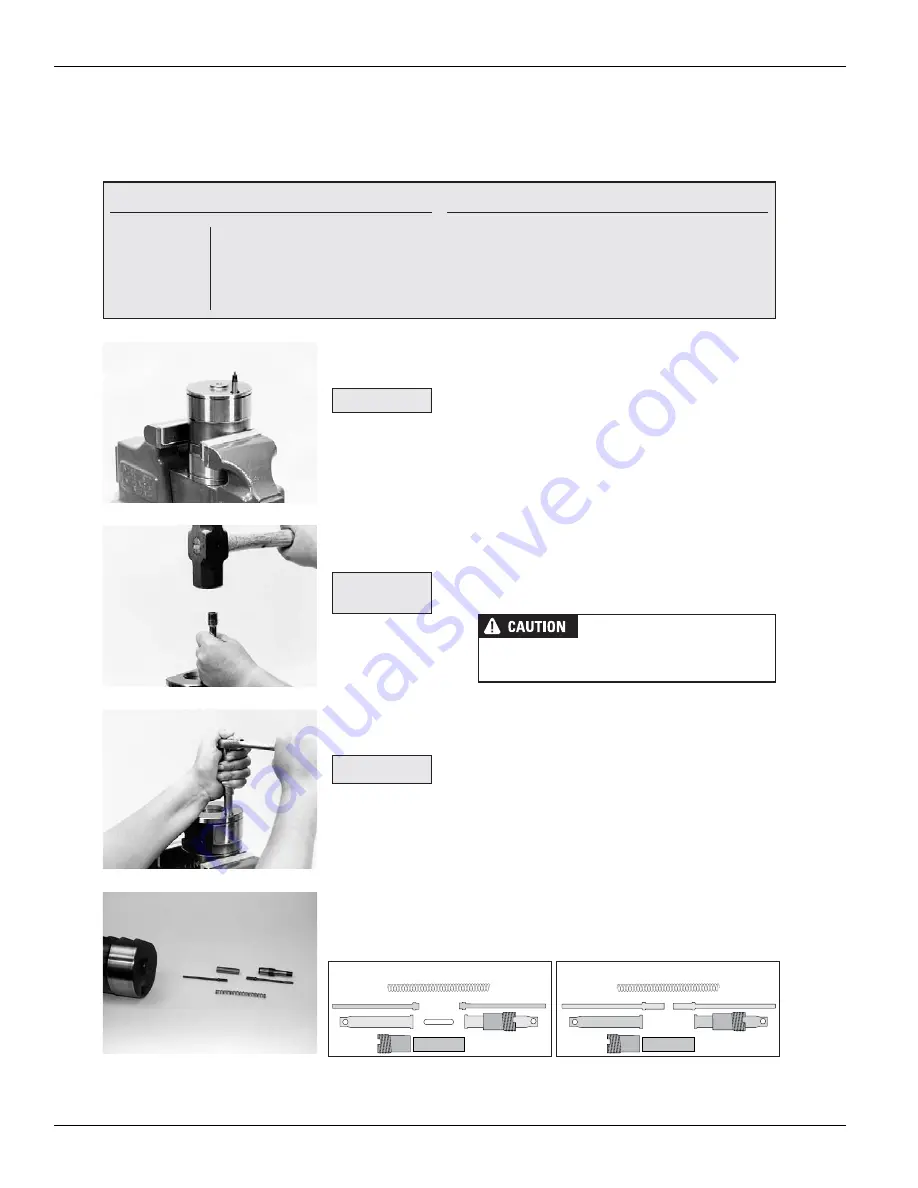
Page 1-42
TRW TAS STEERING GEAR
DocID
STEERING
GROUP 0603-V-003-0207
File Last Modified: September 17, 2012 10:18 am
41
Poppets
Tools Required
2 lb Sledge
Ft
•
lb Torque
wrench
J36452-A
Press
3
⁄
8
"
x 6" drill rod
Materials Required
Locquic "T" primer
Loctite RC680
Ratchet
Soft-jawed vise
Place rack piston
in vise
Loosen poppet
adjuster seat
1.
If the poppet assemblies are to be removed for replacement,
place rack piston (35) in a soft-jawed vise.
2.
Slide special tool #J36452-A over the seat of poppet adjuster
seat and sleeve assembly (23) and engage tool in the slots in the
threaded sleeve. Hit the end of the tool firmly four or five times
with a 2 lb sledge hammer to loosen Loctite.
Poppet adjuster seat and sleeve
assemblies (23) are retained
by Loctite applied to the threads which makes the
assemblies difficult to remove.
Soft-jawed vise
J36452-A
2 lb Sledge
3.
With a ratchet applied to the tool, turn one adjuster seat and
sleeve assembly out of the rack piston. If the ratchet does
not turn easily, strike the adjuster removal tool again with
a hammer. If the engaging tangs won't stay in place while
torquing, it might be necessary to hold in place with an arbor
press while applying loosening torque. Discard poppet seat and
sleeve assembly.
4.
Remove the two poppets (24), spring (26), and push tube (25).
Some older gears may also have a spacer rod (See Illustration)
to be removed.
Remove poppet
components
Remove poppet
adjuster seat
J36452-A
Push Tube
Poppet
Poppet
Poppet Seat
Poppet Seat and
Sleeve Assembly
Poppet
Sleeve
Spring
Push Tube
Poppet
Poppet
Poppet Seat
Spacer Rod
Poppet Seat and
Sleeve Assembly
Poppet
Sleeve
Spring
Old Design
New Design
Summary of Contents for TA S40 Series
Page 5: ...GROUP 0603 V 003 0207 STEERING 7 DocID TRW TAS STEERING GEAR Page 1 5 Review Draft 4 ...
Page 7: ...GROUP 0603 V 003 0207 STEERING 7 DocID TRW TAS STEERING GEAR Page 1 7 Review Draft 6 ...
Page 23: ...GROUP 0603 V 003 0207 STEERING 7 DocID TRW TAS STEERING GEAR Page 1 23 Review Draft 22 ...
Page 57: ...GROUP 0603 V 003 0207 STEERING 7 DocID TRW TAS STEERING GEAR Page 1 57 Review Draft ...