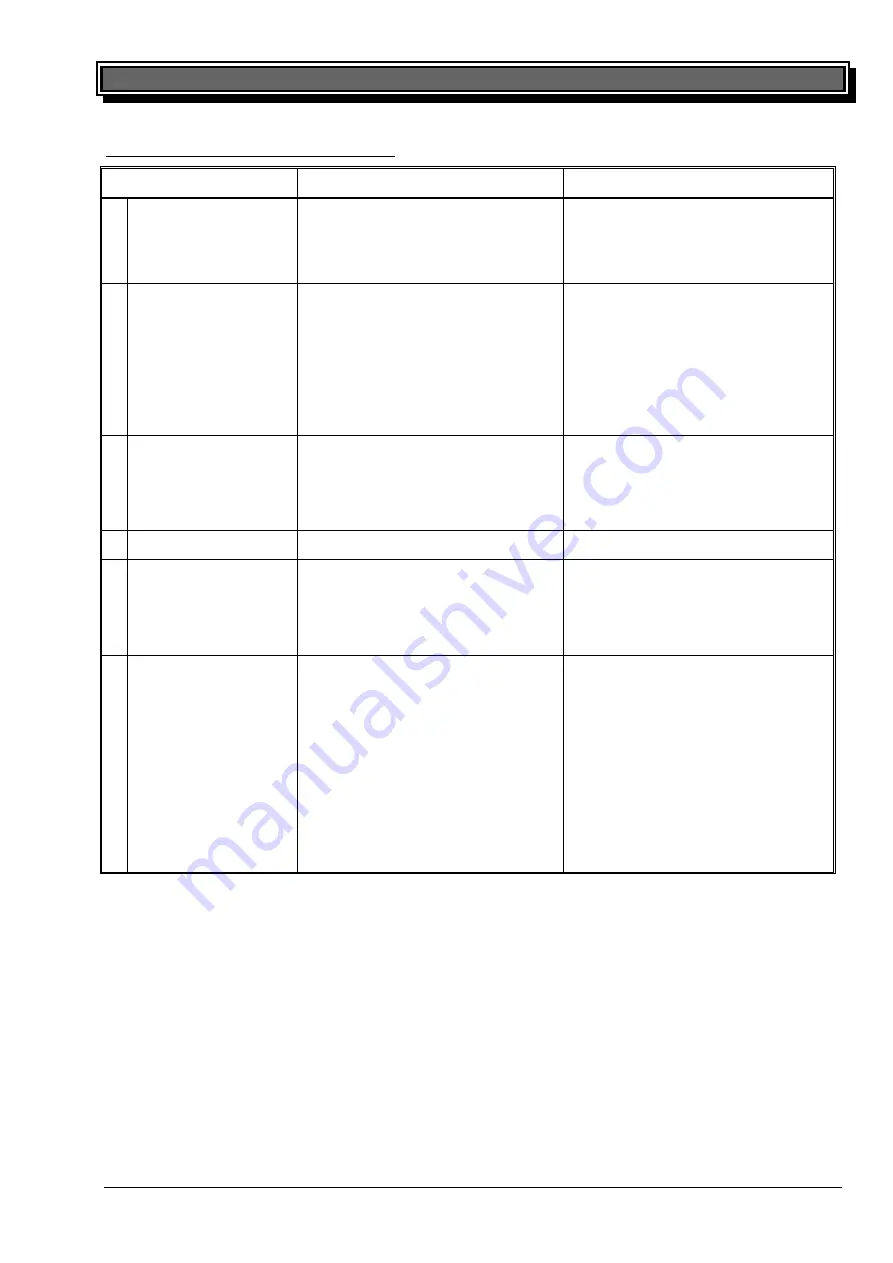
Maintenance
29
Printed: 01/2018 Subject to change!
TopLineUserManual.docx
Check list of your Rotisserie „Top Line“:
Failure
Possible cause
Remedy
1. Rotisserie does not
operate
Electrical supply is interrupted
Check the fuses!
Unpluged?
Fuse defect
Call your local electrician!
2. Fan motor does not
work
mechanic hindrances
Switch off the unit, remove the
cover with ventilation grid, check
the ventilation on mechanic
hindrances (e.g. hardened fat
residues – remove these carefully)!
Fan motor defect
Call your service company. Do not
start the unit!
3. Quartz lamp is off
is not switched on.
Check the position of switch on/off
knob.
Lamp is defect.
Replacement of the quartz lamp by
a local electrician.
4. Noisy motor
Motor or gear is defect.
Call the service company!
5. Spit disks do not
rotate.
Motor protection device has set.
Push the motor protection control
one time, if it sets again call the
service!
Doors are not closed (RT307 only) Close the doors!
6. Rotisserie does not
reach the required
temperature.
Electrical supply is not o.k.
Check the fuse box!
Heating elements are defect.
Call the service!
Fan defect.
See point 2 or call the service!
Thermostat defect.
Call the service!
7. Difference between
programmed and real
time periods
Programming clock is defect.
Call the service!
Summary of Contents for Top Line
Page 1: ...User Manual Rotisseries Top Line RT Series ...
Page 2: ......