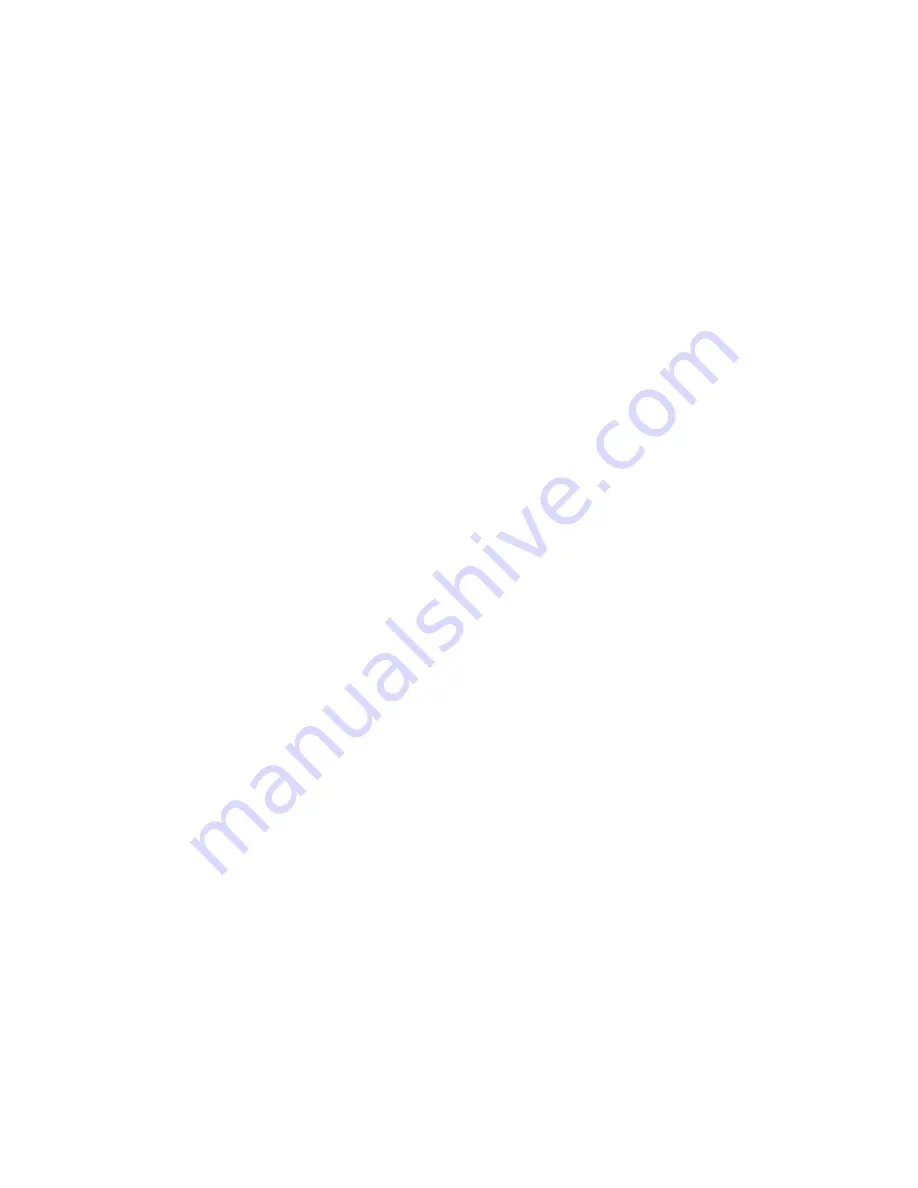
Specifications and Maintenance: Torque Specifications
Page 2–14
4000 Series Z MASTER® Service Manual
3442-427 Rev A
Summary of Contents for Z Master 4000 Series
Page 2: ...Revision History Revision History Page 2 4000 Series Z MASTER Service Manual 3442 427 Rev A...
Page 6: ...Preface Page 6 4000 Series Z MASTER Service Manual 3442 427 Rev A...
Page 108: ...Electrical Service and Repairs Page 8 14 4000 Series Z MASTER Service Manual 3442 427 Rev A...
Page 111: ...Drawing Rev A Sheet 1 3442 427 Rev A Page A 3 Electrical Schematic g342795...
Page 112: ...Page A 4 3442 427 Rev A Drawing Rev Sheet Electrical PTO Engaged Schematic g346038...
Page 113: ...Drawing Rev Sheet 3442 427 Rev A Page A 5 Electrical Run Position g346039...
Page 114: ...Page A 6 3442 427 Rev A Drawing Rev Sheet Electrical Start Position g346040...