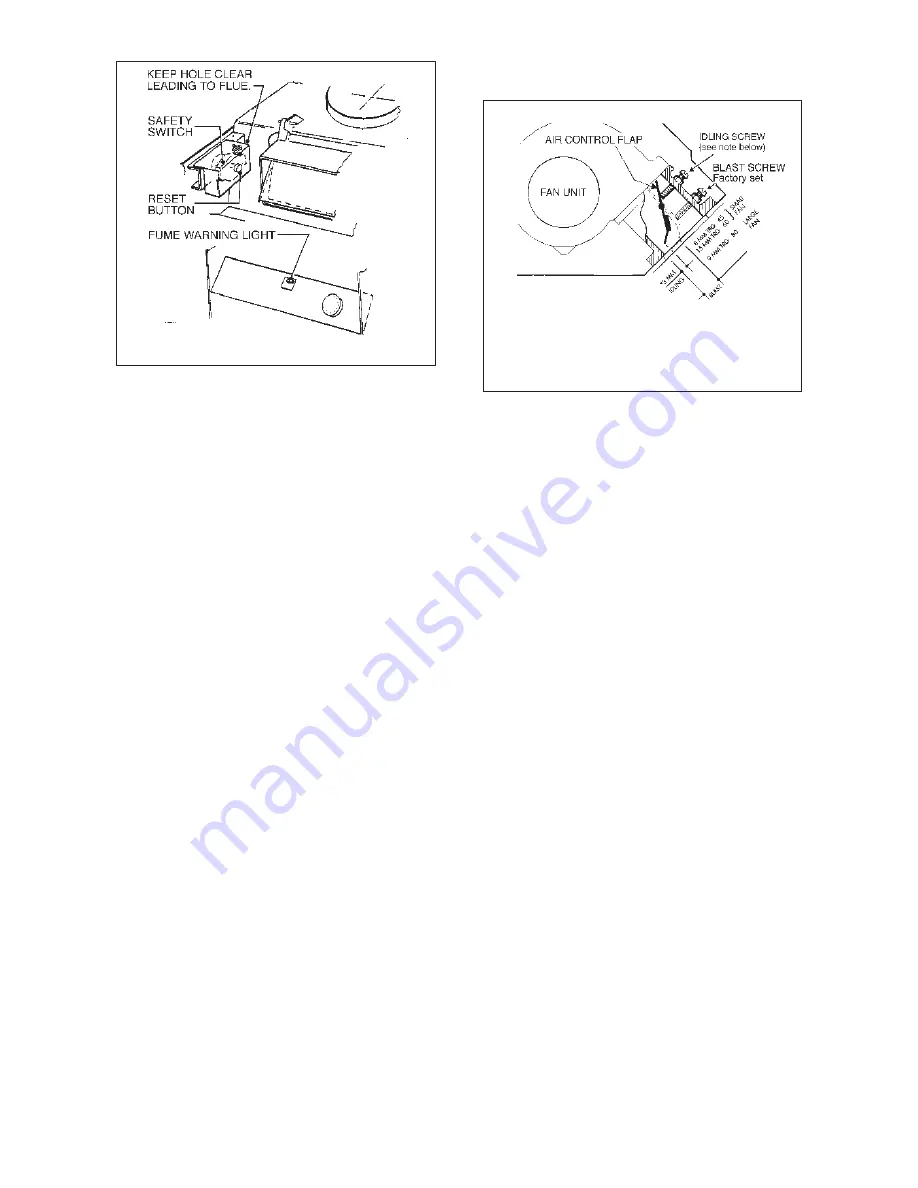
In addition to the primary air, pre-heated secondary air is
also supplied over the firebed to ensure complete combustion.
W A R N I N G N O T E S
Fumes:
When properly installed and operated, this appliance will
not emit fumes into the dwelling. Occasional fumes from
ash removal and refuelling may occur but persistent fume
emission is potentially dangerous and must not be tolerated.
If, despite the operation of the Safety Switch, fumes are
emitted from the boiler then the following immediate
action should be taken:
a. Switch off the electrical supply to the boiler.
b. Open doors and windows to ventilate the room.
c. Let the fire out or safely dispose of fuel from the
appliance.
d. Check the boiler flueways and chimney for blockage
and clean as required.
e. Do not attempt to re-light the fire until the cause of
the fume emission has been identified and corrected.
If necessary, seek expert advice.
Frozen System
Do not attempt to light the fire if it is suspected that any
part of the water system is frozen.
Ventilation
An extractor fan must not be fitted in the same room as
the appliance.
Operating Problems
If in difficulty with the operation of the boiler, refer to the
Fault Finding Chart which indicates most of the common
operating faults and suggests remedies to overcome
them. If this chart does not provide the answer, contact
your local Heating Engineer for assistance.
Maintaining the Boiler
Routine cleaning maintenance of this boiler is a simple
procedure and can be carried out by the user, but it is
recommended that a complete service be undertaken
annually by a qualified Service Engineer.
Fig. 2 AIR CONTROL SETTINGS
Fig. 1
BLOCKED FLUE SAFETY SWITCH
To Light Boiler
1. Check that the boiler is full of water and all valves are open.
2. Switch on electrical supply to boiler
3. Ensure that the fuel- regulator is correctly positioned
to suit the fuel being used and fill hopper (see under
Fuel Regulator Settings)
4. Thoroughly warm the chimney by lighting two or three
wax firelighters in the boiler flue outlet.
5. After warming the chimney insert three wax fire
lighters in the middle and well up into the firebed.
Light and allow them to burn under natural draught for
3 or 4 minutes. (See Fig. 3 for position of fire lighters)
6. Close the fire-door., switch on the fan by turning up
the thermostat.
7. The fire should be well established within approximately
15 minutes, but check to make sure that the fire
lighters have not been extinguished.
8. The fan will continue to blow until the thermostat setting
is reached. Thereafter it will operate automatically,
switching on and off to satisfy the heat demand.
Thermostat Settings
Setting Low
I
I
I
I
High
Approx Temp. °C 55
60
66
71
76
82
The setting selected will depend on the nature of the
load, i.e. whether heating or hot water, the season of the
year and individual requirements.
Typical settings are:
Domestic Hot Water
55° to 60°C
Early and latter parts
66° to 71°C
of heating system
Mid winter conditions
76° to 82°C
Air Control
On a demand for heat, air is supplied to the fire by a
thermostatically controlled forced draught fan, whereas
during the “fan off” period the fire idles at a low rate of
burning under natural draught.
The air supply for both rates of combustion is controlled by a
balanced flap in the fan throat which is factory set for “blast”
and has adjustment for “idling” if required.(See Fig. 2.)
2
THE IDLING CONTROL SCREW MAY NEED ADJUSTING
TO SUIT INDIVIDUAL DRAUGHT CONDITIONS. IF FIRE
GOES OUT SCREW IN APPROX. 2 TURNS TO PROP
OPEN FLAP WIDER. IF BOILER OVERHEATS SCREW
OUT APPROX. 2 TURNS TO CLOSE FLAP