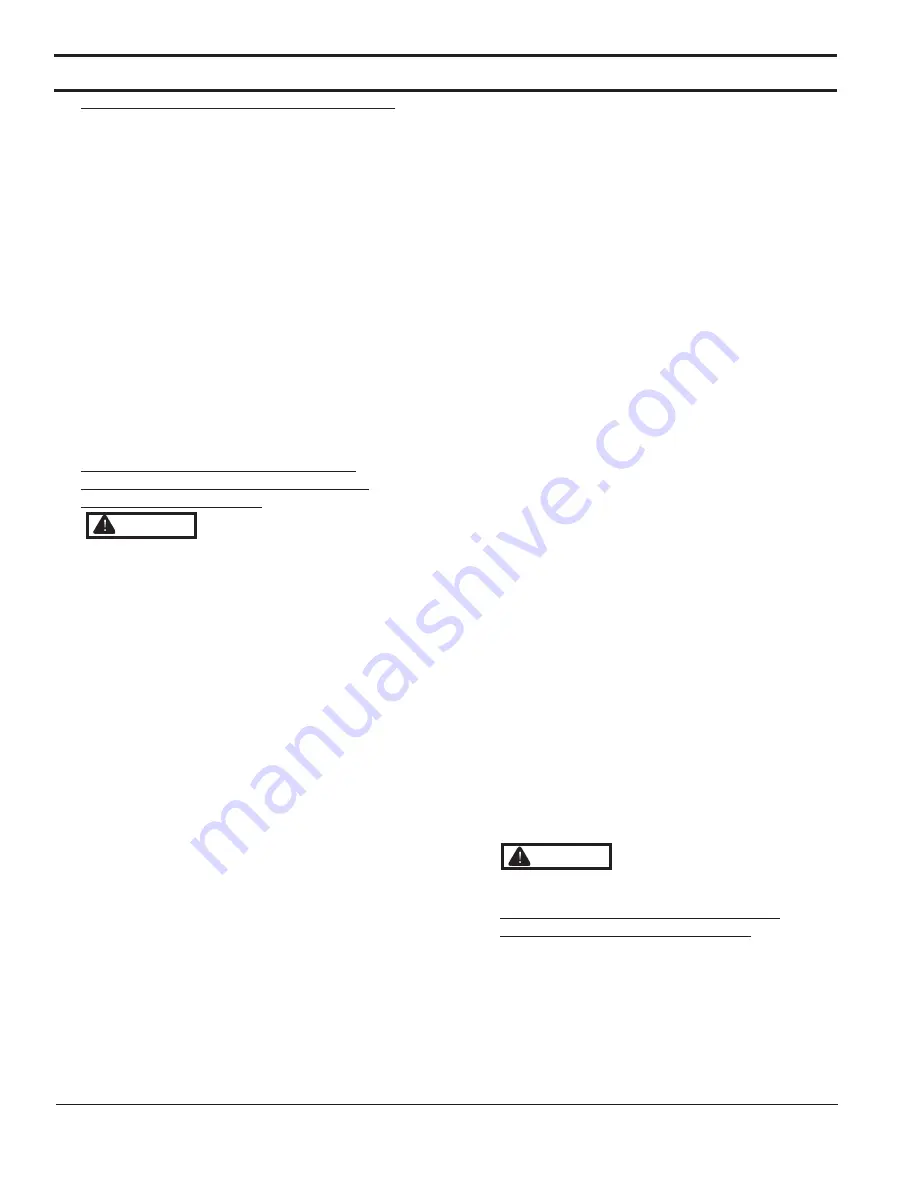
10
103536-08 - 4/18
A. CAST IRON SECTION ASSEMBLY TAPPINGS
Refer to Table 3 "Purpose of Tappings and
Bosses" and Figure 7.
1. All tappings have factory installed thread
protectors. The thread protectors must be
removed prior to jacket and piping installation.
2. Depending of installation specifics and boiler
build ordered, some tappings (front section
Optional Front Return, rear section Indirect
Heater Supply and Indirect Heater Limit) may
not be used and must be plugged before
jacket and piping installation. The appropriate
size plugs for above mentioned tappings,
as well as rear section Surface Blowoff and
front section probe type LWCO tappings,
are enclosed into Part Cartons (100615-01
or 100629-01) and Control Cartons (100678-
01 and 100679-01), supplied as part of
MegaSteam™ Unit-Pak Boiler shipment.
B. REMOVAL OF CAST IRON SECTION/
BURNER SWING DOOR / SMOKE BOX
ASSEMBLY FROM SKID.
1. Move crated Cast Iron Section/Burner
Swing Door/Smoke Box Assembly and part
cartons on the shipping skid as close to final
permanent location as possible.
2. Remove all fasteners at crate skid. Lift outside
container. Examine the skid contents for
damage due to shipping and handling.
3. Remove Insulation Wrapper, Control Carton,
Jacket Carton and Part Carton from skid and
set aside.
4. Instruction/Label Bag is affixed to Section
Assembly tie rod. Remove the bag and locate
MegaSteam™ Boiler Installation, Operating
and Service Instruc-tion manual. READ AND
UNDERSTAND ALL INSTRUCTIONS BEFORE
ATTEMPTING BOILER HANDLING AND
INSTALLATION.
5. The Cast Iron Section/Burner Swing Door/
Smoke Box Assembly is secured to shipping
skid with four lag screws. Remove the screws
and discard.
6. For manual Cast Iron Section/Burner Swing
Door/Smoke Box Assembly removal prepare
one piece of 4” x 4” x 16” lg. (or two pieces of
2” x 4” x 16” lg.) and two pieces of 1” Sch. 40
black pipe to be used as handles. Suggested
pipe length for each handle is 72” (3-section);
78” (4-section) and 84” (5-section).
7. Place wooden block(s) 12” from rear of skid
as shown. See Figure 4 “ Boiler Removal from
Skid”.
8. Insert 1” Sch. 40 black pipe handles thru leg
holes in front and rear section legs. Center rear
pipe ends on wooden block(s). See Figure 4.
9. For best leverage, the pipe handles should
extend 48” minimum beyond front section face.
10. Using the pipe handles, lift the Cast Iron
Section/Burner Swing Door/Smoke Box
Assembly until adjustable legs are elevated
above the skid deck boards.
11. Remove the skid from underneath the Cast
Iron Section/Burner Swing Door/Smoke Box
Assembly.
12. Lower pipe handles until front adjustable legs
touch the floor. Place wood blocks under front
legs, if required, before lowering, to provide
hand clearance.
13. To lower rear of the Cast Iron Section/Burner
Swing Door/Smoke Box Assembly tilt boiler
slightly forward by pushing on smokebox, or,
lift pipes protruding thru rear legs, until wooden
block(s) can be removed (see Figure 4). Slowly
allow the weight of boiler to tilt backward until
rear legs rest on floor.
14. If wood blocks were placed under front legs,
lift pipe handles; remove the blocks and lower
front legs to floor. Remove pipe handles.
15. Move Cast Iron Section/Burner Swing Door/
Smoke Box Assembly to permanent position by
sliding or walking.
C. PROCEDURE TO OPEN, CLOSE AND
SECURE BURNER SWING DOOR.
Throughout this manual you will be instructed to
open and close Burner Swing Door for various
reasons. There is a proper and improper method
of closing and securing the door opened for front
jacket panel installation, inspection, cleaning or
field service. Refer to Figures 5A, 5B, 5C and
paragraphs D “Jacket Front Panel Installation”,
and, F “Closing/Securing Burner Swing Door” for
details.
Section II: Unit-Pak Boiler Assembly (continued)
The Cast Iron Section/Burner
Swing Door/Smoke Box Assembly has a
substantial weight. Insure the travel path
to permanent location, as well as mounting
surface at boiler permanent location, are
structurally sound and rated to handle the
boiler weight and water content (refer to
Table 1A). Otherwise, a potentially hazardous
situation could result in death, serious injury
and substantial property damage.
WARNING
Do not drop boiler when
removing from skid and moving to permanent
position.
CAUTION
Summary of Contents for MegaSteam MST288
Page 54: ...54 103536 08 4 18 Bare Boiler Assembly Section XII Repair Parts continued...
Page 56: ...56 103536 08 4 18 Bare Boiler Assembly Section XII Repair Parts continued...
Page 58: ...58 103536 08 4 18 Jacket Assembly Section XII Repair Parts continued...
Page 62: ...62 103536 08 4 18 Beckett AFG Burner Section XII Repair Parts continued...
Page 65: ...65 103536 08 4 18...
Page 66: ...66 103536 08 4 18...
Page 67: ...67 103536 08 4 18...