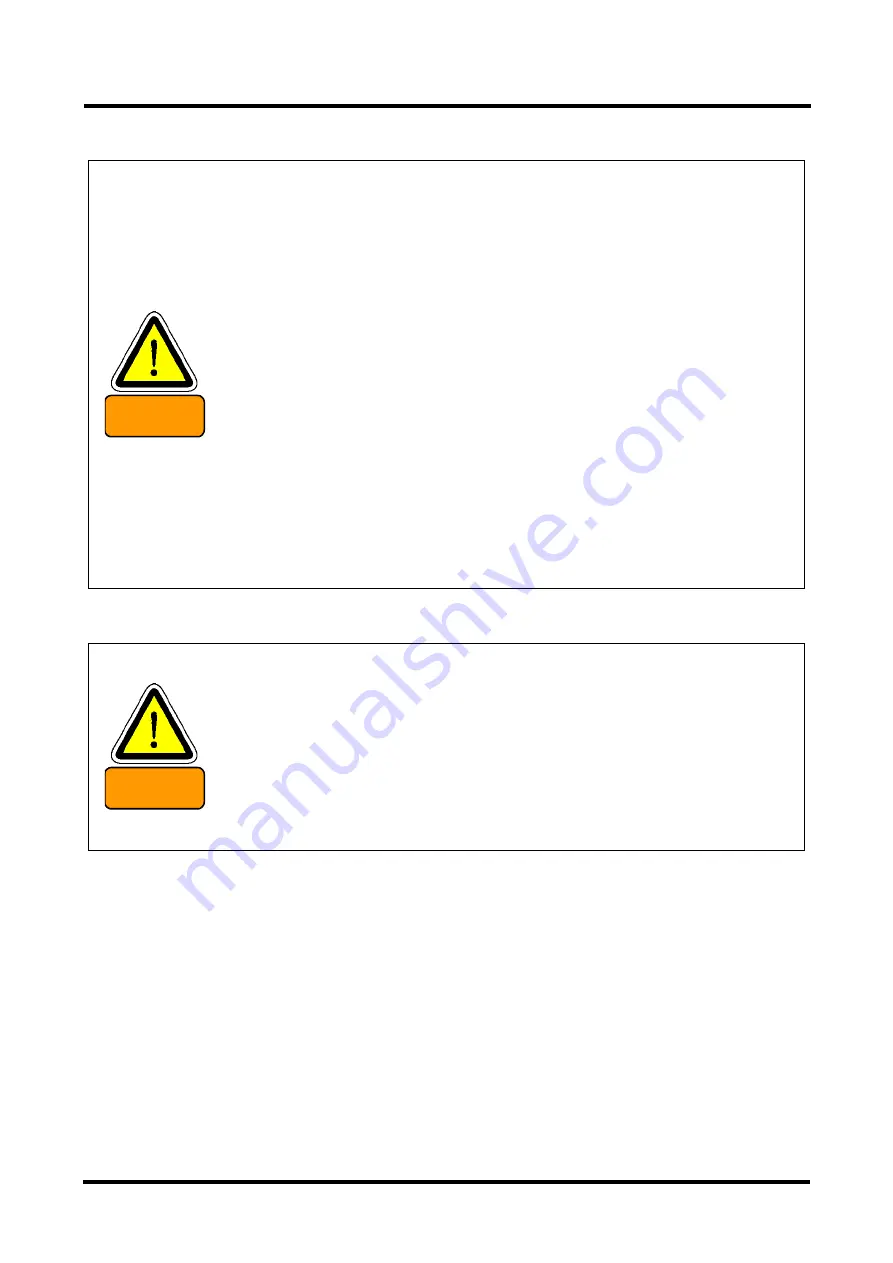
YK08-0028-DI-002-08
v
Installation and storage
WARNING
1) When taking out the product from the box and lifting up the pump,
guide to use the cargo-handling equipment such as a crane utilizing
the eyebolt located at the upper part of the pump and to transfer lifting
it up. Confirm that there is no abnormality before using the eyebolts.
2) Only the technically entitled person should be in charge of conducting
the unloading operation and operating the unloading machinery.
3) There is a risk that the Pump might drop or lay down when attempted
unreasonable operation or machinery setup was not sufficient. You
are strictly restricted to enter beneath the Pump.
4) Since you may get injury due to an anchor being used in the box,
guide the worker to wear the leather gloves and to use the appropriate
tool.
Transfer
WARNING
Pump Weight
VD151
:
29kg
VD201
:
34.5kg
When you carry a pump, you have a risk of giving damage to your back.
Be sure to use the loading machinery (such as mobile crane) to lift up
the Pump or load it on the pallet and fix it and run the Pallet truck for its
transfer.