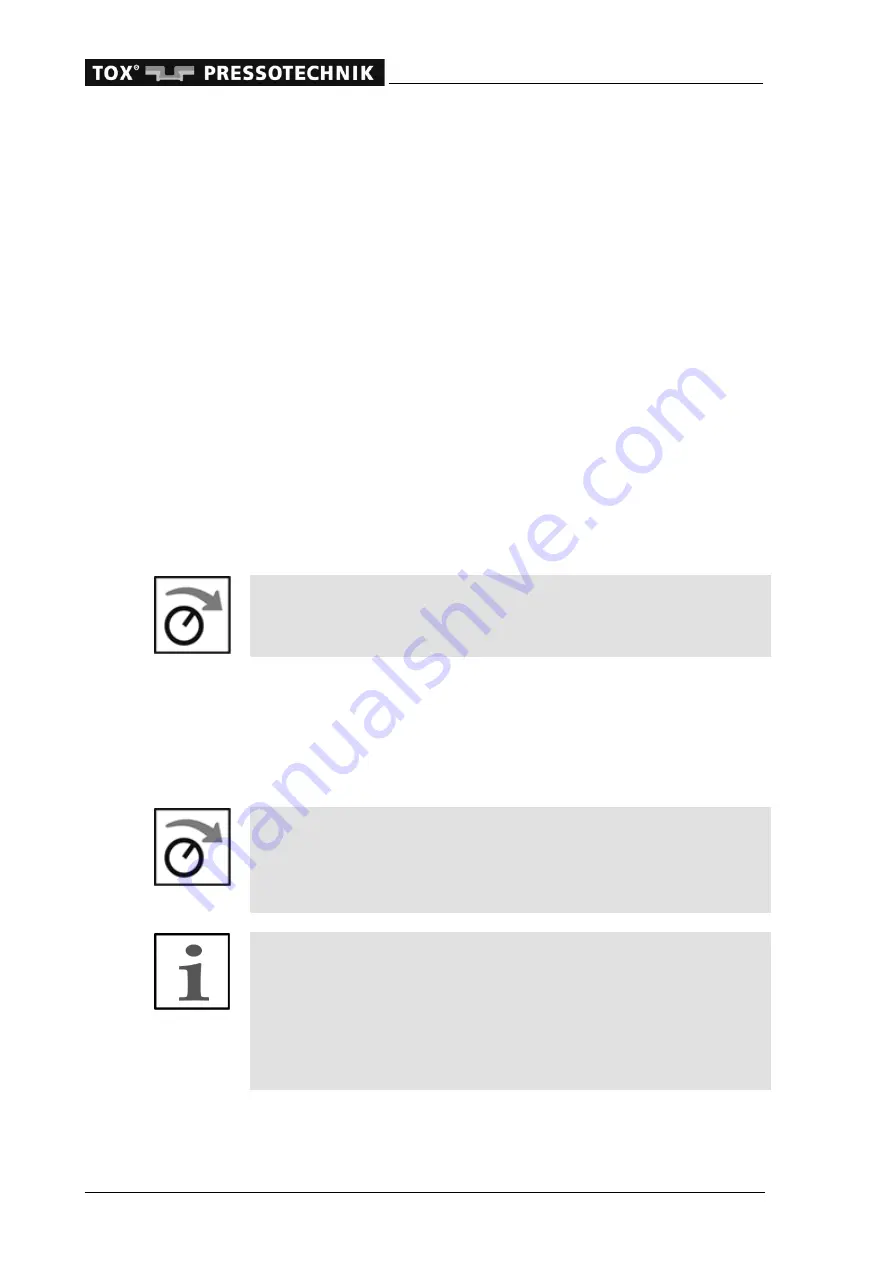
Technical data
20
OM 100.EPW400.202002.en
3.1.10 Sensor: analog standard signals
Measuring is carried out by a sensor with a standardized process signal 0-10 V. The
input is selected in menu 'Configuration'.
Nominal force or nomi-
nal distance:
Adjustable via the menu
A/D converter:
12 bit = 4096 steps (for EPW 400.x02.1x)
16 bit = 65536 steps (for EPW 400.x02.0x)
Nominal load of reso-
lution:
Steps see A/D converter, 1 step (bit) = nominal load /
steps
Accuracy of measure-
ment:
1%
Max. sampling rate:
2000 Hz (0.5 ms)
3.1.11 Sensor: supply voltage
Auxiliary voltage:
24 V ± 5%, max. 100 mA
Reference voltage:
10 V ± 1% nominal signal: 0 – 10 V
Adjustment value
The entries 'Nominal force' or 'Nominal distance' must not be
changed without the agreement of the manufacturer.
3.1.12 Screw sensor with standard signal output
Auxiliary voltage:
24 V ± 5%, max. 100 mA
Nominal signal:
0 – 10 V
Tare signal:
0 V = zero adjustment, > 9 V = measuring mode
Adjustment value
The entry 'Nominal force' must not be changed without the agree-
ment of the manufacturer.
Tightening torque: 14 Nm
Zero adjustment before each work cycle
With some types of force transducers or measurement amplifiers
with tare function, a decrease of the measuring accuracy is possible
after a certain period of time depending on the process. In order to
ensure repeating accuracy, a zero adjustment should be carried out
before each work cycle or at regular time intervals (e.g. for ZKN
model force transducers after approx. 10 minutes).
Summary of Contents for EPW400
Page 3: ......