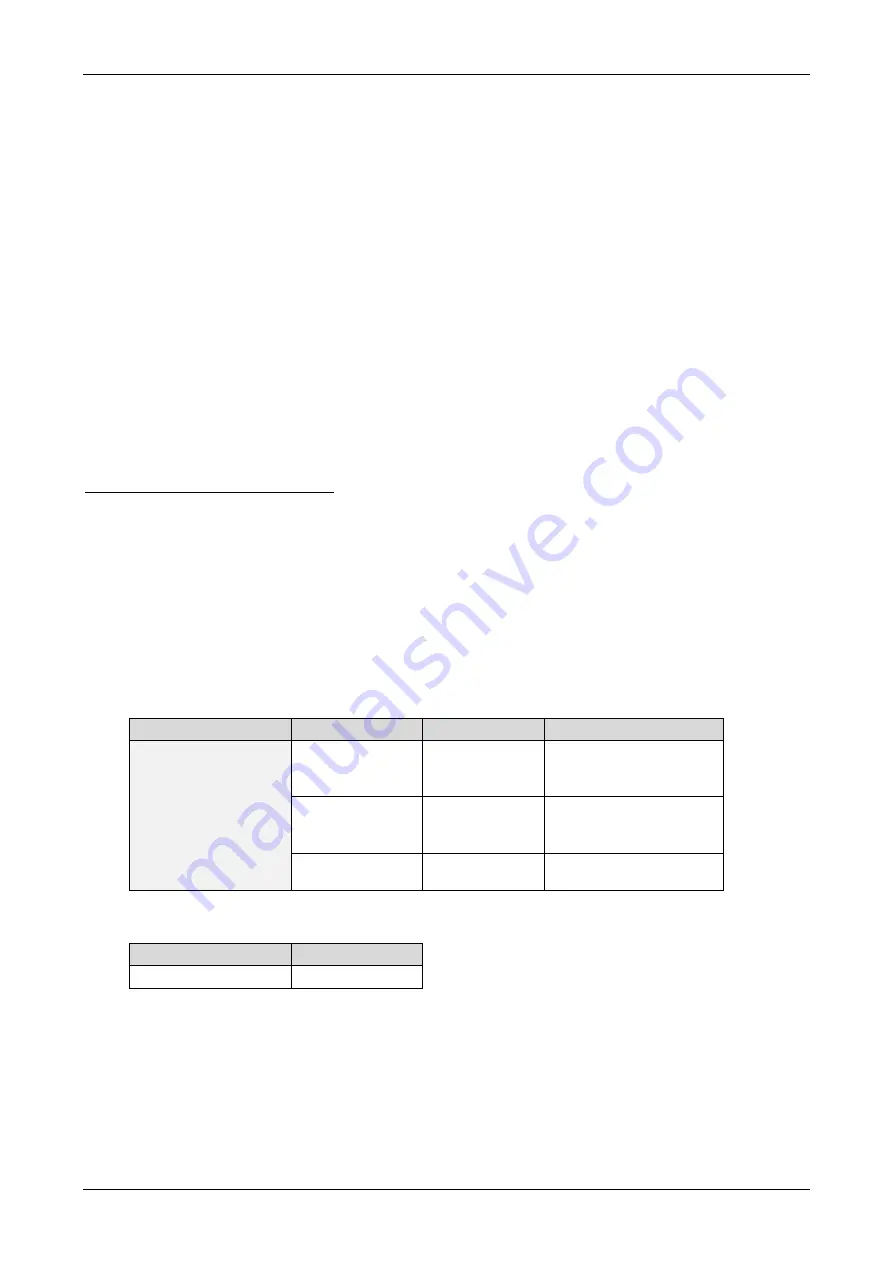
PD57/60-1060 / TMCM-1060 TMCL™ Firmware Manual (V1.04 / 2011-AUG-29)
25
Copyright © 2011, TRINAMIC Motion Control GmbH & Co. KG
5.7.4
MVP (move to position)
With this command the motor will be instructed to move to a specified relative or absolute position or a
pre-programmed coordinate. It will use the acceleration/deceleration ramp and the positioning speed
programmed into the unit. This command is non-blocking – that is, a reply will be sent immediately after
command interpretation and initialization of the motion controller. Further commands may follow without
waiting for the motor reaching its end position. The maximum velocity and acceleration are defined by axis
parameters #4 and #5.
The range of the MVP command is 32 bit signed (−2.147.483.648… +2.147.483.647). Positioning can be
interrupted using MST, ROL or ROR commands.
Attention:
Please note, that trajectory parameters (like maximum positioning speed and acceleration) cannot
be changed while positioning is in progress.
Only the target position can be changed while positioning is in progress (with some restrictions).
Please note, that the distance between the actual position and the new one should not be more
than 2.147.483.647 microsteps. Otherwise the motor will run in the wrong direction for taking a
shorter way. If the value is exactly 2.147.483.648 the motor maybe stops.
Three operation types are available:
Moving to an absolute position in the range from −2.147.483.648… +2.147.483.647.
Starting a relative movement by means of an offset to the actual position. In this case, the new
resulting position value must not exceed the above mentioned limits, too.
Moving the motor to a (previously stored) coordinate (refer to SCO for details).
Internal function:
A new position value is transferred to the axis parameter #2
target position
.
Related commands:
SAP, GAP, SCO, CCO, GCO, MST
Mnemonic:
MVP <ABS|REL|COORD>, 0, <position|offset|coordinate number>
Binary representation:
INSTRUCTION NO.
TYPE
MOT/BANK
VALUE
4
0 ABS – absolute
0
*
<position>
−2.147.483.648…
+2.147.483.647
1 REL – relative
0
<offset>
−2.147.483.648…
+2.147.483.647
2 COORD –
coordinate
0
<coordinate number>
0… 20
*motor number is always O as only one motor is involved
Reply in direct mode:
STATUS
VALUE
100 – OK
don’t care