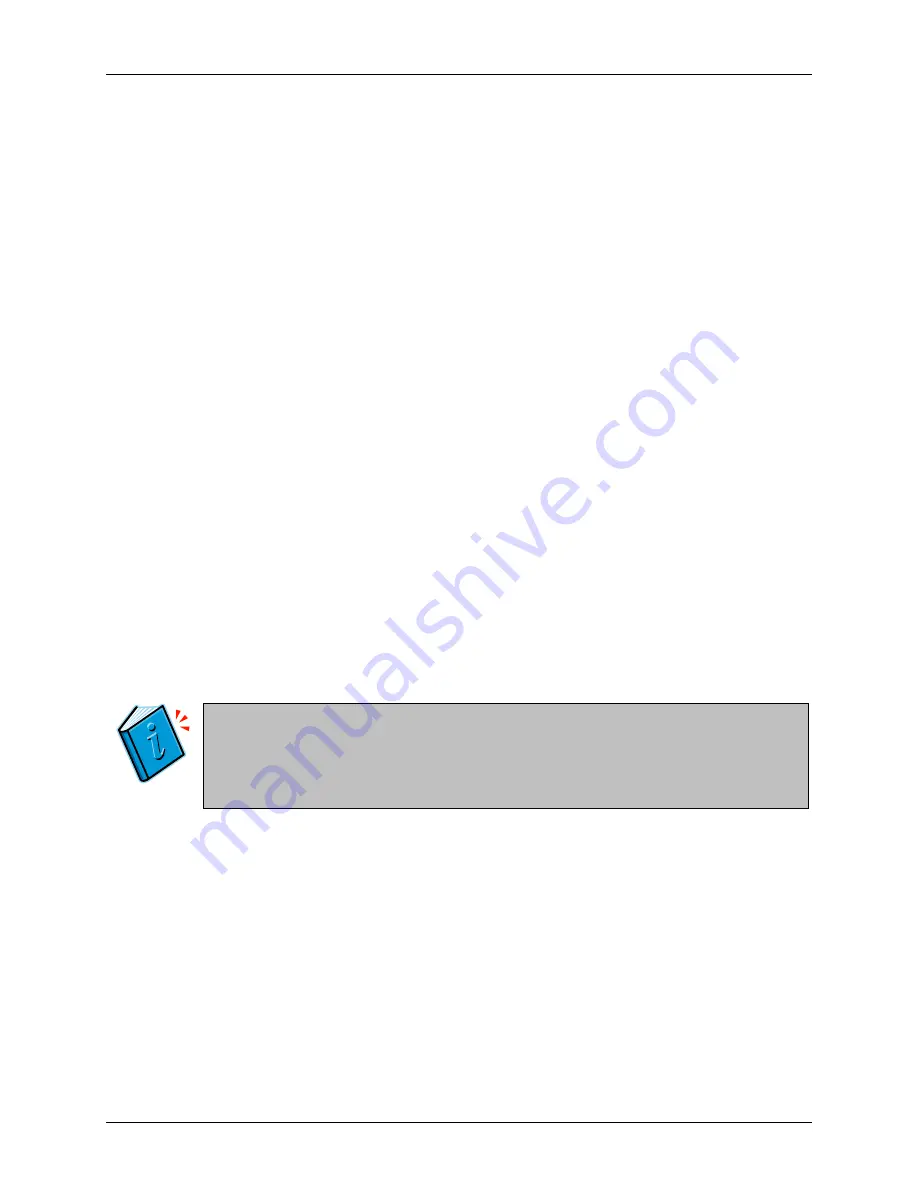
STACIS
2100 Piezoelectric Isolation System - Installation & Operation Manual
P/N 96-28765-01
Page 26 of 43
5.3
Description of Menu Tree Functions
The following sections describe the function of the different options shown above.
5.3.1
Monitoring X, Y, or Z Signals
This menu option allows the monitoring of the control signal sent to the HVAs for the three control axes
(X, Y and Z) for each of the isolators. The signal can be seen on the BNC Output located on the
controller’s front panel. The signal is proportional to the vibration motion being cancelled by the system.
If little or no signal is present on an axis relative to the other system’ axes, this may be an indication of a
damaged vibration sensor. If the signal is too large, it may be an indication that an actuator is damaged
or the floor displacement is too high and the system gains need to be lowered. The Monitor Sig. on BNC
function is used primarily for troubleshooting and monitoring the system’s performance. The output is
immediate when the user selects the axis to monitor.
5.3.2
Monitoring Isolator Loads
As described in the earlier
Installation
section of the manual, this function is used to monitor the loading
of the isolators. It shows the nominal deflection of the internal elastomer mount inside each STACIS
isolator.
5.3.3
Shaker Mode
With this function, STACIS
can be used as a dynamic shaker for vibration testing of equipment. The
shaker function operates in “open loop” mode and can be set for the vertical axis, every 45 degree axis in
the horizontal plane, X Twist (rotation), Y Twist or Z Twist.
“Open Loop” mode disables the vibration isolation function, and uses a signal applied to the controller’s
front-panel BNC Input directly to the PZT stacks in the STACIS
isolators. The resulting displacement of
the payload is proportional to the input at frequencies below 10Hz, but it rolls off quickly at high
frequencies. This mode applies the largest signals to the payload, and
Shaker Mode is ideal for two-channel vibration transfer measurements, etc.
5.3.4
System Diagnostics
This function is a test mode, used only for troubleshooting. It allows the user to test and collect data for
each of the system’s servo loops individually.
In
Manual Mode
, the user is able to inject a known signal into a particular axis (1X through 4Z) through
the controller BNC Input using a signal generator. The controller processes the signal and output a
response through the BNC Output. The signal can be monitored with an oscilloscope.
In
Automatic Mode
, the same checks performed during the power-up sequence are reproduced on the
user selected axis. The response signal can be monitored by connecting an oscilloscope to the
controller’s BNC Output.
The
Upload Data to PC
option allows the user to collect, save and recall data representing the
structural “signature” of the entire assembly (i.e. customer supporting frame, payload and TMC’s isolation
When using the STACIS
system as a shaker, the actuators and/or sensors can
saturate depending on the mode, frequency, and amplitude of input signal. If saturation
occurs, the resultant payload motion will no longer be proportional to the input. TMC
recommends that a reference sensor (such as an accelerometer) is always used to
confirm that the payload motion is correct.