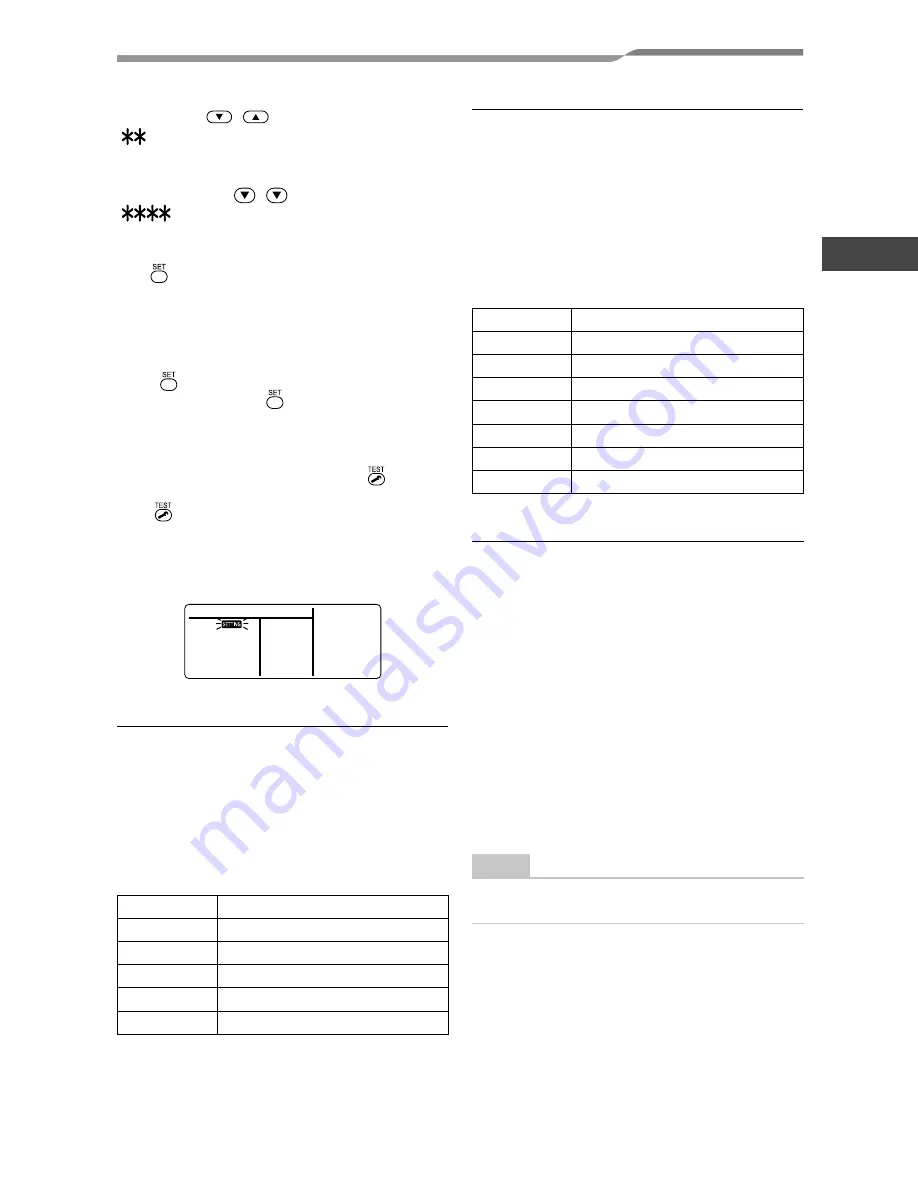
GR
NL
PT
ES
IT
DE
FR
RU
SI
SK
LV
CS
TR
EN
21-EN
Installation Manual
–21–
Toshiba 1112750201 (EN)
Change of lighting time of fi lter sign
According to the installation condition, the lighting
time of the fi lter sign (Notifi cation of fi lter cleaning)
can be changed.
Follow to the basic operation procedure
(
1
→
2
→
3
→
4
→
5
→
6
) .
• For the CODE No. in Procedure
3
, specify [01].
• For the [SET DATA] in Procedure
4
, select the SET
DATA of fi lter sign lighting time from the following
table.
To secure better effect of heating
When it is diffi cult to obtain satisfactory heating due to
installation place of the indoor unit or structure of the
room, the detection temperature of heating can be
raised. Also use a circulator, etc. to circulate heat air
near the ceiling.
Follow to the basic operation procedure
(
1
→
2
→
3
→
4
→
5
→
6
) .
• For the CODE No. in Procedure
3
, specify [06].
• For the SET DATA in Procedure
4
, select the SET
DATA of shift value of detection temperature to be set
up from the table below.
Procedure
3
Using “TEMP.”
/
buttons, specify CODE No.
[
].
Procedure
4
Using timer “TIME.”
/
buttons, select SET DATA
[
].
Procedure
5
Push
button. When the display changes from fl ashing
to lit, the setup is completed.
• To change settings of another indoor unit, repeat from
Procedure
2
.
• To change other settings of the selected indoor unit,
repeat from Procedure
3
.
Use button to clear the settings.
To make settings after
button was pushed, repeat
from Procedure
2
.
Procedure
6
When settings have been completed, push
button to
determine the settings.
When
button is pushed, “SETTING” fl ashes and then
the display content disappears and the air conditioner
enters the normal stop mode.
(While “SETTING” is fl ashing, no operation of the
remote controller is accepted.)
SET DATA
Filter sign lighting time
0000
None
0001
150H (Factory setting)
0002
2500H
0003
5000H
0004
10000H
SET DATA
Detection temp shift value
0000
No shift
0001
+1°C
0002
+2°C
0003
+3°C (Factory setting)
0004
+4°C
0005
+5°C
0006
+6°C
Group control
In a group control, a remote controller can control
up to maximum 8 units.
• The wired remote controller only can control a group
control. The wireless remote controller is unavailable
for this control.
• For cabling procedure and cables of the individual line
(Identical refrigerant line) system, refer to “Electric
work” in this Manual.
• Cabling between indoor units in a group is performed
in the following procedure.
Connect the indoor units by connecting the remote
controller inter-unit cables from the remote controller
terminal blocks (A, B) of the indoor unit connected
with a remote controller to the remote controller
terminal blocks (A, B) of the other indoor unit.
(Non-polarity)
• For address setup, refer to the Installation Manual
attached to the outdoor unit.
NOTE
Net work adapter (Model TCB-PCNT20E) can not
connect to this air conditioner.
Summary of Contents for MML-AP0074NH-E
Page 2: ......