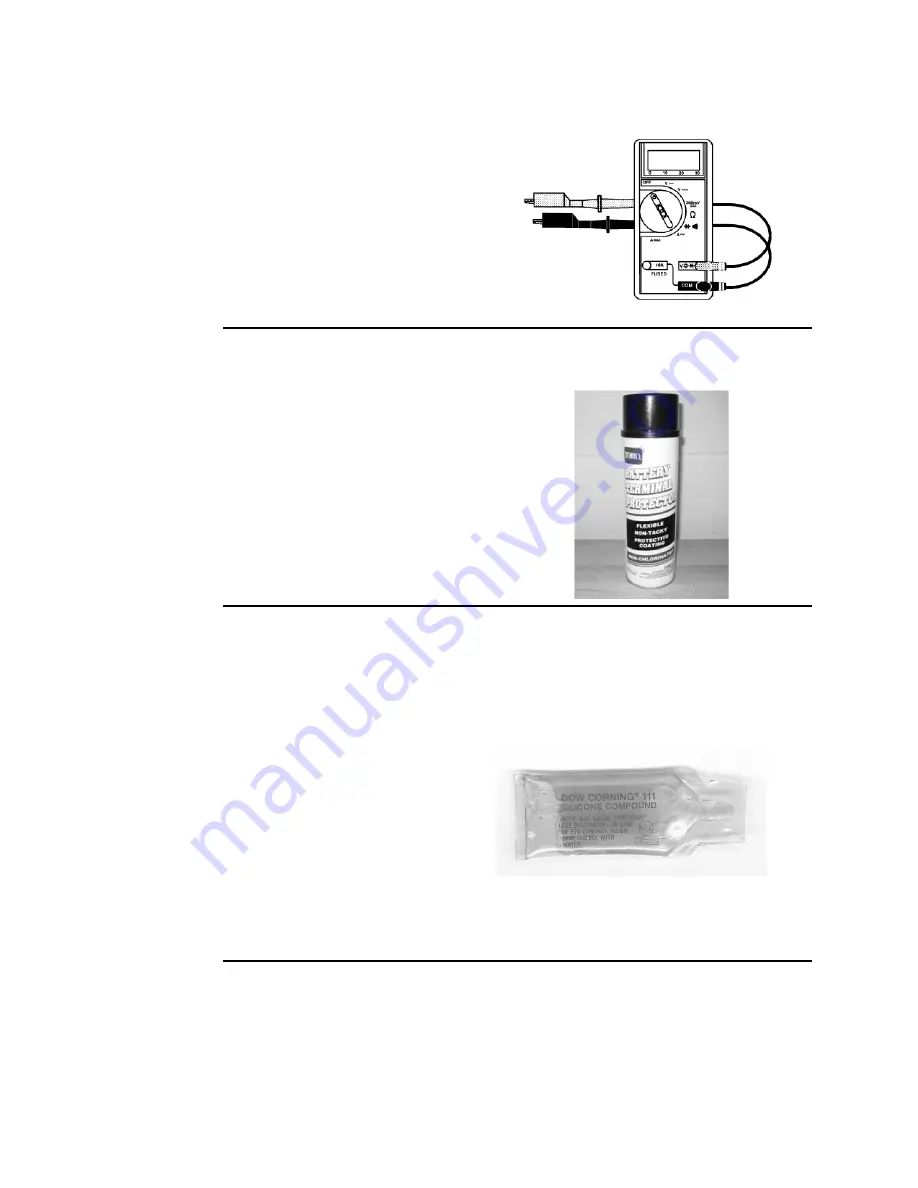
Special Tools
Multimeter
Obtain this tool locally
The meter can test the electrical
components and circuits for current,
resistance, or voltage.
Note:
Use a digital multimeter when
testing the electrical circuits. The high
impedance (internal resistance) of a digital
meter in the voltage mode ensures that
the excess current is not allowed through
the meter. This excess current can
damage the circuits that are not designed
to carry it.
Battery Terminal Protector
Toro Part No. 107-0392
Use this aerosol spray on the battery
terminals, ring terminals, and fork terminals
to reduce corrosion problems. Apply the
terminal protector to the connection after
you secure the battery cable, ring terminal,
or fork terminal.
Dielectric Gel
Toro Part No. 107-0342
Use the dielectric gel to prevent
corrosion of unsealed connection
terminals. To ensure complete
coating of the terminals, liberally
apply the gel to the component
and wire harness connector, plug
the connector into the component,
disconnect the connector, apply
the gel to both surfaces again, and
connect the harness connector
to the component again. The
connectors must be fully packed
with gel for effective results.
Note:
Do not use the dielectric gel
on the sealed connection terminals
as the gel can unseat the connector
seals during assembly.
Specifications and Maintenance: Special Tools
Page 2–12
Pro Force® Debris Blower
18237SL Rev A
Summary of Contents for Pro Force 44552
Page 4: ...Reader Comments Page 4 Pro Force Debris Blower 18237SL Rev A ...
Page 8: ...Preface Page 8 Pro Force Debris Blower 18237SL Rev A ...
Page 28: ...Specifications and Maintenance Special Tools Page 2 14 Pro Force Debris Blower 18237SL Rev A ...
Page 54: ...Engine Service and Repairs Page 4 16 Pro Force Debris Blower 18237SL Rev A ...
Page 98: ...Electrical System Service and Repairs Page 5 44 Pro Force Debris Blower 18237SL Rev A ...