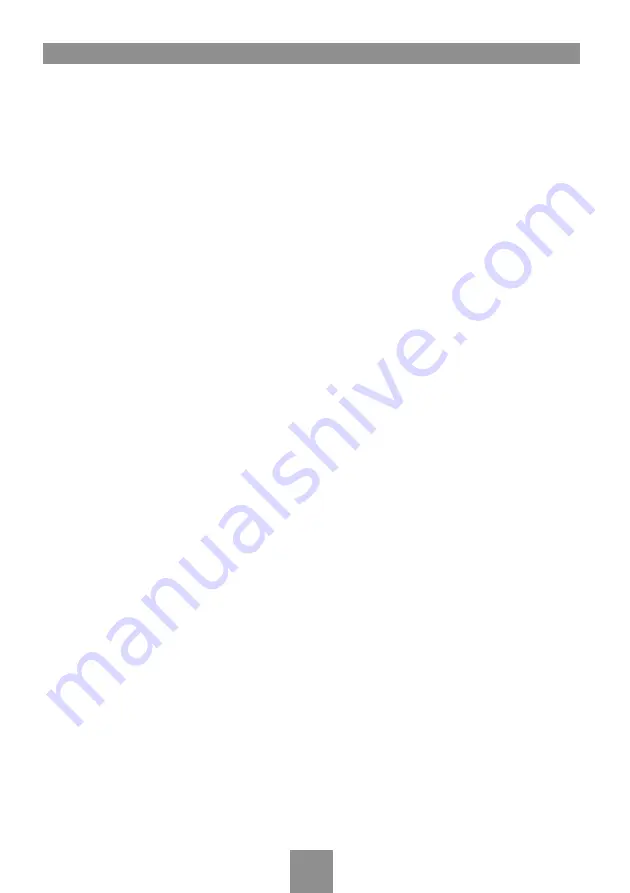
DC7000 ANTIQUE
2
INTRODUCTION
This book contains all the necessary fitting and
operating instructions for your Triton dual control
mixer shower. Please read them carefully. Read
through the whole of this book before beginning
your installation.
The shower installation must be carried out by a
suitably competent person and in sequence of this
instruction book.
Care taken during the installation will ensure a
long and trouble free life from the shower.
This thermostatic shower valve has been
independently tested and approved to all the
requirements of
NHS Estates Model Engineering
Specification D08 Thermostatic Mixing Valves
(Healthcare Premises)
to the following
designations and for the following applications:
HP-S
Shower with supply pressures of
1 - 5 Bar and unrestricted flow rate.
LP -S
Shower with supply pressures of
0.2 - 1 Bar and unrestricted flow rate.
For optimum performance within the specified
running pressure range a minimum flow of 8 litres
per minute should be available to both inlets.
The valve is suitable for fully modulating
type combination boilers and multi-point hot
water heaters. Also suitable for thermal
storage, unvented systems and pumped
gravity systems.
Important: Before installing with a gas
instantaneous water heater, ensure the
appliance is capable of hot water delivery at
a minimum switch on flowrate of 3 litres per
minute. At flow rates between 3 and 8 litres
per minute the appliance must be capable of
raising the water temperature by 45°C.
Water temperature at the inlet to the mixer
must remain relatively constant when
flowrate adjustments are made.
The valve unit can be fitted in any orientation. For
a wall mounted sprayhead installation, the
plumbing will be simplified if the outlet is fitted
upwards.
The valve is supplied with an integral single check
valve and integral large area filter on each inlet.
Inlet connections are by compression fittings for
15mm copper pipe.
This valve unit is supplied with a mounting bracket
to suit installation in a chased out cavity in a solid
wall, a stud partition wall, dry lined wall or fixing
to a shower cubicle or panel. It is also supplied
with an attached tiling shroud which provides
protection for the unit.
SAFETY WARNINGS
1
Layout and sizing of pipework must be such
that when other services are used, pressures
at the shower control inlets
do not
fall below
the recommended minimum.
2
DO NOT choose a position where the shower
could become frozen.
3
The outlet of this appliance must not be
connected to any form of tap or fitting not
recommended by the manufacturer.
4
The sprayhead must be cleaned regularly to
remove scale and debris.
5
Conveniently situated isolating valves in each
inlet supply must be fitted as an independent
method of isolating the shower should
maintenance or servicing be necessary.
6
If it is intended to operate the shower in areas
of hard water it is advisable to fit a scale
inhibitor.
7
If it is intended to operate the shower outside
the guidelines laid out in the requirements
then see NOTE below.
NOTE: In the event of items 2 and 7, contact
Triton Customer Service for advice.
Tel: (024) 7637 2222.
Replacement parts can be ordered from Triton
Customer Service. See
‘spare parts’
for details and
part numbers.
Due to continuous improvement and updating,
specification may be altered without prior notice.
Summary of Contents for DC7000 Antique
Page 2: ...DC7000 ANTIQUE UKAS QUALITY MANAGEMENT 003...
Page 25: ...23 DC7000 ANTIQUE...
Page 26: ...DC7000 ANTIQUE 24...
Page 27: ......