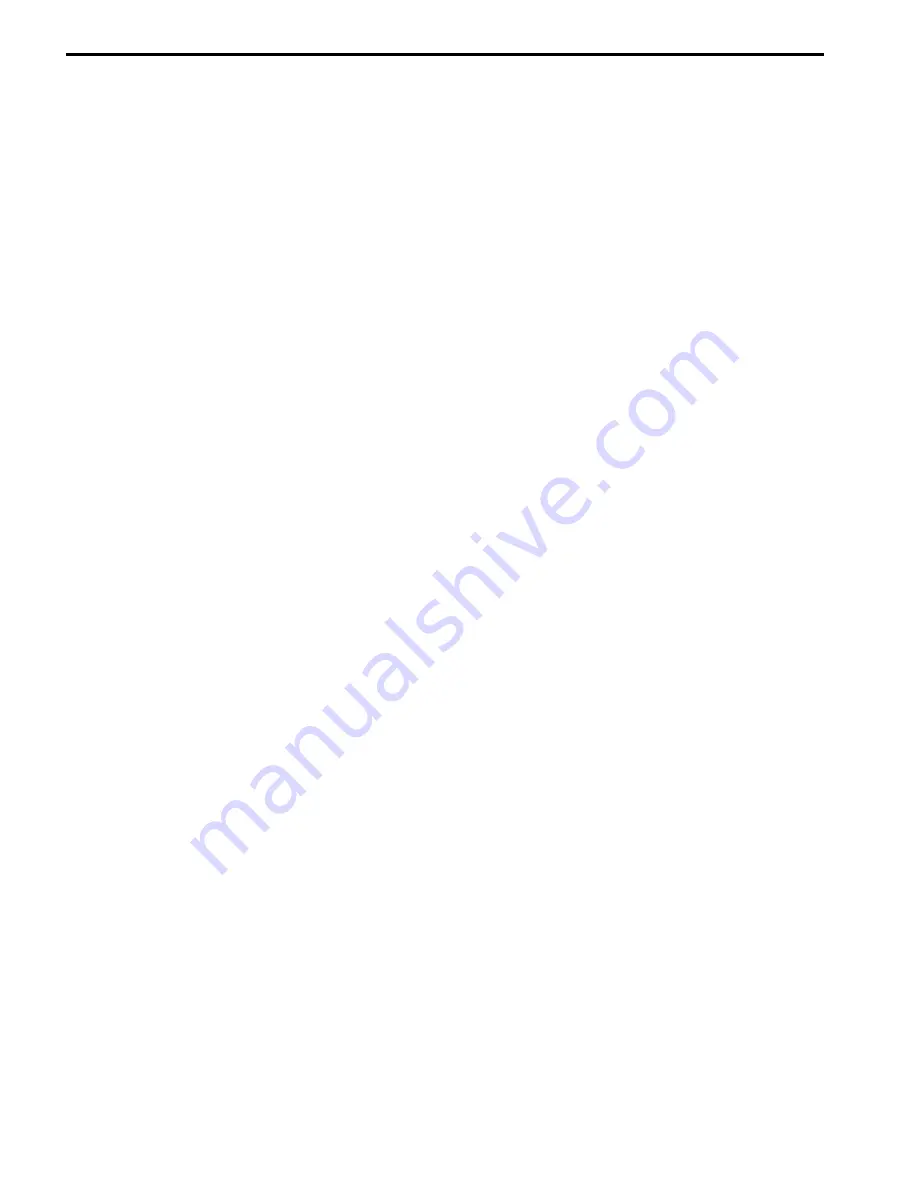
Lower Cutting Units / Mow
The hydraulic pump that provides oil flow to the reel
drive circuit is driven off the PTO output shaft of the
hydrostatic transmission. This oil flow enters a control
valve block which directs the oil flow to perform the
functions of reel drive and cutting unit lift and lower.
The valve block consists of two individual control cir
cuits. Each circuit is supplied by its own pump section
– “P1” and “P2”. The only common connection from one
circuit to the other is the case drains from the motors
and the tank ports from all valves.
To lower the cutting units, solenoid valves “S3”, “S4”,
and “S5” must be energized along with “S6”. Valve “S6”
is a load holding poppet-type valve. If “S6” is not ener
gized, no cutting units will lower. Valve “S7” must be in
its normal de-energized position to allow the return oil
from the cylinder circuit to be directed to tank.
On the “P1” pump circuit, maximum system pressure is
limited by relief valve “R1” which is set at 3000 PSI.
System pressure on the “P1” side can be measured at
Port “G1”. Total pump flow must go through solenoid
valve “S7”. In its normal de-energized position, valve
“S7” directs pump flow to the front reel circuit. Solenoid
valve “S1” must be energized to allow pressure to build
in the front reel circuit. When solenoid valve “S1” is
energized, variable solenoid valve “VS1” will direct part
of the pump flow to tank, while directing the remaining
flow to solenoid valve “S8” and out to the front reel
motors. Valve “VS1” is adjusted by the electronic control
unit (ECU) with a variable duty cycle pulse-width-modu-
lated (PWM) voltage. As the PWM duty cycle is in
creased, less oil is by-passed to tank, causing more oil
to go to the reel motors. When “VS1” is fully energized,
no flow by-passes to tank and all flow is routed to the
reel motors. In its normal de-energized position, sole
noid valve “S8” directs flow from “VS1” to the front reel
motors to turn them in a forward or “mow” direction.
Return oil from the motors is directed to tank through
valve “S8”.
On the “P2” pump circuit, maximum system pressure is
limited by relief valve “R2”, which is set at 2000 PSI. This
pressure can be monitored at port “G2”. Solenoid valve
“S2” must be energized to allow pressure to build in the
rear reel circuit. The variable solenoid valve “VS2” con
trols reel speed and functions the same as “VS1”. In its
normal de-energized position, solenoid valve “S9” di
rects flow from “VS2” to the front reel motors to turn them
in a forward or “mow” direction. Return oil from the
motors is directed to tank through valve “S9”.
NOTE: The variable solenoid valves, “VS1” and “VS2”,
are energized with a pulse-width-modulated (PWM)
voltage during most mowing or backlapping operations.
Only when the reel speed control is set to full speed
(position A), are the valves energized with a full 12 volts.
Hydraulic Flow Diagrams
Page 4 - 8
Reelmaster
®
5100-D
Summary of Contents for Reelmaster 5100-D
Page 2: ...This page is blank ...
Page 4: ...This page is blank ...
Page 8: ...Safety Instructions Page 1 4 Reelmaster 5100 D ...
Page 12: ...Maintenance Interval Chart Maintenance Interval Chart Page 2 4 Rev A Reelmaster 5100 D ...
Page 32: ...Troubleshooting Page 3 16 Reelmaster 223 D 5100 D ...
Page 33: ...Reelmaster 223 D 5100 D Page 3 17 Troubleshooting ...
Page 86: ...Specifications Page 4 2 2 Reelmaster 5100 D ...
Page 90: ...Hydraulic Schematic Rev A Hydraulic Schematic Page 4 6 Reelmaster 5100 D ...
Page 154: ...Logic Chart Page 5 2 Reelmaster 5100 D ...
Page 155: ...Wiring Schematic S N Below 51001 Rev B Reelmaster 5100 D Page 5 3 Wiring Schematic ...
Page 206: ...Repairs Page 5 48 Rev A Reelmaster 5100 D ...
Page 230: ...Repairs Page 6 24 Reelmaster 5100 D ...
Page 304: ...Repairs Page 8 22 Reelmaster 223 D 5100 D 5300 D ...
Page 317: ...This page is blank ...