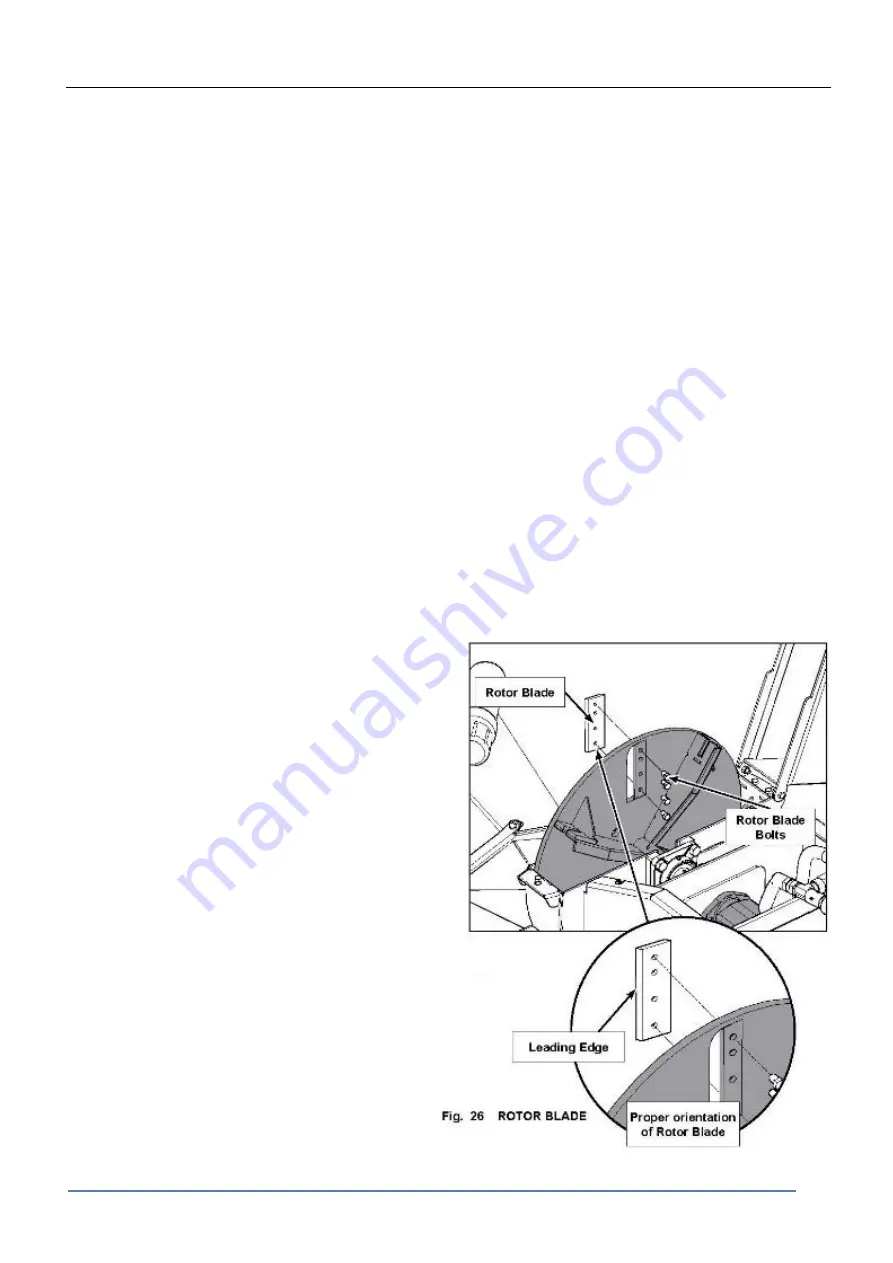
WWW.TMGINDUSTRIAL.COM
18 / 27
dŽůů&ƌĞĞ
:1-887-761-2819
M A I N T E N A N C E
MAINTENANCE
By following a careful service and maintenance program for your machine, you will enjoy many years of
trouble-free operation.
Blade and Breaker Maintenance
The rotor and ledger blades need to be sharp for the Chipper to perform as expected. Periodic inspection is
recommended. Keep the blades sharp to reduce the amount of power required during operation. Watch the
sharpness of the blades when processing material with a lot of sand, soil or dirt mixed with it. Reverse or
sharpen the blades if the cutting edge becomes dull. Twig breaker should be inspected for gouges or bent.
Rotor Blades:
The rotor is equipped with 4 blades spaced evenly to keep the rotor in balance. If one needs to be changed,
the one opposite should also be changed.
It is recommended that the rotor blades be removed from the rotor when sharpening. Always sharpen the
blades at a 45° angle to provide the best cutting effect as it meets the stationary blade. Be sure to tighten the
blade mounting bolts to their specified torque when reinstalling the blades to the rotor.
1.
Turn off the hydraulics, stop the engine,
remove the ignition key, and place it in your
pocket and wait for all moving parts to stop.
2.
Remove the bolt that secures the upper rotor
housing, and carefully open the rotor
housing.
3.
Manually rotate chipper rotor plate so that the
blade is fully exposed
4.
Remove the bolts that hold the rotor blade to
the rotor, remove the blade.
5.
Rotate the blade and reinstall or replace with
new or resharpened blade.