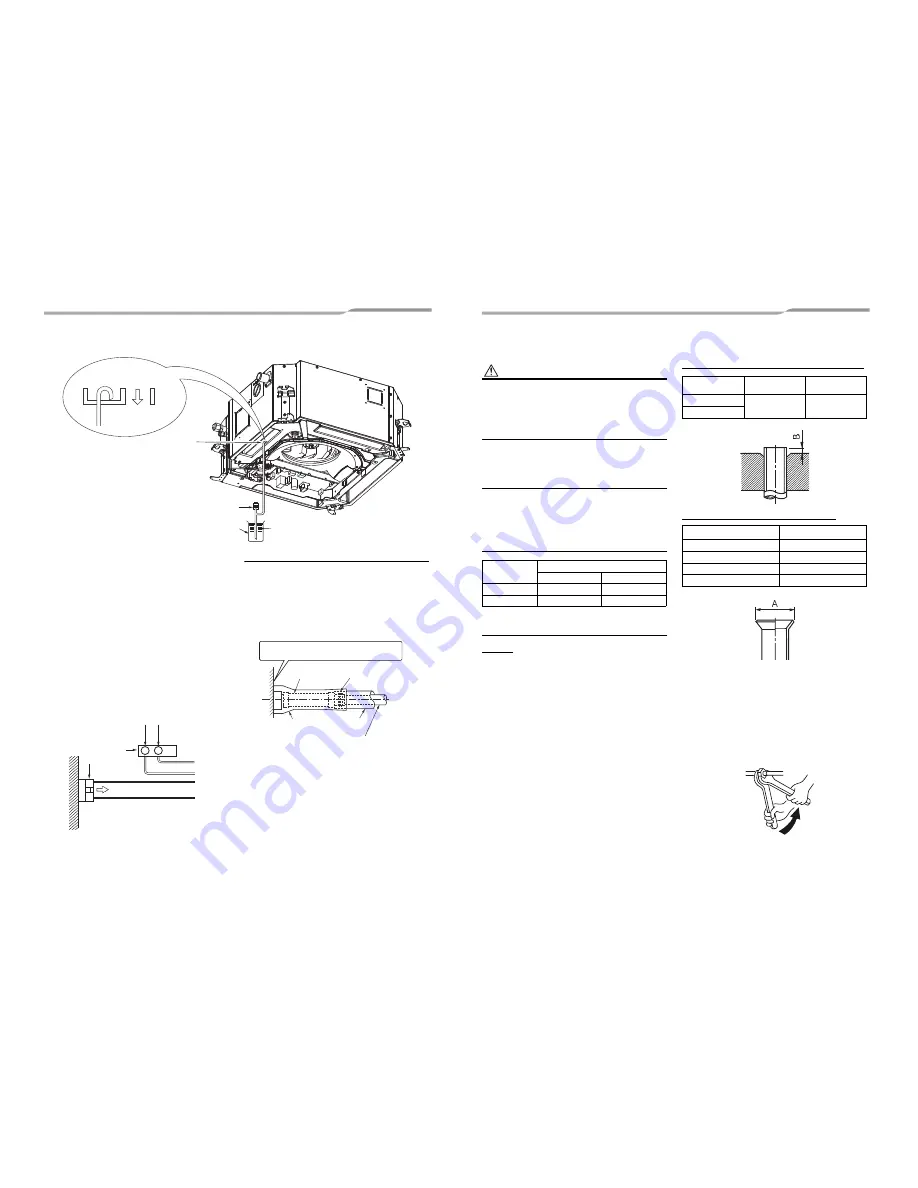
– 10 –
• After the electric work has finished, pour water
during COOL mode operation.
• If the electric work has not yet finished, pull out the
float switch connector (CN34: Red) from the
electrical control box, and check draining by plugging
the single phase 220 - 240 V power to the terminal
blocks R(L) and S(N).
If doing so, the drain pump motor operates.
• Test water drain while checking the operation sound
of the drain pump motor.
(If the operation sound changes from continuous
sound to intermittent sound, water is normally
drained.)
After the check, the drain pump motor runs,
connecting the float switch connector.
(In case of check by pulling out the float switch
connector, return the connector to the original
position.)
Perform heat insulating
• As shown in the figure, cover the flexible hose and
hose band with the attached heat insulator up to the
bottom of the indoor unit without gap.
• Cover the drain pipe seamlessly with a heat insulator
to be procured locally so that it overlaps with the
attached heat insulator of the drain connecting
section.
* Direct the slits and seams of the heat insulator
upward to avoid water leakage.
Air
discharge area
Insert the leading part of the hose
between the heat exchanger and
the drain pan, and then bend it
downward.
Polyethylene hand pump for
pouring water in drain pan
Water (1500 cc to 2000 cc)
Vessel
Drain pan
L
N
Pull out connector CN34 (Red)
from P.C. board.
CN34
(RED)
Black
Black
Red
White
Power
terminals
220 - 240 V, 50 Hz
220 V, 60 Hz
Wrap the attached heat insulator seamlessly from
the surface of the indoor unit.
Flexible hose
Hose band
Attached heat
insulator
Heat insulator to be
procured locally
Hard vinyl chloride pipe
6
Refrigerant piping
CAUTION
When the refrigerant pipe is long, provide support
brackets at intervals of 2.5 m to 3 m to clamp the
refrigerant pipe. Otherwise, abnormal sound may be
generated.
Use the flare nut attached with the indoor unit or R410A
flare nut.
Permissible piping length and
height difference
They vary depending on the outdoor unit. For details,
refer to the Installation Manual attached to the outdoor
unit.
Pipe size
Connecting refrigerant piping
Flaring
1. Cut the pipe with a pipe cutter.
Remove burrs completely. (Remaining burrs may
cause gas leakage.)
2. Insert a flare nut into the pipe, and flare the pipe.
Use the flare nut provided with the unit or the one
used for the R410A refrigerant. The flaring
dimensions for R410A are different from the ones
used for the conventional R22 refrigerant. A new
flare tool manufactured for use with the R410A
refrigerant is recommended, but the conventional
tool can still be used if the projection margin of the
copper pipe is adjusted to be as shown in the
following table.
Projection margin in flaring: B (Unit: mm)
Flaring diameter size: A (Unit: mm)
* In case of flaring for R410A with the conventional
flare tool, pull it out approx. 0.5 mm more than that
for R22 to adjust to the specified flare size. The
copper pipe gauge is useful for adjusting projection
margin size.
• The sealed gas was sealed at the atmospheric
pressure so when the flare nut is removed, there will
no “whooshing” sound: This is normal and is not
indicative of trouble.
• Use two wrenches to connect the indoor unit pipe.
RAV-SM
Pipe size(mm)
Liquid side
Gas side
SM30
Ø6.4
Ø9.5
SM40, 45, 56
Ø6.4
Ø12.7
Outer dia. of
copper pipe
R410A tool used
Conventional
tool used
6.4, 9.5
0 to 0.5
1.0 to 1.5
12.7, 15.9
Outer dia. of copper pipe
A
+0
–0.4
6.4
9.1
9.5
13.2
12.7
16.6
15.9
19.7
Work using double spanner
19-EN
20-EN
Summary of Contents for RAV-SM404MUT-E
Page 24: ...EH99885797 ...
Page 48: ...EH99885797 ...
Page 72: ...EH99885797 ...
Page 96: ...EH99885797 ...
Page 120: ...EH99885797 ...
Page 144: ...EH99885797 ...
Page 168: ...EH99885797 ...
Page 192: ...EH99885797 ...
Page 216: ...EH99885797 ...
Page 240: ...EH99885797 ...
Page 264: ...EH99885797 ...
Page 288: ...EH99885797 ...