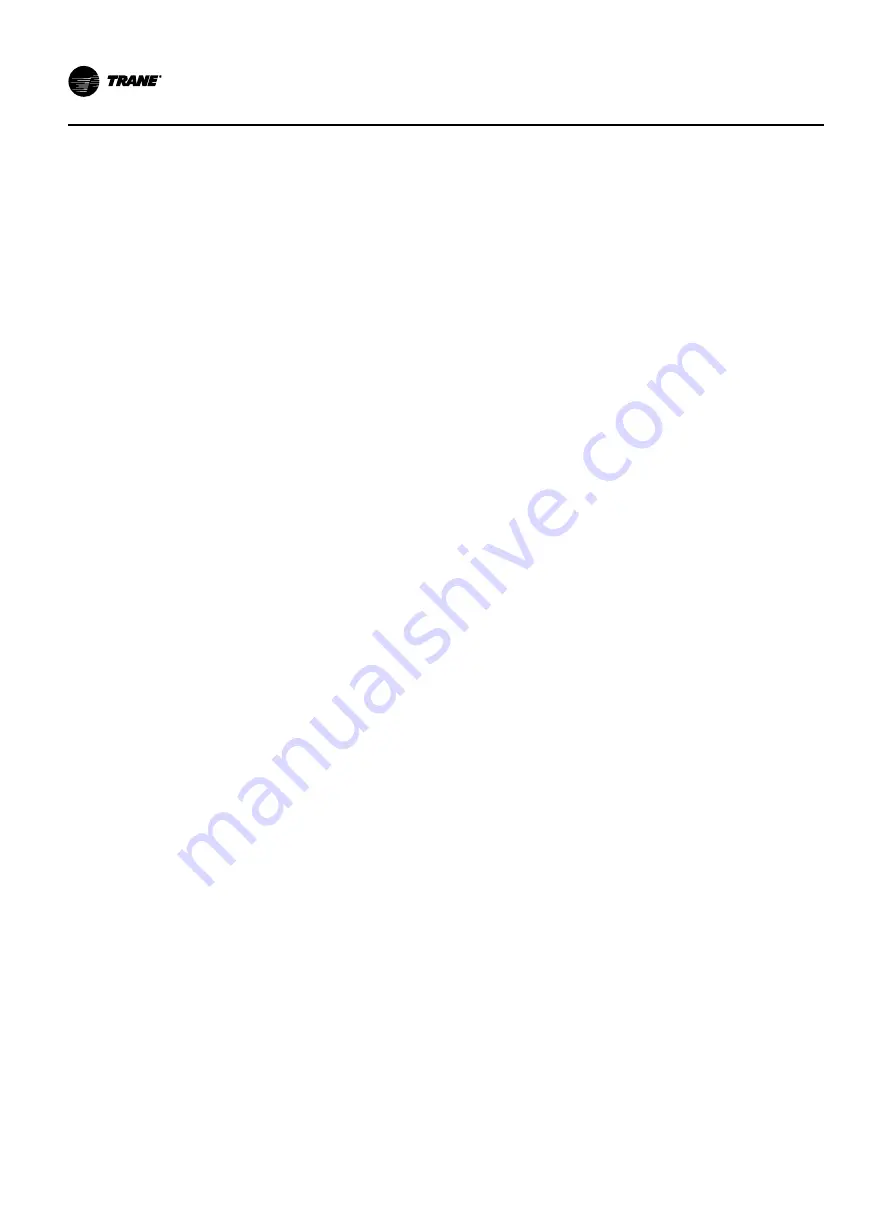
close for unit shutdown. After a chiller starts and is run-
ning the inlet guide vanes will pass through the HGBP
Cut-In-Vane position as the chiller starts to load. As the
chiller catches the load and starts to unload, the inlet
guide vanes will close to the HGBP Cut-In Vane position.
At this point the movement of the inlet guide vanes is
stopped and further loading/unloading of the chiller is
controlled by the opening/closing of the HGBP Valve
(4M5). When the control algorithm determines the chiller
to be shut down, the inlet guide vanes will be driven
fully closed, and the HGBP valve will be driven closed.
After the inlet guide vanes are fully closed the chiller
will shut down in the Friendly mode. Chillers with HGBP
have a discharge temperature sensor (4R16) monitoring
the discharge gas temperature from the compressor. If
this temperature exceeds 200°F, the chiller will shut off
on a MAR diagnostic. The chiller will reset automatically
when this temperature drops 50°F below the trip-point.
HGBP is enabled in the Features menu settings Group of
the Tracer AdaptiView Menus by enabling the option. The
setting the HGBP Cut-In Vane Position is setup at unit
commissioning via the service tool.
Hot Water Control
Occasionally CTV chillers are selected to provide heat-
ing as a primary mission. With hot water temperature
control, the chiller can be used as a heating source or
cooling source. This feature provides greater application
flexibility. In this case the operator selects a hot water
temperature and the chiller capacity is modulated to
maintain the hot water setpoint. Heating is the primary
mission and cooling is a waste product or is a second-
ary mission. This type of operation requires an endless
source of evaporator load (heat), such as well or lake wa-
ter. The chiller has only one condenser.
This is NOT heat recovery. Although this feature could be
used to recover heat in some form, a heat recovery unit
has a second heat exchanger on the condenser side.
The Tracer AdaptiView Main Processor provides the hot
water temperature control mode as standard. The leaving
condenser water temperature is controlled to a hot water
setpoint between 80°F and 140°F (26.7 to 60°C) The leav-
ing evaporator water temperature is left to drift to satisfy
the heating load of the condenser. In this application the
evaporator is normally piped into a lake, well, or other
source of constant temperature water for the purpose of
extracting heat. In hot water temperature control mode
all the limit modes and diagnostics operate as in normal
cooling with one exception; the leaving condenser water
temperature sensor is an MMR diagnostic when in hot
water temperature control mode. (It is an informational
warning in the normal cooling mode.)
In the hot water temperature control mode the differen-
tial-to-start and differential-to-stop setpoints are used
with respect to the hot water setpoint instead of with the
chilled water setpoint. The control panel provides a sep-
arate entry at the Tracer AdaptiView to set the hot water
setpoint. Tracer is also able to set the hot water setpoint.
In the hot water mode the external chilled water setpoint
is the external hot water setpoint; that is, a single analog
input is shared at the 1A16 –J2-1 to J2-3 (ground).
An external binary input to select external hot water
control mode is on the EXOP OPTIONAL module 1A18
terminals J2-3 to J2-4 (ground). Tracer also has a binary
input to select chilled water control or hot water tem-
perature control. There is no additional leaving hot water
temperature cutout; the HPC and condenser limit provide
for high temperature and pressure protection.
In hot water temperature control the softloading pull-
down rate limit operates as a softloading pullup rate
limit. The setpoint for setting the temperature rate limit
is the same setpoint for normal cooling as it is for hot
water temperature control. The hot water temperature
control feature is not designed to run with HGBP, AFD,
free cooling, or ice making.
The factory set PID tuning values for the leaving water
temperature control are the same settings for both nor-
mal cooling and hot water temperature control.
Heat Recovery Cycle
Heat recovery is designed to salvage the heat that is
normally rejected to the atmosphere through the cooling
tower, and put it to beneficial use. For example, a high-
rise office building may require simultaneous heating
and cooling during the winter months. With the addition
of a heat recovery cycle, heat removed from the building
cooling load can be transferred to areas of the building
that require heat. (Keep in mind that the heat recovery
cycle is only possible if a cooling load exists to act as a
heat source.)
To provide a heat recovery cycle, a heat-recovery con-
denser is added to the unit. Though physically identical
to the standard cooling condenser, the heat-recovery
condenser is piped into a heat circuit rather than to
the cooling tower. During the heat recovery cycle, the
unit operates just as it does in the cooling only mode
except that the cooling load heat is rejected to the heat-
ing water circuit rather than to the cooling tower water
circuit. When hot water is required, the heating water
circuit pumps energize. Water circulated through the
heat-recovery (or auxiliary) condenser tube bundle by
the pumps absorbs cooling-load from the compressed
refrigerant gas discharge by the compressor. The heated
water is then used to satisfy heating requirements.
Auxiliary Condensers
Unlike the heat-recovery condenser (which is designed
to satisfy comfort heating requirements), the auxiliary
condenser serves a preheat function only, and is used
in those applications where hot water is needed for use
in kitchens, lavatories, etc. While the operation of the
auxiliary condenser is physically identical to that of the
60
RELEASED 10/Mar/2020 06:59:20 GMT