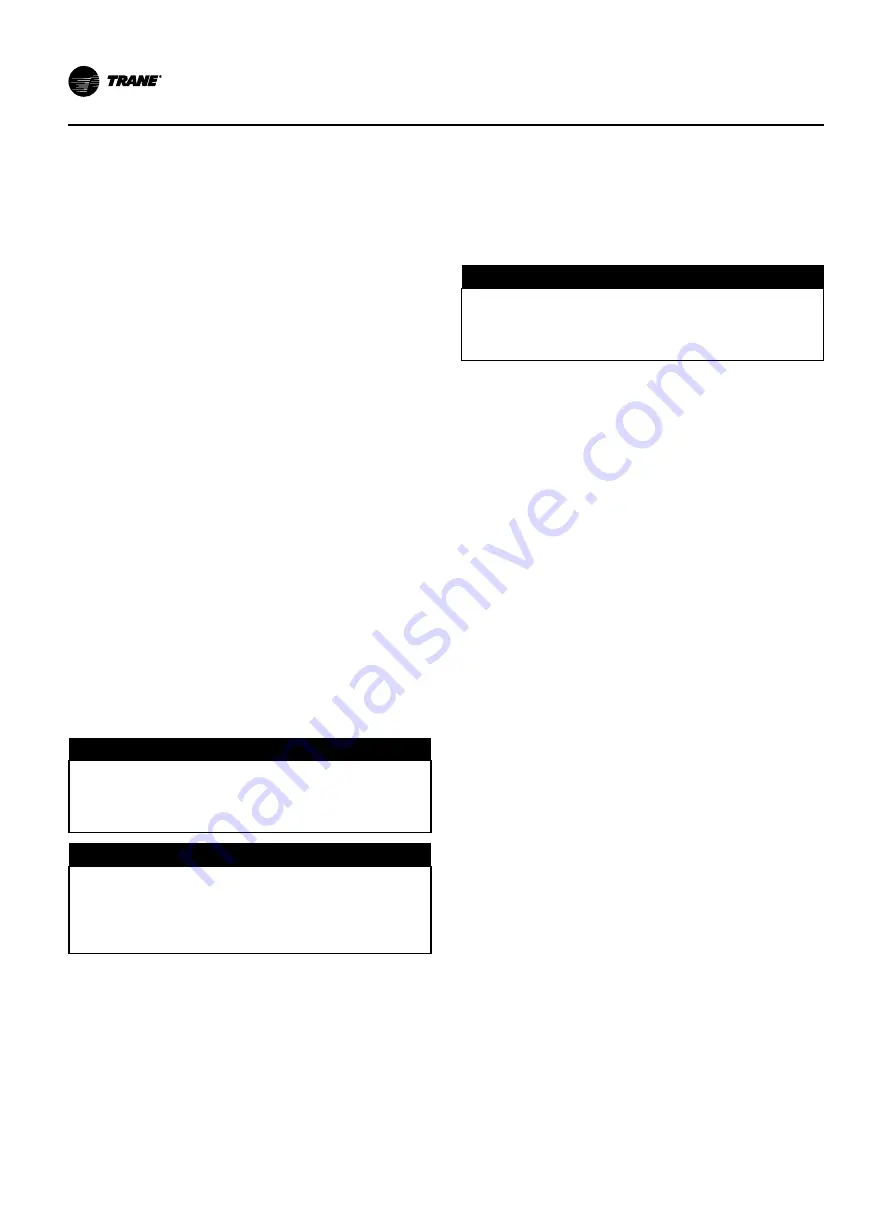
Bus Bars
Bus bars and extra nuts are available as a Trane option.
Install the bus bars between the motor terminals when
using a low-voltage
•
across-the-line
•
primary reactor/ resistor
•
auto transformer
•
customer-supplied outside the delta solid-state
•
customer-supplied AFD.
Connect T1 to T6, T2 to T4, and T3 to T5.
Note:
Bus bars are not needed in medium-voltage or
high-voltage applications since only 3 terminals
are used in the motor and starter.
When attaching starter leads to 6.6 – 7kV motor termi-
nals, the 1/2”– 13 brass jam nuts should be tightened to
a maximum torque of 18 to 22 ft·lb (18 to 30 N·m). Al-
ways use a second wrench to back- up the assembly and
prevent applying excessive torque to the terminal shaft.
Starter to Control Panel Wiring
Field wiring connection diagram and starter to control
panel connection diagram showing the electrical connec-
tions required between the remote-mounted starter and
the control panel are available in the unit submittal.
Note:
Install separate conduit into the low voltage (30
volts) section of the control panel.
When sizing and installing the electrical conductors for
these circuits, follow the guidelines listed. Use 14 ga.
wire for 120V control circuits unless otherwise specified.
D
NOTICE
Component Damage!
Remove all debris from inside the starter panel.
Failure to do so could result in an electrical short and
could cause serious starter component damage.
D
NOTICE
Electrical Noise!
Maintain at least 6 inches between low-voltage (<30V)
and high voltage circuits. Failure to do so could result
in electrical noise that may distort the signals carried
by the low voltage wiring, including the IPC wiring.
1. If the starter enclosure must be cut to provide electri-
cal access, exercise care to prevent debris from fall-
ing inside the enclosure. Do not cut AFD enclosure.
2. Use only shielded twisted pair wiring for the Inter-
processor Communication (IPC) circuit between the
starter and the control panel on remote mounted
starters. Recommended wire is Beldon Type 8760, 18
AWG for runs up to 1000 feet.
Note:
The polarity of the IPC wiring is critical for proper
operation.
3. Separate low-voltage (less than 30V) wiring from the
115V wiring by running each in its own conduit.
4. As you route the IPC circuit out of the starter enclo-
sure, make sure that it is at least 6” from all wires
carrying a higher voltage.
D
WARNING
Grounding Required!
Follow proper local and state electrical code on
requirements for grounding. Failure to follow code
could result in death or serious injury.
5. The IPC wiring shield should be grounded on one
end only at control panel end.The other end should
be un-terminated and taped back on the cable sheath
to prevent any contact between shield and ground.
6. Oil Pump Interlock - All starters must provide an inter-
lock (normally open) contact with the chiller oil pump
connected to the control panel at Terminals 1A7-2-4
and 1A7-J2-2 (14 ga.) The purpose of this interlock is
to power the oil pump on the chiller in the event that
a starter failure, such as welded contacts, keeps the
chiller motor running after the controller interrupts
the run signal.
46
RELEASED 10/Mar/2020 06:59:20 GMT