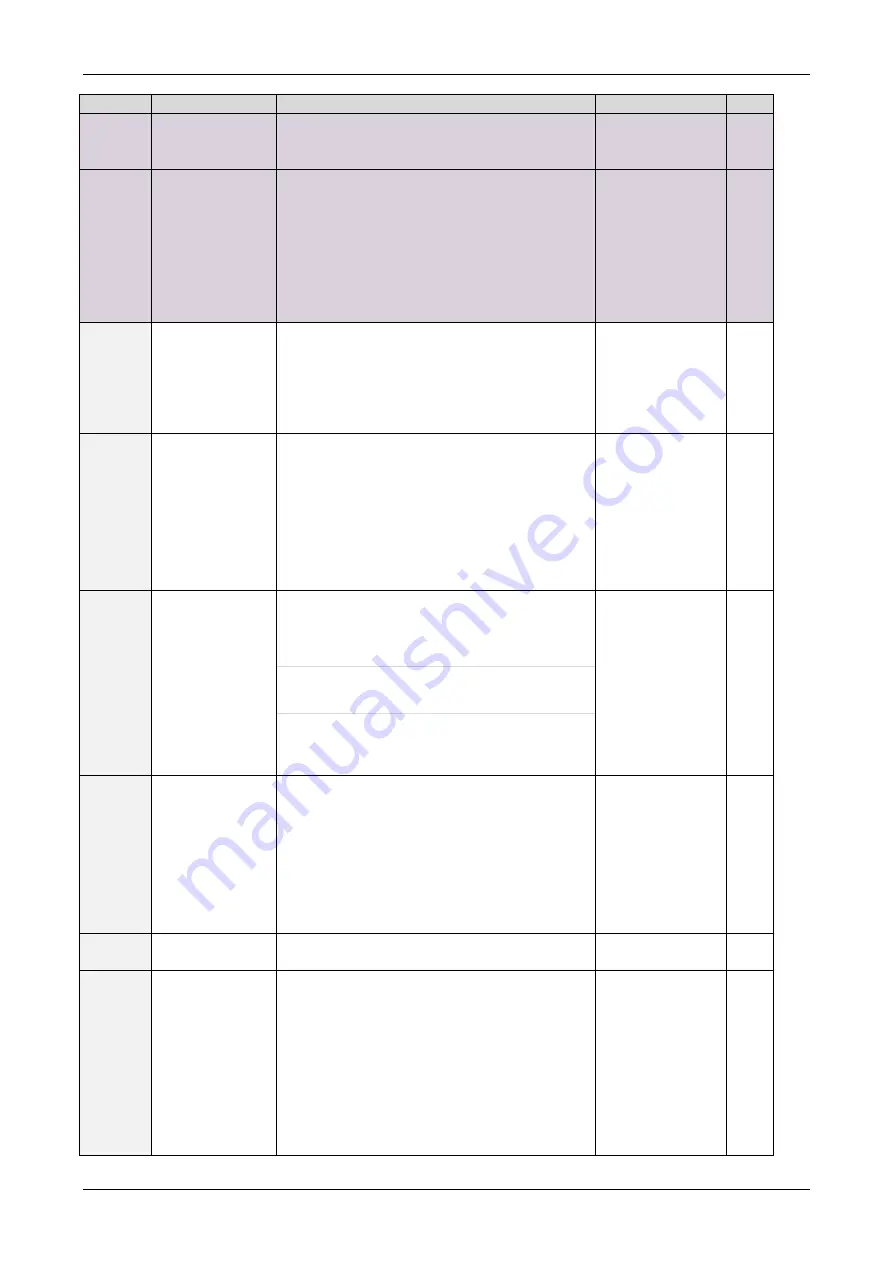
PD57/60-1060 / TMCM-1060 TMCL™ Firmware Manual (V1.04 / 2011-AUG-29)
96
Copyright © 2011, TRINAMIC Motion Control GmbH & Co. KG
Number Axis Parameter Description
Range [Unit]
Acc.
166
chopper
hysteresis start
Hysteresis start setting. Please remark, that
this value is an offset to the hysteresis end
value.
0… 8
RW
167
chopper off time The off time setting controls the minimum
chopper frequency. An off time within the
range of 5µs to 20µs will fit.
Off time setting for constant t
OFF
chopper:
N
CLK
= 12 + 32*t
OFF
(Minimum is 64 clocks)
Setting this parameter to zero completely
disables all driver transistors and the motor
can free-wheel.
0 / 2… 15
RW
168
smartEnergy
current minimum
(SEIMIN)
Sets the lower motor current limit for
coolStep™ operation by scaling the CS
(Current Scale, see axis parameter 6) value.
minimum motor current:
0 – 1/2 of CS
1 – 1/4 of CS
0/1
RW
169
smartEnergy
current down
step
Sets the number of stallGuard2™ readings
above the upper threshold necessary for each
current decrement of the motor current.
Number of stallGuard2™ measurements per
decrement:
Scaling: 0… 3: 32, 8, 2, 1
0: slow decrement
3: fast decrement
0… 3
RW
170
smartEnergy
hysteresis
Sets the distance between the lower and the
upper threshold for stallGuard2™ reading.
Above the upper threshold the motor current
becomes decreased.
0… 15
RW
Hysteresis:
(smartEnergy hysteresis value + 1) * 32
Upper stallGuard threshold:
(smartEnergy hysteresis start + smartEnergy
hyst 1) * 32
171
smartEnergy
current up step
Sets the current increment step. The current
becomes incremented for each measured
stallGuard2™ value below the lower threshold
(see smartEnergy hysteresis start).
current increment step size:
Scaling: 0… 3: 1, 2, 4, 8
0: slow increment
3: fast increment / fast reaction to rising load
1… 3
RW
172
smartEnergy
hysteresis start
The lower threshold for the stallGuard2™
value (see smart Energy current up step).
0… 15
RW
173
stallGuard2™
filter enable
Enables the stallGuard2™ filter for more
precision of the measurement. If set, reduces
the
measurement
frequency
to
one
measurement per four fullsteps.
In most cases it is expedient to set the
filtered mode before using coolStep™.
Use the standard mode for step loss
detection.
0 – standard mode
1 – filtered mode
0/1
RW