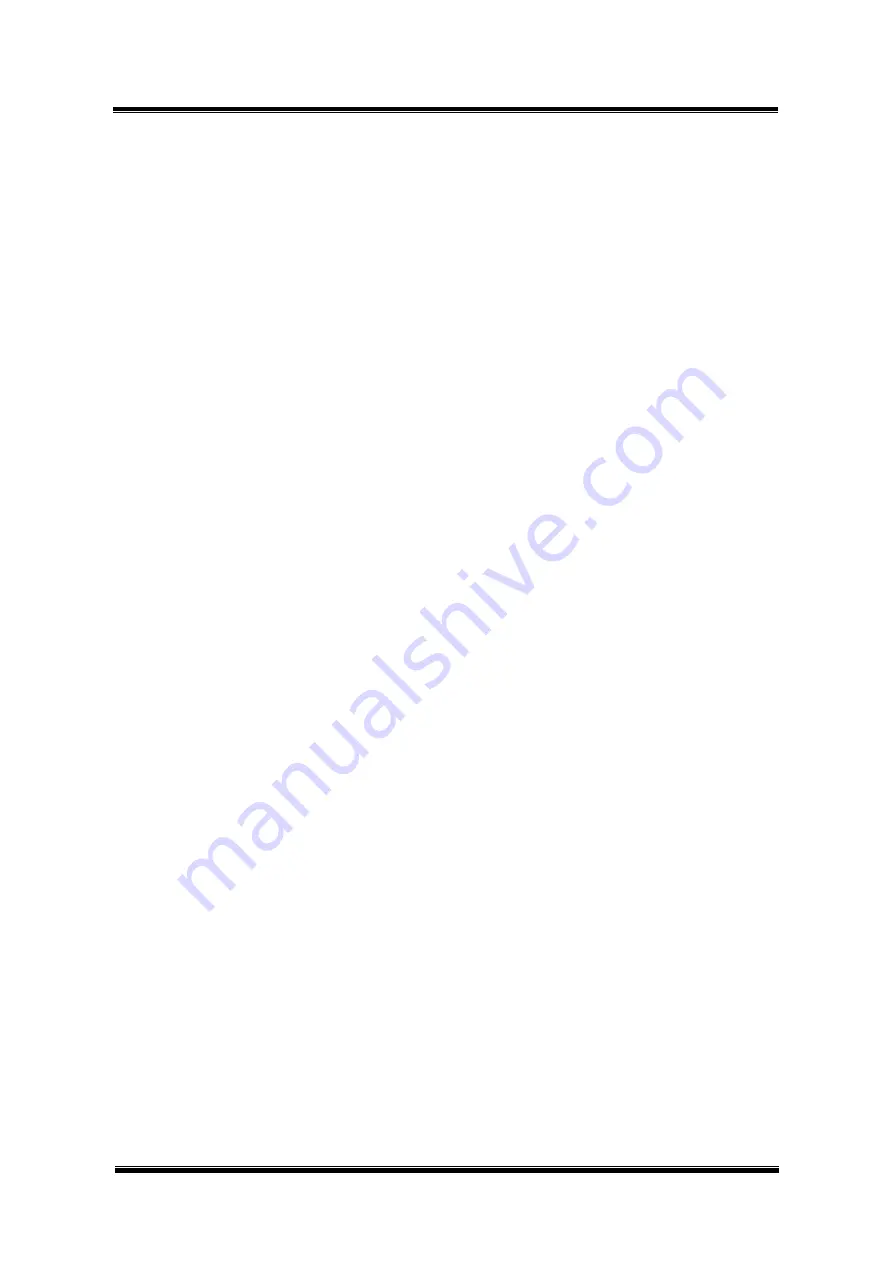
Page 26
M4220170607EN
UI Robot Technology Co. Ltd.
UIM2842
4.2 Enable/Disable RTCN
Every RTCN can be enabled or disabled through user instruction.
Enable/disable the
RTCN is achieved by the writing to the Master Configuration Register’s ORGIE bit
(MCFG<5>), STPIE bit (MCFG<4>), P4IE bit (MCFG<3>), S3IE bit (MCFG<2>), S2IE bit
(MCFG<1>) and S1IE bit (MCFG<0>). Please refer to section 4.1 for details.
Please note, to realize the sensor event control, user needs to further configure the sensor
control registers S34CON and S12CON. Please refer to Chapter 8.0 and Chapter 10.0 for
details.