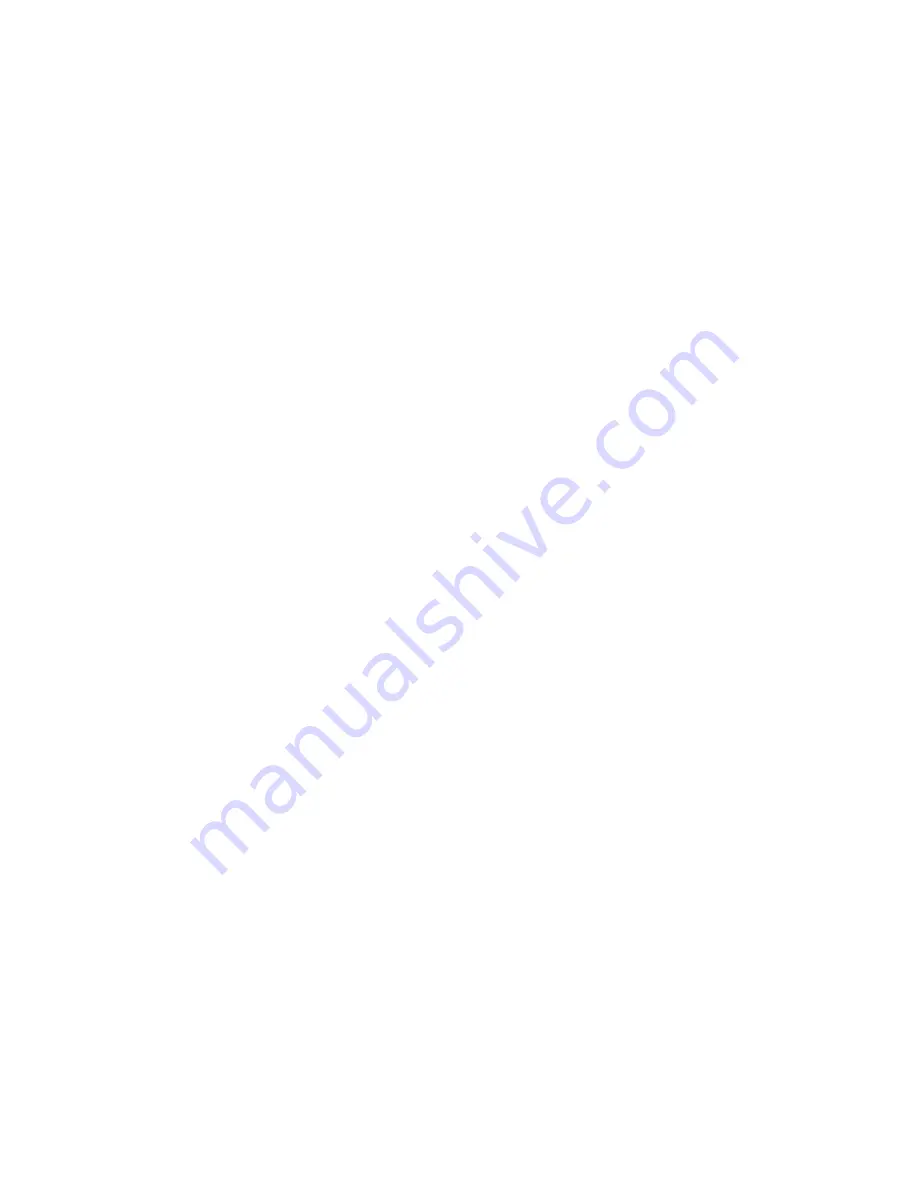
3. Secure the flange end of the pump (Fig. 88, Item 23)
in a vise with the drive shaft (Item 24) pointing down.
4. Remove the four (4) capscrews (Item 3) and washers
(Item 4).
5. Put your hand on the pump case and gently tap the
pump case with a soft face hammer to loosen the pump
sections. Be careful not to drop parts or disengage gear
mesh.
6. Before removing each gear set, apply marking dye to
mating teeth to retain “timing”. Pump efficiency may be
affected if the teeth are not installed in the same position
during reassembly.
IMPORTANT: To prevent damage to load plates dur
ing pump operation, do not mark gears with a punch
or scribe.
7. Be careful when disassembling. The needle bearings
in the pump body may be of the loose, grease retained
type. Pack these with general purpose grease to retain
them for reassembly. It is recommended NOT to remove
the bearing races. The bearings cannot be serviced
separately. The pump body must be replaced if the
bearings are damaged.
8. Remove the shaft oil seal (Item 22), seal rings (Item
6), load plates (Item 18), pre-load high pressure seals
(Item 16) and high pressure seals (Item 17) while dis
assembling the pump.
9. Clean all parts. Check all parts for burrs, scoring,
nicks and other damage. Check the bushings in the
plate assemblies (Items 15 and 25) and cover assembly
(Item 5) for excessive wear or scoring. Replace the
cover or plate assemblies as necessary. The bushings
are not serviceable.
10. Replace load plates if excessively worn or scored.
Replace gears in sets if scored or worn excessively.
11. Apply oil to inside of gear plates and bushings. Apply
grease or petroleum jelly to load seals and load plates
before installing.
12. Assemble pump sections starting at body end
(Item 23). Apply grease or petroleum jelly to new seal
rings (Item 6) before installing.
13. After pump has been assembled, tighten capscrews
by hand. Rotate the drive shaft to check for binding.
Protect the shaft if using a pliers.
14. Tighten the capscrews evenly in a crossing pattern
to a torque of 25 ft-lb.
15. Before installing new oil seal (Item 22), make sure
seal bore and shaft on pump are clean and free of
foreign material.
16. Put seal protector tool on pump shaft or apply thin
plastic or tape on the shaft to protect the seal from
damage.
17. Before installing seal, fill volume between lips of new
seal with Master Lubricant Co. “Lubrico M-6", Lubriplate
”Aero Lube" or equivalent. Apply grease or petroleum
jelly to inside diameter of new oil seal. Carefully install
new oil seal with lip of seal toward pump body.
Mowing Circuit Repairs
Page 4 - 60
Reelmaster
®
5100-D
Summary of Contents for Reelmaster 5100-D
Page 2: ...This page is blank ...
Page 4: ...This page is blank ...
Page 8: ...Safety Instructions Page 1 4 Reelmaster 5100 D ...
Page 12: ...Maintenance Interval Chart Maintenance Interval Chart Page 2 4 Rev A Reelmaster 5100 D ...
Page 32: ...Troubleshooting Page 3 16 Reelmaster 223 D 5100 D ...
Page 33: ...Reelmaster 223 D 5100 D Page 3 17 Troubleshooting ...
Page 86: ...Specifications Page 4 2 2 Reelmaster 5100 D ...
Page 90: ...Hydraulic Schematic Rev A Hydraulic Schematic Page 4 6 Reelmaster 5100 D ...
Page 154: ...Logic Chart Page 5 2 Reelmaster 5100 D ...
Page 155: ...Wiring Schematic S N Below 51001 Rev B Reelmaster 5100 D Page 5 3 Wiring Schematic ...
Page 206: ...Repairs Page 5 48 Rev A Reelmaster 5100 D ...
Page 230: ...Repairs Page 6 24 Reelmaster 5100 D ...
Page 304: ...Repairs Page 8 22 Reelmaster 223 D 5100 D 5300 D ...
Page 317: ...This page is blank ...