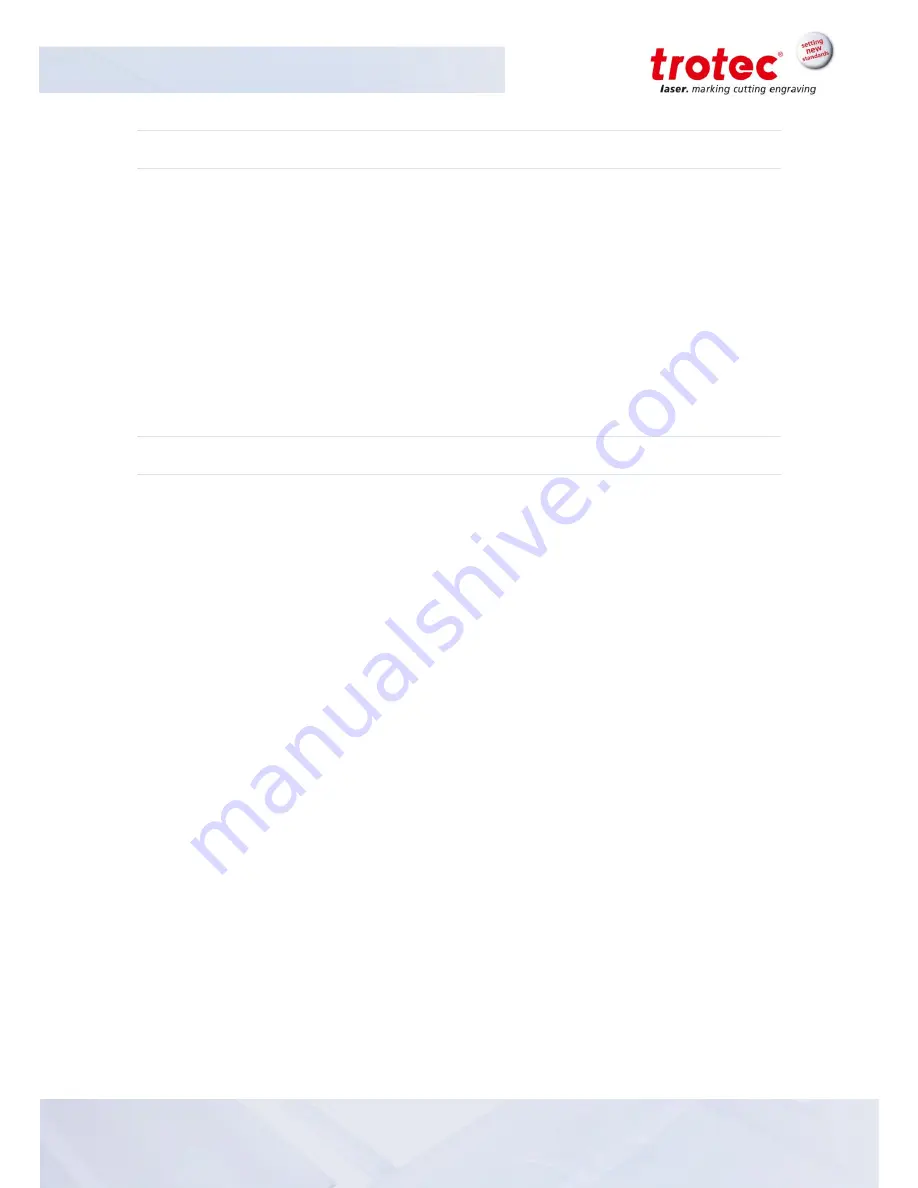
Speedy 360
BA 8032_2.2_EN (05/2016)
73 / 90
www.troteclaser.com
8.9.2
Tips and tricks for laser cutting
Distance to the surface of the workpiece
To achieve very good results when laser-cutting acrylic or wood, we recommend that the plate be
attached at least some millimeters above the engraving table. By doing this, the smoke and the molten
residues underneath the plate can escape unhindered. Slight moistening of the plate will reduce the
area of heat influence. Generally the protection foil should be removed, except when there is
considerable development of fumes. During laser cutting the Hz setting (pulses per second) should be
set to a low value, in particular for flammable materials.
Activate the air assist for cutting in order to protect the lens from being soiled by material parts being
blasted off.
Multiple cutting
Often a clearer contour can be achieved by cutting twice rather than cutting only once.
8.9.3
Tips and tricks for the production of rubber dies
The various mixtures and densities of rubber plates cause a slightly varying engraving depth. The
settings in the overview table give a good indication. Since engraving a standard rubber material
requires relatively high laser power, the laser power is principally set to 100%, and only the speed is
varied.
Due to their lower density, so-called micro-porous rubber materials allow significantly higher engraving
speeds. Test the rubber first, to find out the correct speed setting.
The JobControl
®
software simplifies the creation of a stamp significantly. Mirroring as well as
converting is performed automatically, and a cone-shaped shoulder is generated around each letter.
Due to the wider base, the letters are stabilized during stamping, and therefore the imprint becomes
clearer. If you engrave rubber dies without using this option, the letters will have no shoulders, making
them very thin and unstable.
To avoid flaming, we recommend a low Hz setting near 1000 Hz for cutting the rubber die. The laser
pulses are thus set apart from each other so far that their edges just touch. This results in a
perforation. The rubber die stays connected to the rubber plate, but can be torn off easily. The
advantage of this method is that there is practically no further risk of deformation or melting of the
material. Furthermore, the entire plate can be removed from the laser at one time instead of having to
collect all dies individually.
Engraving rubber produces a considerable amount of dust. Therefore a well-dimensioned exhaust
system and its regular maintenance are very important. An appropriate Trotec exhaust system is
recommended.