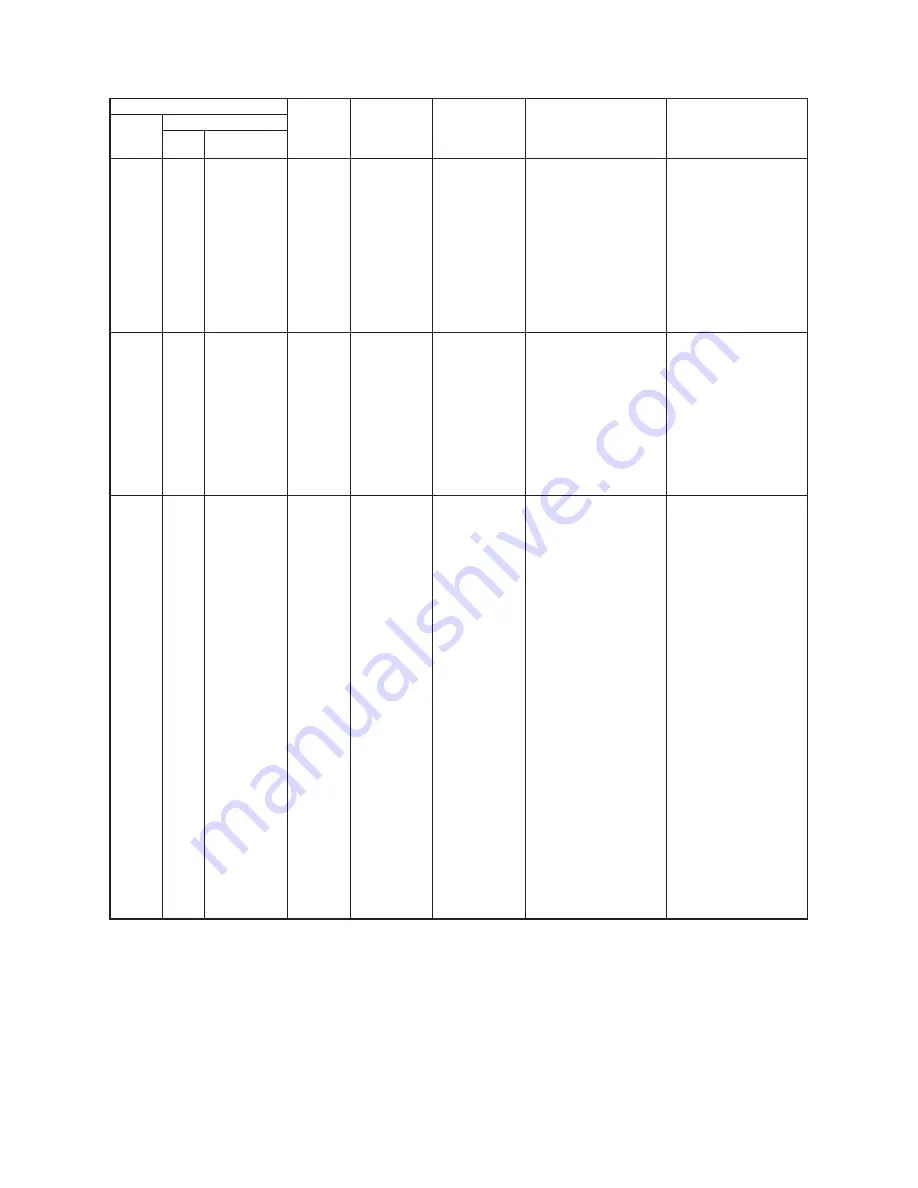
– 58 –
Check code
Location
of
detection
Description
System status
Error detection
condition(s)
Check items (locations)
Main
remote
controller
Outdoor 7-segment display
Check
code
Sub-code
• Check outdoor service
valves (gas side, liquid
side) to confirm full opening.
• Check outdoor PMVs
(PMV1, 2, 4) for clogging.
• Check resistance
characteristics of TD3
sensor.
• Check for defect in 4-way
valve.
• Check SV43 circuit for
leakage.
• Check SV4 circuit (for wiring
or installation error involving
SV41, SV42 and SV43).
I/F
—
Discharge
temperature
TD3 error
All stop
Discharge temperature
(TD3) exceeds 115 ˚C.
P18
P18
• Check for defect in main
body of 4-way valve.
• Check for coil defect in 4-
way valve and loose
connection of its connector.
• Check resistance
characteristics of TS1 and
TE1 sensors.
• Check output voltage
characteristics of Pd and
Ps pressure sensors.
• Check for wiring error
involving TE1 and TL
sensors.
I/F
Detected
outdoor unit No.
4-way valve
reversing error
All stop
Abnormal refrigerating cycle
data is collected during
heating operation.
P19
P19
• Check for defect in Pd
pressure sensor.
• Check service valves (gas
side, liquid side) to confirm
full opening.
• Check for defect in outdoor
fan.
• Check for defect in outdoor
fan motor.
• Check outdoor PMVs
(PMV1, 2, 4) for clogging.
• Check indoor / outdoor
heat exchangers for
clogging.
• Check for short-circuiting
of outdoor suction /
discharge air flows.
• Check SV2 circuit for
clogging.
• Check for defect in outdoor
P.C. board (I/F).
• Check for defect in indoor
fan system (possible cause
of air flow reduction).
• Check opening status of
indoor PMV.
• Check indoor-outdoor
communication line for
wiring error.
• Check for faulty operation
of check valve in discharge
pipe convergent section.
• Check gas balancing SV4
valve circuit.
• Check SV5 valve circuit.
• Check for refrigerant
overcharging.
I/F
—
Activation of
high-pressure
protection
All stop
Pd sensor detects pressure
equal to or greater than
3.6 MPa.
P20
P20
Indoor unit (including Hot Water Module)