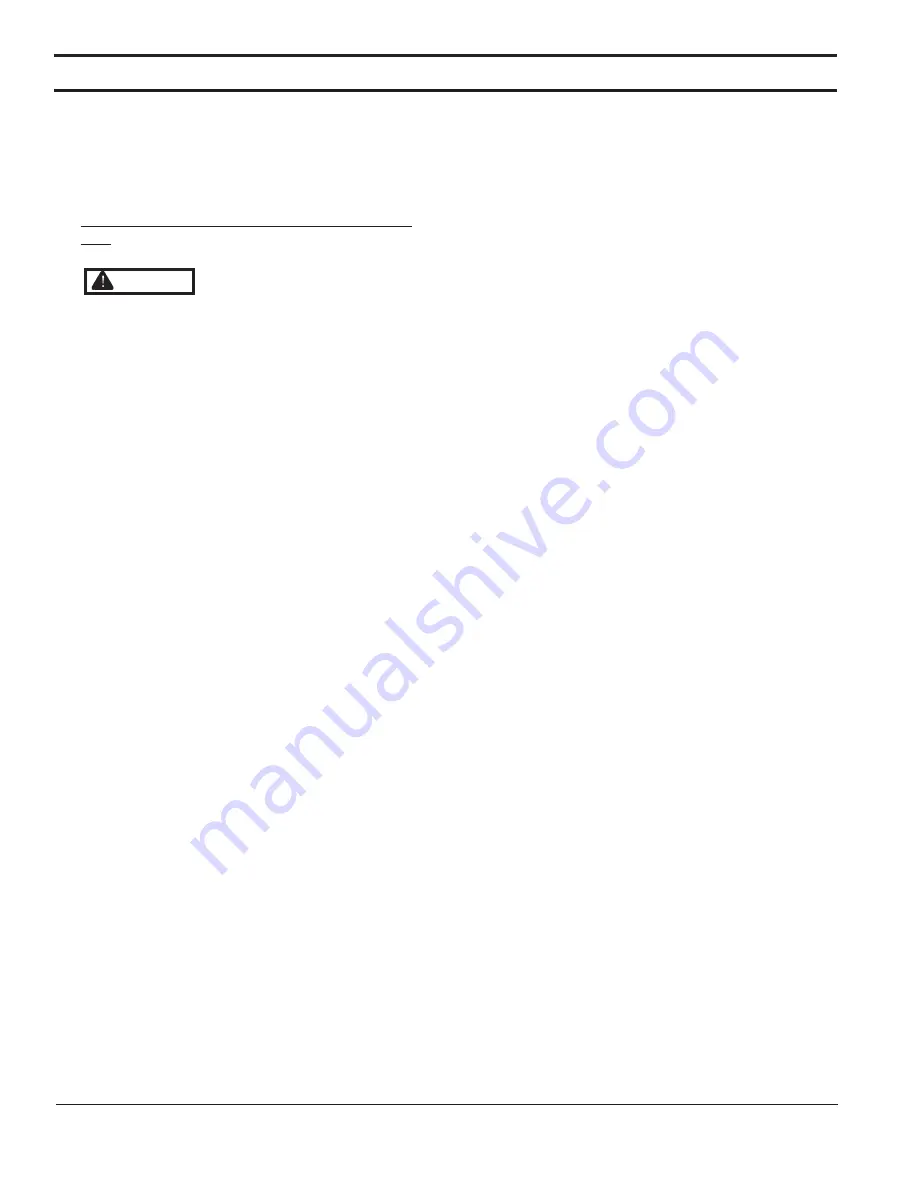
8
103536-08 - 4/18
5. For minimum clearances to combustible
materials. See Figure 2.
C.
PROVIDE COMBUSTION AND VENTILATION
AIR.
Local and National Codes may apply and
should be referenced.
1. Determine volume of space (boiler room).
Rooms communicating directly with the
space in which the appliances are installed,
through openings not furnished with doors, are
considered a part of the space.
Volume(ft
3
) = Length(ft) x Width(ft) x Height(ft)
2. Determine total input of all appliances in the
space.
Add inputs of all appliances in the space and
round the result to the nearest 1000 BTU per
hour.
3. Determine type of space. Divide Volume by
total input of all appliances in space. If the
result is greater than or equal to 50 ft
3
/1000
BTU per hour, then it is considered an
unconfined space
. If the result is less than
50 ft
3
/1000 BTU per hour then the space is
considered a
confined space.
4. For boiler located in an
unconfined space of a
conventionally constructed building,
the fresh
air infiltration through cracks around windows
and doors normally provides adequate air for
combustion and ventilation.
5. For boiler located in a confined space or an
unconfined space in a building of
unusually
tight construction,
provide outdoor air.
a. Outdoor air for combustion may be
provided with an optional U.S. Boiler
Company Fresh Air Accessory Kit,
(ONLY
AVAILABLE WITH BECKETT BURNER
-
P/N 102119-01). Refer to Fresh Air
Accessory Kit Instructions for installation
and air intake piping details.
or
b. Outdoor air may be provided with the
use of two permanent openings which
communicate directly or by duct with the
outdoors or spaces (crawl or attic) freely
communicating with the outdoors. Locate
one opening within 12 inches of top of
space. Locate remaining opening within
12 inches of bottom of space. Minimum
dimension of air opening is 3 inches. Size
each opening per following:
i.
Direct communication with outdoors.
Minimum free area of 1 square inch
per 4,000 BTU per hour input of all
equipment in space.
ii.
Vertical ducts.
Minimum free area of
1 square inch per 4,000 BTU per hour
input of all equipment in space. Duct
cross-sectional area shall be same as
opening free area.
iii.
Horizontal ducts.
Minimum free area of
1 square inch per 2,000 BTU per hour
input of all equipment in space. Duct
cross-sectional area shall be same as
opening free area.
Alternate method for boiler located
within confined space.
Use indoor air if
two permanent openings communicate
directly with additional space(s) of
sufficient volume such that combined
volume of all spaces meet criteria for
unconfined space. Size each opening
for minimum free area of 1 square inch
per 1,000 BTU per hour input of all
equipment in spaces, but not less than
100 square inches.
6. Louvers and Grilles of Ventilation Ducts
a. All outside openings should be screened
and louvered. Screens used should not be
smaller than 1/4 inch mesh. Louvers will
prevent the entrance of rain and snow.
b. Free area requirements need to consider
the blocking effect of louvers, grilles, or
screens protecting the openings. If the free
area of the louver or grille is not known,
assume wood louvers have 20-25 percent
free area and metal louvers and grilles have
60-75 percent free area.
c. Louvers and grilles must be fixed in the
open position, or interlocked with the
equipment to open automatically during
equipment operation.
Section I: Pre-Installation (continued)
NOTICE
Clearance to venting is for single wall
vent pipe. If Type L vent is used, clearance
may be reduced to the minimum required by
the vent pipe manufacturer.
Adequate combustion and
ventilation air must be provided to assure
proper combustion and to maintain safe
ambient air temperatures.
Do not install boiler where gasoline or other
flammable vapors or liquids, or sources of
hydrocarbons (i.e. bleaches, fabric softeners,
etc.) are used or stored.
Do not install boiler in laundry room, or, in
vicinity of clothes dryer to prevent inadequate
air supply to burner and lint contamination of
burner air intake openings.
WARNING
Summary of Contents for MegaSteam MST288
Page 54: ...54 103536 08 4 18 Bare Boiler Assembly Section XII Repair Parts continued...
Page 56: ...56 103536 08 4 18 Bare Boiler Assembly Section XII Repair Parts continued...
Page 58: ...58 103536 08 4 18 Jacket Assembly Section XII Repair Parts continued...
Page 62: ...62 103536 08 4 18 Beckett AFG Burner Section XII Repair Parts continued...
Page 65: ...65 103536 08 4 18...
Page 66: ...66 103536 08 4 18...
Page 67: ...67 103536 08 4 18...