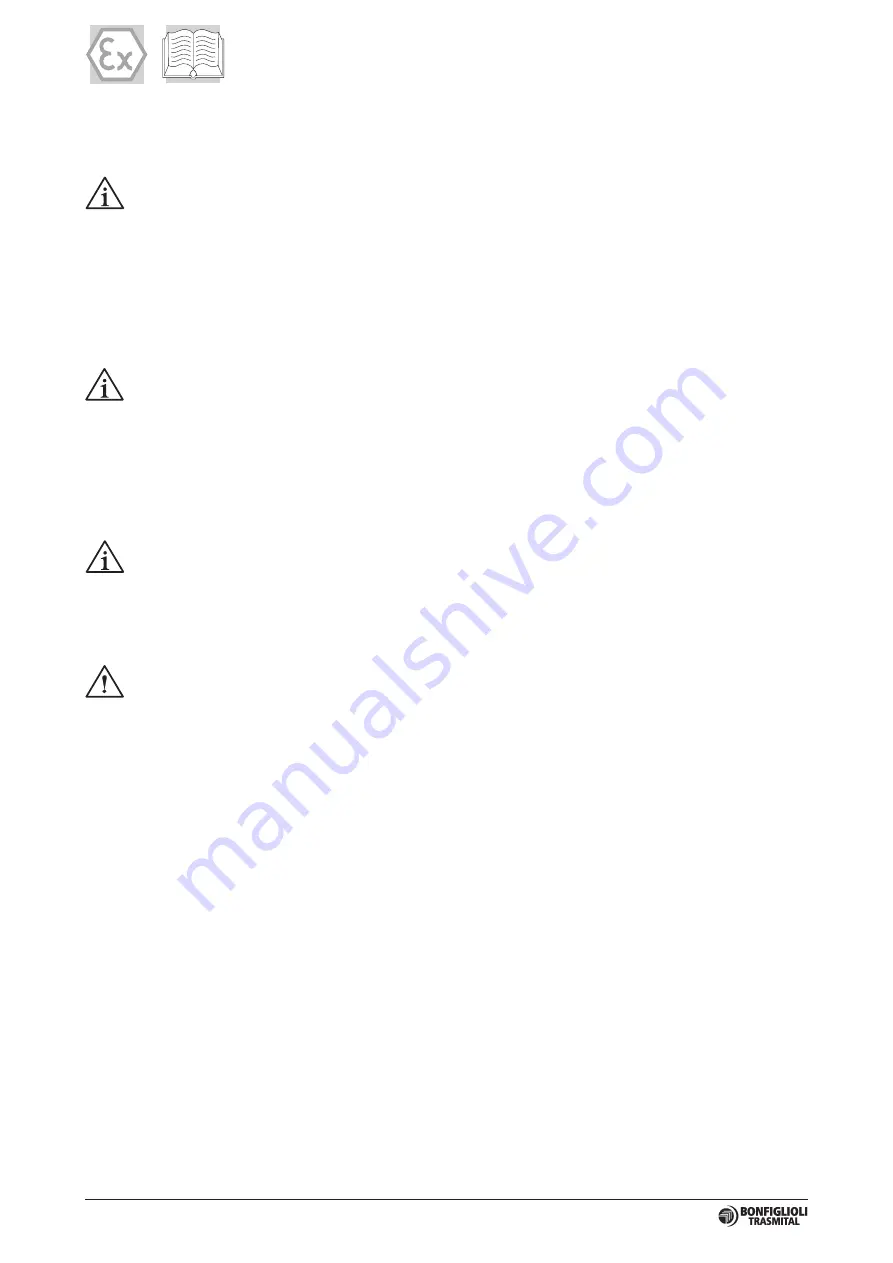
32
8.2 - OIL CHANGES
1. Place an adequate container under the drain plug.
2. Remove the filler and drain plugs and allow the oil to drain out.
The oil will drain better if it is warm
.
3. Wait for a few minutes until all the oil has drained out, then screw the drain plug back on after first chan-
ging the plug seal.
4. Fill with new oil until it reaches the level mark.
Do not mix oils of different makes or specifications
and check that the oil is highly resistant to foaming and is EP rated
.
5. Tighten down the filler plug after changing its seal.
The gear unit may be supplied with or without lubricant, as requested by the User. The quan-
tity of charge oil required is specified in the Sales Catalogue. This specification is however,
approximate, and reference must always be made to the mark on the level plug, the placement
of which depends on the mounting position specified in the purchase order.
Life lubricated gear units which are not subject to external contamination do not normally require pe-
riodic lubricant changes.
If the same type of oil as that already in use is not available, drain the gear unit
casing completely and wash its interior thoroughly with a light solvent before refilling with the new lubricant.
If a leak is found, identify the cause of the fault and repair it before topping up the lubricant
and operating the unit.
Lubricants, solvents and detergents are toxic/harmful to health:
- they may cause irritation in direct contact with the skin
- they may cause intoxication if inhaled
- they may be fatal if swallowed.
Handle them with care using suitable individual safety equipment. Do not dump them into the environment
and dispose of in accordance with applicable legislation.
8.3 - CHECKING OPERATIONAL EFFICIENCY
•
Remove any dust from the gear unit and motor casings.
•
Check that the noise generated at continuous load does not vary. Excessive vibration or noise can indicate
wear of the gear train or failure of a bearing.
•
Check the power absorption and voltage against the rated values given on the motor’s nameplate.
•
Check the wear of the friction surfaces and braking gasket on the brake motors (if fitted) and, if necessary,
adjust the gap.
•
Check for lubricant leaks from the gaskets/seals, plugs and casings.
•
Check all bolted couplings for wear, deformation and corrosion and tighten them down fully, but without
over tightening.
8.4 - CLEANING
Remove all dust and process waste from the gear unit. Do not use solvents or other products that are incom-
patible with the unit’s construction material and do not direct high pressure jets of water at the gear unit.
Summary of Contents for DP20-4H
Page 11: ......
Page 12: ......
Page 26: ......
Page 27: ......
Page 28: ......
Page 29: ......
Page 30: ......
Page 31: ......
Page 32: ......
Page 33: ......
Page 34: ......
Page 35: ...Service Manual Variable Displacement Pumps MP1 powersolutions danfoss com ...
Page 93: ...Service Manual MP1 Danfoss July 2017 AX00000244en US0103 59 ...
Page 94: ...Service Manual MP1 60 Danfoss July 2017 AX00000244en US0103 ...
Page 95: ...Service Manual MP1 Danfoss July 2017 AX00000244en US0103 61 ...
Page 110: ......
Page 111: ......
Page 112: ......
Page 113: ......
Page 115: ......
Page 154: ......
Page 156: ...www dexteraxle com OPERATION MAINTENANCE SERVICE MANUAL 600 8 000 lb Axles Related Components ...
Page 238: ...Service Record Date Service Performed Mileage ...
Page 239: ...Service Record Date Service Performed Mileage ...
Page 240: ...Service Record Date Service Performed Mileage ...