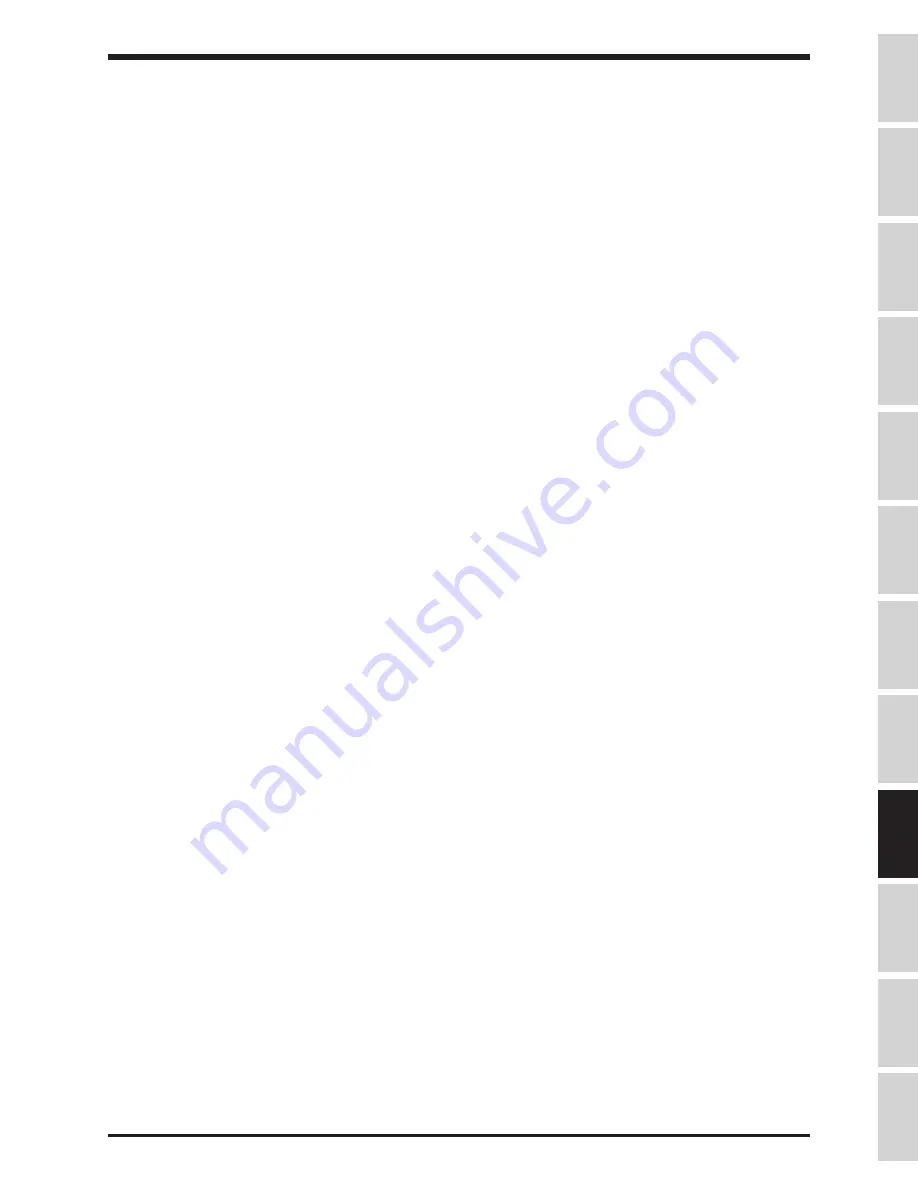
TOSHIBA
9 - 24
Parameter Explanations (cont'd)
Item 275,
FM TERMINAL FUNCTION SELECTION
(con't) - Choices for "FM" terminal's signal's
function:
0: (default for "FM"). Pre-compensation reference frequency. This is the drive's internal
frequency command and is affected by acc/dec and PID and droop (same as the actual output
frequency displayed on the drive's keypad).
1: Post-compensation output frequency may be higher than frequency command (drive
overspeeds to compensate for slip in vector control).
2: Frequency command. Use for master/follower. Not affected by stopping or accel/decel.
3: (default for "AM"). Output current. (output amps)
2
=(torque amps)
2
+(excitation amps)
2
4: DC bus voltage
5: Output voltage
6: Torque current. (output current)
2
= (torque current)
2
+ (excitation current)
2
7:
Excitation current
. (output current)
2
= (torque current)
2
+ (excitation current)
2
8: PID feedback value. This is the frequency represented by the feedback signal
9: Motor overload ratio. Example: H3 is rated for 150% FLA for 2 minutes. If H3 runs at
150% for 1 minute, this output will be 50%. Drive trips when ration hits 100%.
10: Inverter overload ratio. See example for selection 9 above.
11: Dynamic braking resistor overload ratio. See example for selection 9 above.
12: Input power (watts)
13: Output power (watts)
14: Meter calibration setting
15: Peak output current. Peak is reset by cycling power, initiating a run, or resetting drive.
16: Peak input voltage. Peak is reset by cycling power, initiating run, or resetting drive.
Calculated from DC bus.
Item 276,
FREQUENCY METER ADJUSTMENT
- This setting adjusts the gain of the "FM" terminal. With
Item 275 set to "14" (or Item 277 for the "AM" terminal), press the up/down arrows (ignoring parameter
value shown) until external meter/system reads the following value for the chosen operating variable:
For
post compensation frequency, adjust until meter/system reads 75% of Item 1,
MAXIMUM
OUTPUT FREQUENCY
For
post-compensation output frequency, adjust until meter/system reads 75% of Item 1,
MAXIMUM OUTPUT FREQUENCY
For
frequency command, adjust until meter/system reads 75% of Item 1,
MAXIMUM OUTPUT
FREQUENCY
For
output current, adjust until meter/system reads drive rated amps (or 100%)
For
DC bus voltage, adjust until meter/system 283 VDC for a 230 V drive or 566 VDC for a 460 V
drive.
For
output voltage, adjust arrows until meter/system reads 200 VAC (or 100%) for a 230 V drive
or 400 VAC (or100%) for a 460 V drive.
For
torque current, adjust arrows until meter/system reads drive rated amps (or 100%).
For
excitation current, adjust arrows until meter/system reads drive rated amps (or 100%).
For
PID feedback value, adjust arrows until meter/system reads 75% of Item 1,
MAXIMUM
OUTPUT FREQUENCY.
For
motor overload ratio, adjust arrows until meter/system reads 100%.
For
inverter overload ratio, adjust arrows until meter/system reads 100%.
For
dynamic braking resistor overload ratio, adjust arrows until meter/system reads 100%.
For
input power, adjust arrows until meter/system reads 346 X drive FLA for a 230 V drive or 692
X drive FLA for a 460 V drive.
For
output power, adjust arrows until meter/system reads 346 X drive FLA for a 230 V drive or
692 X drive FLA for a 460 V drive.
For
peak output current, adjust arrows until meter/system reads drive rated amps (or 100%).
For
peak input voltage, adjust arrows until meter/system reads 200 VAC for a 230 V drive or 400
VAC for a 460 V drive.
Specifications
Precautions
Wiring
Jumpers
Panel
Keypad
Parameters
Programming
Service
Dimensions
Index
Inspection
Summary of Contents for Adjustable Speed Drive H3
Page 1: ...March 2008 Part 46687 004 ...
Page 2: ......