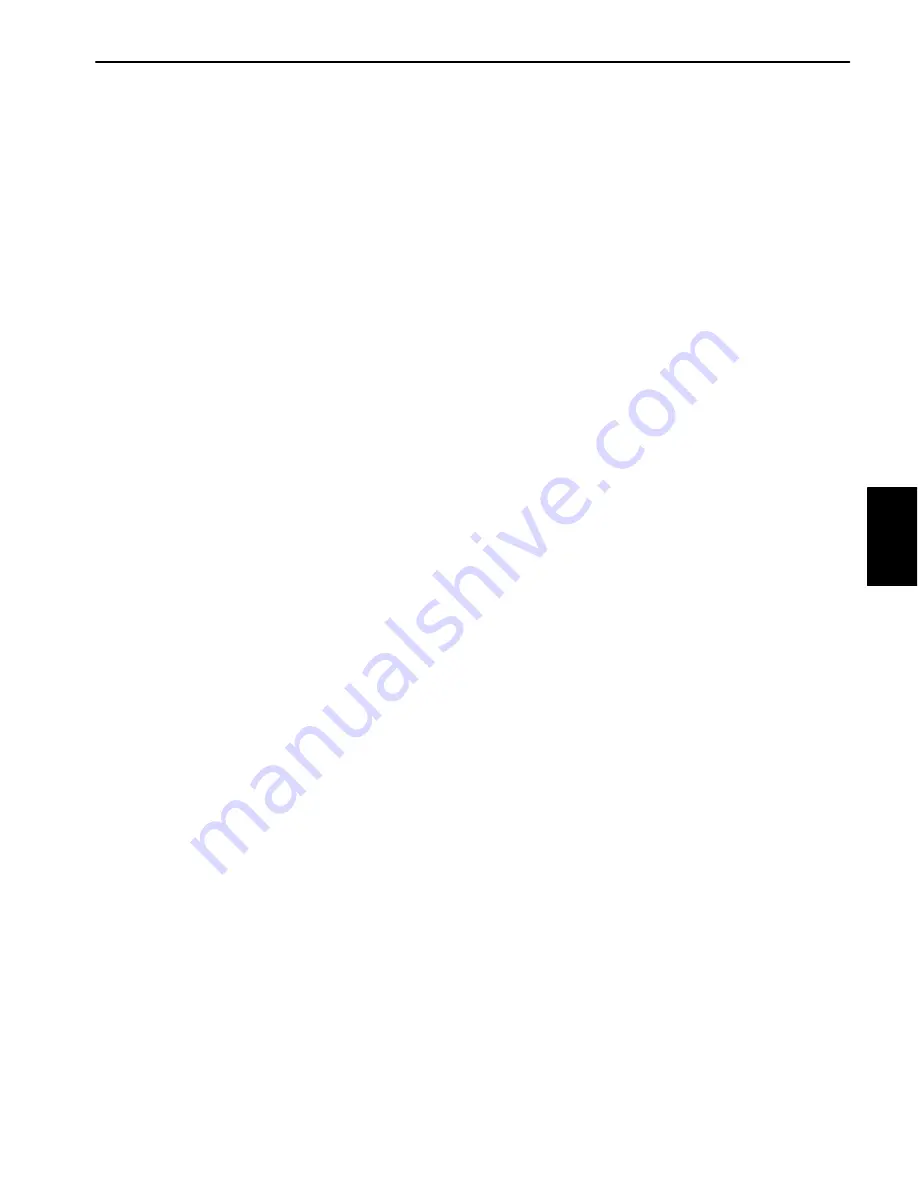
Reelmaster 7000−D
Hydraulic System
Page 5 − 13
Traction Circuit: LOW Speed (Mow)
The traction circuit piston pump is a variable displace-
ment pump that is directly coupled to the engine fly-
wheel. Pushing the traction pedal engages a hydraulic
servo valve which controls the variable displacement
piston pump swash plate to create a flow of oil. Traction
circuit oil is directed to the dual displacement front wheel
motors and rear axle motor. Operating pressure on the
high pressure side of the closed loop traction circuit is
determined by the amount of load developed at the
wheel motors and rear axle motor. As the traction load
increases, circuit pressure can increase to the relief
valves setting of 5000 PSI (345 bar) in forward or re-
verse. If traction circuit pressure exceeds the relief set-
ting, oil flows through the piston pump relief valve to the
low pressure side of the closed loop traction circuit.
Front wheel motors and the rear axle motor are positive,
dual displacement motors. The dual displacement fea-
ture allows operation in either a LOW (mow) or HI (trans-
port) speed range. The motors are spring biased to
maximum displacement for LOW speeds, and are hy-
draulically shifted to minimum displacement for HI
speeds. The rear axle motor includes a flushing valve to
help cool the traction circuit oil. The valve bleeds off a
small amount of hydraulic oil from the closed loop trac-
tion circuit letting the charge circuit replenish the oil that
is bled from the traction circuit with cooler oil from the
charge circuit.
An optional traction circuit flow divider is available that
equally splits traction pump flow between the front
wheel motors and rear axle motor to prevent excessive
circuit flow going to a spinning wheel. If equipped, the
front traction manifold which includes the flow divider is
mounted to the right side of the front frame.
The piston pump, front wheel motors and rear axle mo-
tor use small amounts of hydraulic fluid for internal lu-
brication. Fluid is designed to leak across traction pump
and motor components into the case drain. This leakage
results in the loss of hydraulic fluid from the closed loop
traction circuit that must be replaced. The charge circuit
is designed to replace this traction circuit leakage. The
gear pump section (P4) that supplies oil to the steering
and lift/lower circuits also provides oil for the charge cir-
cuit.
Gear pump flow for the charge circuit is directed through
the steering valve, lift manifold, oil filter, and to the low
pressure side of the closed loop traction circuit. Charge
pressure is limited to 207 PSI (14.3 bar) by a check valve
located in the lift manifold.
Forward Direction
With the mow speed limiter in the LOW speed (mow)
position, the solenoid valve in the Hi/Low range manifold
is not energized. The front wheel motors and rear axle
motor are at their maximum displacement when in LOW
speed providing a slower traction speed for mowing
conditions.
When in LOW speed (mow) position with the traction
pedal pushed in the forward direction, oil from the piston
pump is directed to the front wheel motors and rear axle
motor through a parallel system. Oil flow to the front
wheel motors drives the motors in the forward direction
and then returns to the piston pump. Oil flow to the rear
axle motor drives the motor in the forward direction. Oil
returning from the axle motor enters the rear traction
manifold at the M8 port. The majority of the return flow
bypasses the pressure reducing (PR) cartridge and
passes through a less restrictive check valve (CV), out
manifold port P2 and returns to the piston pump.
When going down a hill, the tractor becomes an over−
running load that drives the front wheel and rear axle
motors. In this condition, the rear axle motor could lock
up as the oil pumped from the motor increases pressure
as it returns to the piston pump. To prevent rear wheel
lock up, an adjustable relief valve (RV) in the rear trac-
tion manifold opens to reduce rear axle motor pressure
created in down hill, dynamic braking conditions.
Reverse Direction
The traction circuit operates essentially the same in re-
verse LOW speed (mow) as it does in forward LOW
speed (mow). However, the flow through the circuit is re-
versed. Oil flow from the piston pump is directed to the
front wheel motors and also to the rear traction manifold.
The oil to the front wheel motors drives them in the re-
verse direction and then returns to the piston pump. The
oil to the rear traction manifold enters the manifold at
port P2 and flows through pressure reducing valve (PR)
which limits the down stream pressure to the rear axle
motor to 400 PSI (27.6 bar) so the rear wheels will not
scuff the turf during reverse operation. This reduced
pressure flow is directed out rear traction manifold port
M8 to drive the rear axle motor in reverse. Return oil
from the rear motor returns to the piston pump.
Hydraulic
System
Summary of Contents for 03781
Page 1: ...Form No 15214SL Rev D Reelmaster 7000 D Models 03780 A and 03781 Original Instructions EN ...
Page 4: ...NOTES _ ...
Page 6: ...Reelmaster 7000 D This page is intentionally blank ...
Page 8: ...Reelmaster 7000 D This page is intentionally blank ...
Page 10: ...Reelmaster 7000 D This page is intentionally blank ...
Page 16: ...Reelmaster 7000 D Page 1 6 Safety This page is intentionally blank ...
Page 40: ...Reelmaster 7000 D Page 3 18 Yanmar Diesel Engine This page is intentionally left blank ...
Page 70: ...Reelmaster 7000 D Page 4 24 Kubota Diesel Engine This page is intentionally blank ...
Page 80: ...Reelmaster 7000 D Hydraulic System Page 5 10 This page is intentionally blank ...
Page 226: ...Reelmaster 7000 D Hydraulic System Page 5 156 This page is intentionally blank ...
Page 230: ...Reelmaster 7000 D Page 6 4 Electrical System This page is intentionally blank ...
Page 337: ...Reelmaster 7000 D Page 8 3 Chassis This page is intentionally blank Chassis ...
Page 349: ...Reelmaster 7000 D Page 8 15 Chassis This page is intentionally blank Chassis ...
Page 354: ...Reelmaster 7000 D Page 8 20 Chassis This page is intentionally blank ...
Page 440: ...Reelmaster 7000 D Universal Groomer Optional Page 11 20 This page is intentionally left blank ...
Page 459: ...Page 12 19 Reelmaster 7000 D Engine Wire Harness Drawing Model 03780 Yanmar Engin ...
Page 461: ...Page 12 21 Reelmaster 7000 D Engine Wire Harness Drawing Model 03781 Kubota Engine ...
Page 463: ...Page 12 23 Reelmaster 7000 D Seat and Console Wire Harness Drawing Model 03780 30781 ...