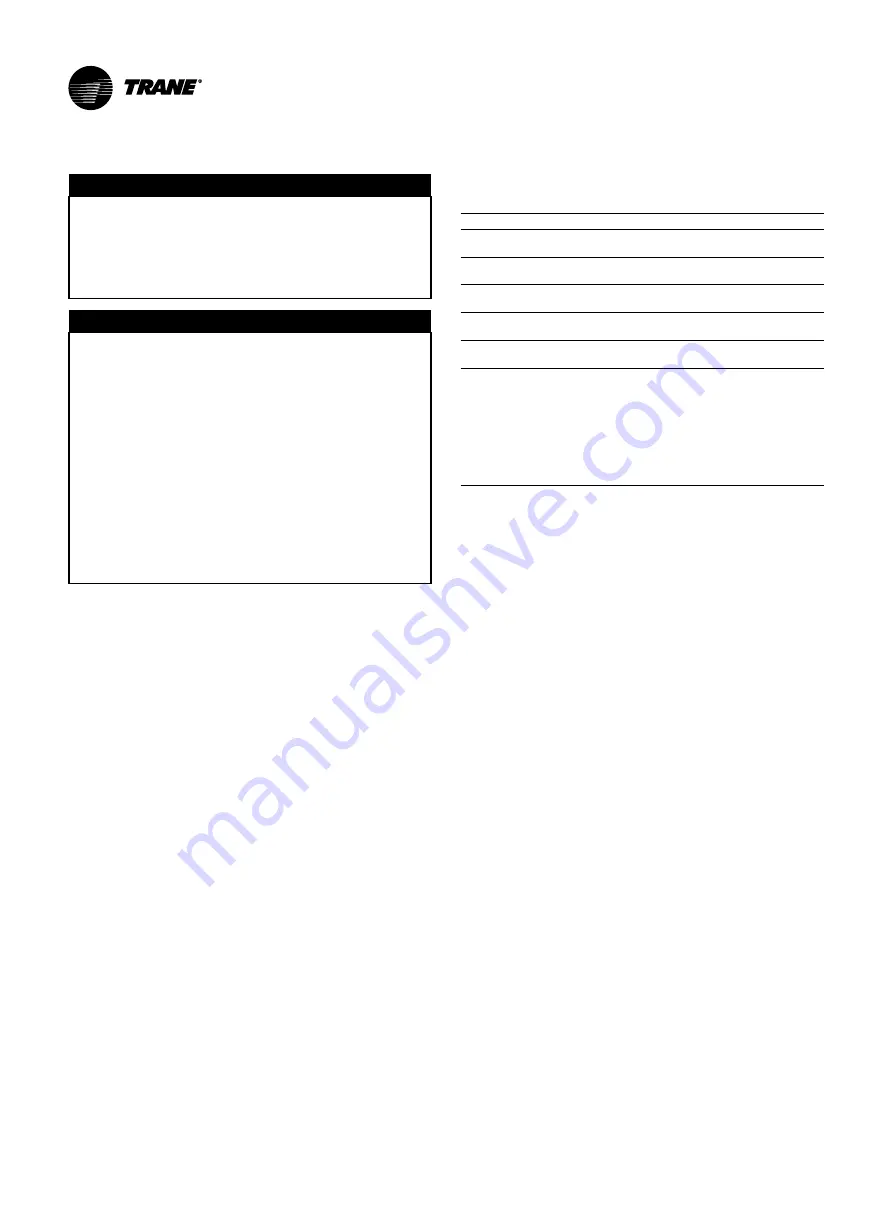
Maintenance
D
NOTICE
Moisture Contamination!
If frequent purging is required, monitor purge pum-
pout rate, identify and correct source of air or water
leak as soon as possible. Failure to do so could short-
en chiller life expectancy, due to moisture contami-
nation caused by leakage.
D
WARNING
Hazardous Voltage w/Capacitors!
Disconnect all electric power, including remote
disconnects before servicing. Follow proper lock-
out/ tagout procedures to ensure the power cannot
be inadvertently energized. For variable frequency
drives or other energy storing components provided
by Trane or others, refer to the appropriate manu-
facturer’s literature for allowable waiting periods for
discharge of capacitors. Verify with an appropriate
voltmeter that all capacitors have discharged. Failure
to disconnect power and discharge capacitors before
servicing could result in death or serious injury.
Note: For additional information regarding the safe
discharge of capacitors, see PROD-SVB06A-EN or
PROD-SVB06A-FR.
This section describes the basic chiller preventive main-
tenance procedures, and recommends the intervals at
which these procedures should be performed. Use of a
periodic maintenance program is important to ensure
the best possible performance and efficiency from a
CenTraVac chiller.
Recommended purge maintenance procedures for the
EarthWise Purge Operation and Maintenance manual
which can be obtained at the nearest Trane office.
For R-123 chillers, recommended purge maintenance
procedures are detailed in
Operation and Maintenance
Guide: EarthWise™ Purge system with Tracer AdaptiV-
iew™ Control for Water-Cooled CenTraVac™ Chillers
with R-123 Refrigerant (PRGF-SVX001*-EN).
For R-514A
chillers, recommended purge maintenance procedures
are detailed in
Operation and Maintenance Guide:
Purge System with Tracer AdaptiView™ Control for
Water-Cooled CenTraVac™ Chillers with R-514A Re-
frigerant (PRGG-SVX001*-EN)
.
Record Keeping Forms
An important aspect of the chiller maintenance program
is the regular completion of records. Provided at the end
of this manual are copies of the recommended forms.
When filled out accurately by the machine operator, the
completed logs can be reviewed to identify any develop-
ing trends in the chiller’s operating conditions. For exam-
ple, if the machine operator notices a gradual increase
in condensing pressure during a month’s time, he can
systematically check, then correct the possible cause of
this condition.
Daily Maintenance and Checks
Operating Characteristic
Normal Reading
Approximate Evaporator Pres-
sure
6 to 9 PSIA / -9 to -6 PSIG
Approximate Condenser Pres-
sure (see Note 1 & Note 2)
17 to 27 PSIA / 2 to 12 PSIG
(standard condenser)
Oil Sump Temperature Unit
not running
140°F to 176°F (60°C to
80°C)
Oil Sump Temperature Unit
running
95°F to 162°F (35°C to 72°C)
Oil Sump Differential Oil Pres-
sure (see Note 3)
18 to 22 psid
Notes:
1. Condenser pressure is dependent on condenser water tem-
perature, and should equal the saturation pressure of HCFC- 123
at a temperature above that of leaving condenser water at full
load.
2. Normal pressure readings for ASME condenser exceed 12
PSIG.
3. Oil tank pressure -9 to -6 psig HG Discharge oil pressure 7 to
15 PSIG
64
RELEASED 10/Mar/2020 06:59:20 GMT