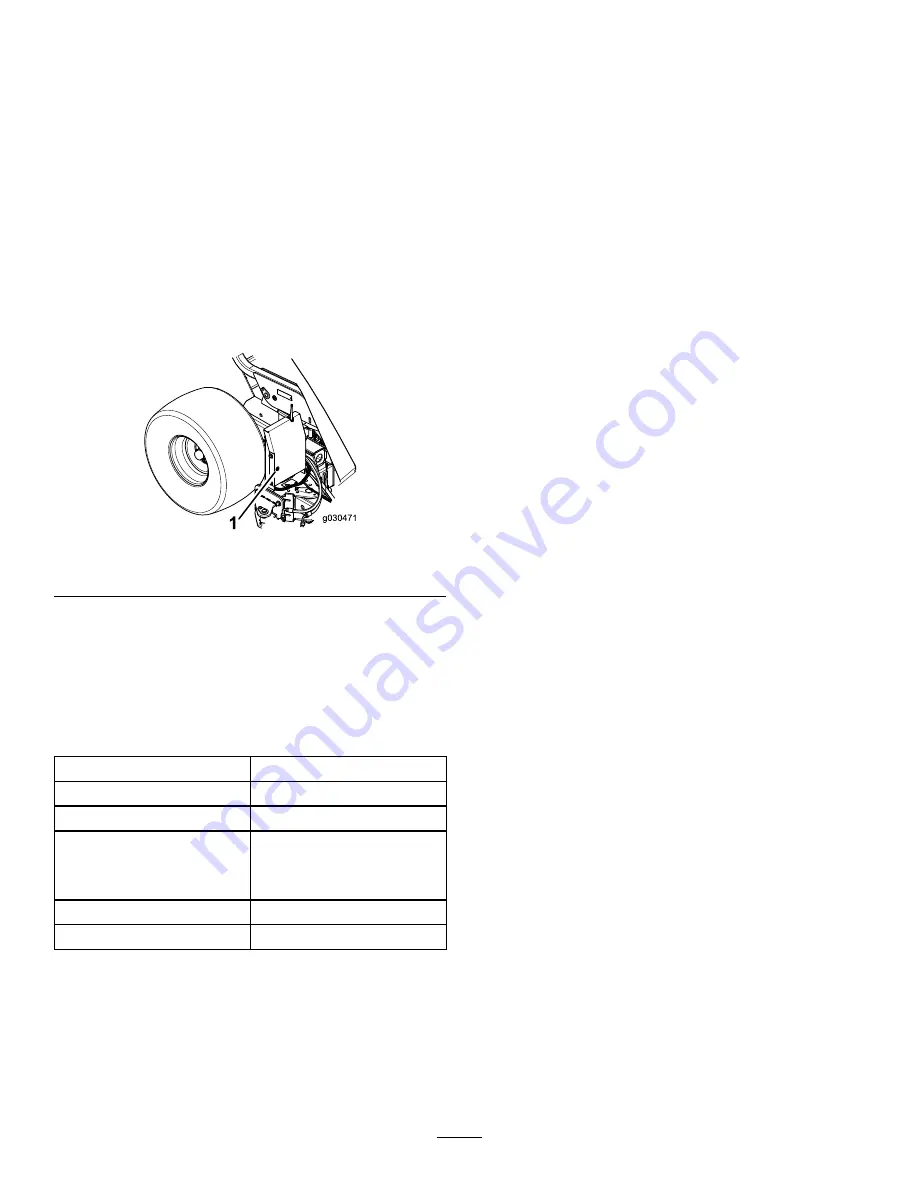
Diagnostic Light
The diagnostic light (
) is located on the front cover
and indicates machine fault codes. After you turn the key
to the R
UN
position, the diagnostic light will illuminate for
5 seconds, turn off for 5 seconds, and then begin flashing
3 times a second until you push a button on the handheld
remote. If the light turns on for 5 seconds and then starts
blinking 10 times a second (with or without a 5 second pause)
there is a fault with the machine; refer to
.
Note:
The diagnostic light illuminates when a button is
pushed on the handheld remote.
Note:
If you have a button depressed on the handheld
remote when you start the machine, the light will not flash 3
times a second after it turns off for 5 seconds.
Figure 18
1.
Diagnostic light
Specifications
Note:
Specifications and design are subject to change
without notice.
Dimensions and Weights
Width
221 cm (87 inches)
Height
202 cm (79-1/2 inches)
Dump height clearance
173 cm (68 inches)
Length
Hopper lowered -
173 cm (68 inches)
Hopper raised - 229-249
cm (90-98 inches)
Empty weight
680 kg (1500 lb)
Gross vehicle weight (GVW)
1588 kg (3500 lb)
Attachments/Accessories
A selection of Toro approved attachments and accessories is
available for use with the machine to enhance and expand
its capabilities. Contact your Authorized Service Dealer or
Distributor or go to www.Toro.com for a list of all approved
attachments and accessories.
18
Summary of Contents for 07068
Page 34: ...Notes 34...